So last time I popped by I was talking about my ring piece. I machined it to suit the location around the rear main seal holder, then cut out another ring piece from the engineering plastic. Harder to cut with the jigsaw than I expected. Put it in the lathe, machined it to the same size as the alloy ring. Machines really nicely. Makes lots of fine mess, much like a very not so tasty candy floss.I then drilled and tapped the alloy ring concentric to the main seal holder on the bell housing backplate. Then drilled the plastic ring, spot facing the holes and bolted it to the alloy ring. I now had an easily replaceable large thrust bearing.
Next was the tricky bit. The crank has about .007" lineal movement on the crank. I wanted to set the thickness of the ring just so there's a smidge less because it will bed in. First I had to get close enough I could start accurately measuring it but I couldn't get in between the back plate and the flywheel to measure in any accurate way. So I used some plastigauge between the flywheel and its hub. Id fit it in place carefully and because the plastic was slightly too thick the plastigauge would show me how much I needed to remove from the thrust face before there was no lineal movement at all when the flywheel bolts were cinched up.
Once I was at that point I could take a skim off the plastic and I ended up with about 5-6 thou movement. Perfect.
Because its an English car, irrespective of what engine is fitted it'll no doubt leak. So in order to help it drip oil properly I added a tiny drain hole below the rear main seal..
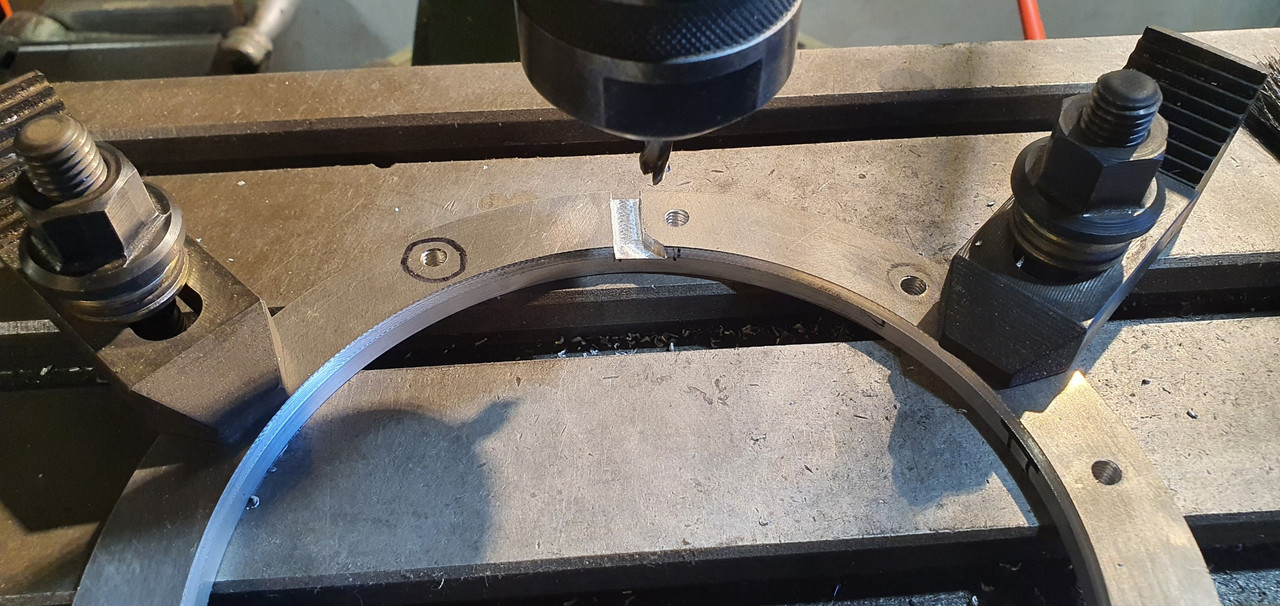
...and a hole in the bottom of the bellhousing. Always horrible having a build up of oil in a bellhousing, flicking all over the clutch etc. Now it can leak gracefully onto a driptray
I put the dust sheet over the block and pulled the cylinder heads out from under the bench. Gave them both a clean as best I could with the valves in place. A nice job to relax into in the afternoon sun...
Heads much cleaner I put one aside and set up shop on the bench to remove the valves and clean them up. I was going to put the bits in an egg tray but it wasn't really ideal so instead a plastic tray with moveable partitions. Very careful not to mix any bits..
The seats and valves were all really good. A bit of carbon build up behind the heads on the exhaust valves but they all cleaned up mint in the lathe with a wire brush. The stems had barely any sign of wear and were jiggle free in the guides. More signs that this engine really is a low mileage, well maintained unit.I made a basic wooden jig to hold the heads at the valve angle so making for an easy time to accurately lap the valve seats clean. They came up sweet with minimal lapping.
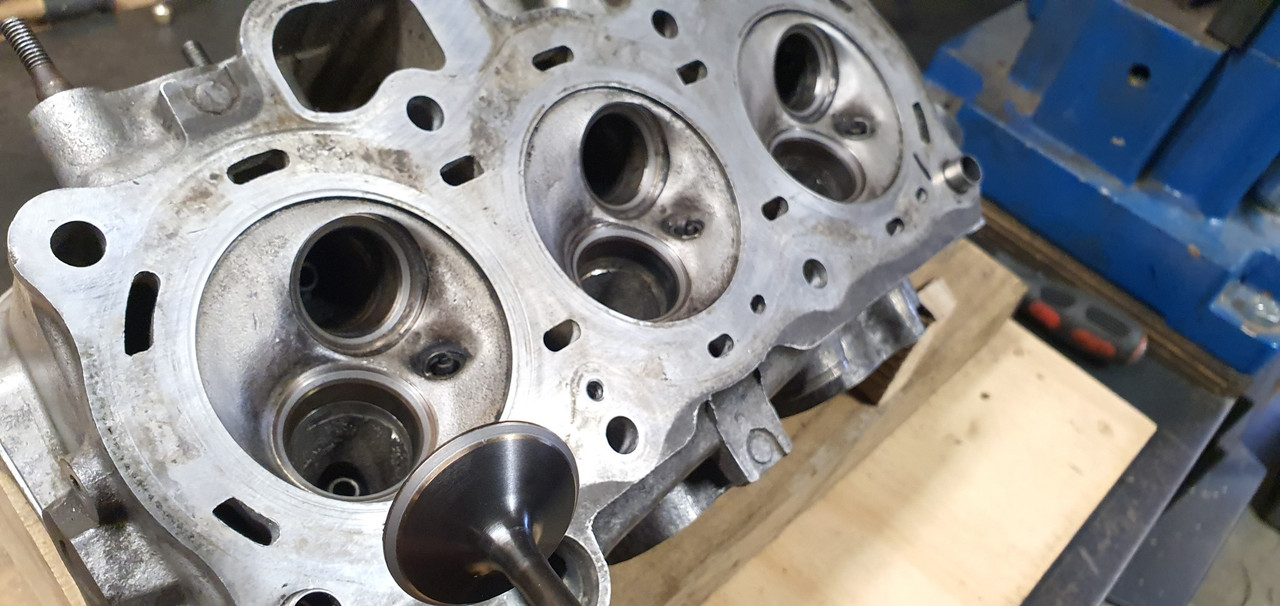
Happy that the valves and seats were good I decided to give the ports a little clean up. Nothing too flash but there's a few casting ridges etc that I could remove...
I was going to use the air grinder but the Dremel seemed a lot more suitable, especially when I remembered I had the flexible extension I've never used before. Wow!! Its perfect for the job.
Just a tickle..
Into the sunshine and swapped over to some tiny sanding drums to smooth things up.
I wanted a nice clean but 'rough' finish on the inlet ports. Certainly not polished. The exhaust ports were smoothed off a lot more but not polished either, a waste of time for very minimal gains on one of these mildly tuned engines I think. If this engine swap works out well, without grenading the transmission etc then another set of heads will be a fun thing to play with. More on this subject later.
Once the port clean up was completed I fastidiously cleaned the heads and blew away any signs of anything that might cause harm if it were to get into a bearing surface. Brake cleaner and the airline was perfect for this.
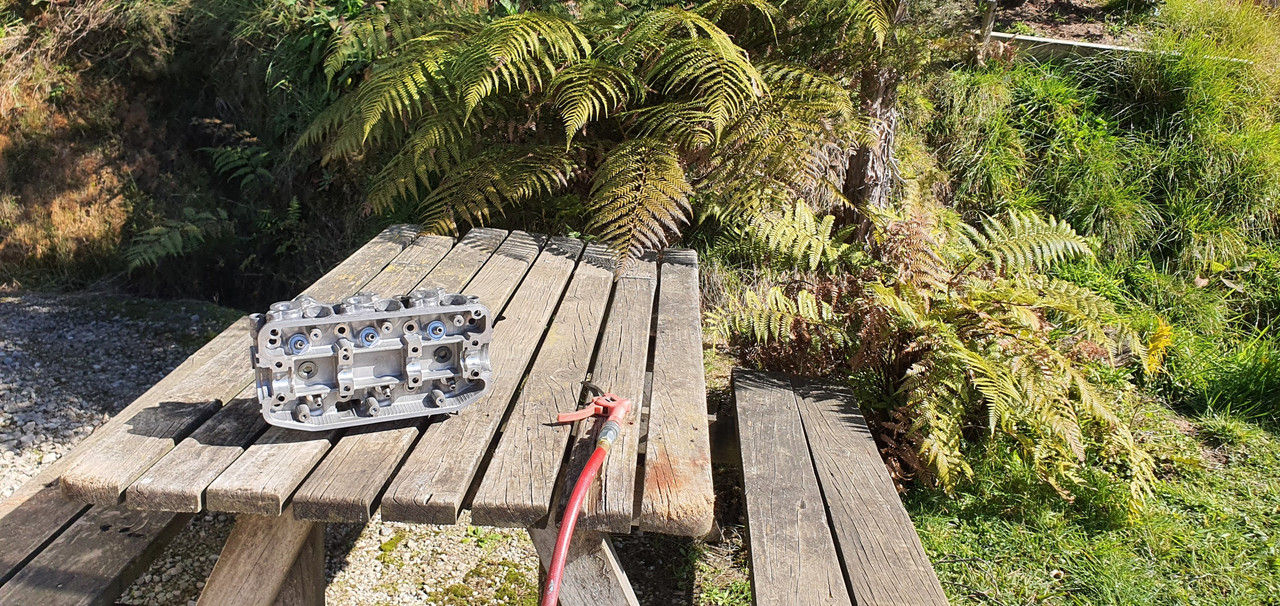
Next I sealed up the ports and fitted the plugs back in place..
Brand new stem seals, the ones I'd ordered from Norway of all places and they had taken bloody ages to get here, but here they are..
Refitted the valves and called it done. Rise and repeat for the other head. Then I had two nice clean heads ready for service..
Next job was the cam follower assemblies. Again, like the heads, not too dirty, no real signs of oil staining etc but certainly in need of a clean anyway.
The underside showing the rockers..
Plastic tray compartments cleaned and shuffled about to suit their new role. One assembly at a time.
The rockers, followers and rocker shafts show next to no wear. The lack of needle roller bearings between the rocker and the eccentric lash adjuster cam thing dates this engine to something around early 90s. If I'm correct I think they added needle bearings around 1993.
Here's a pic to show how the hydraulic lash adjuster moves the cam and so take up the slack in the rocker..
These adjusters are like many you might find in car engines. To make things easier to explain here is an exceptionally accurate, highly detail and finely drawn technical drawing I just did on my phone...
Oil is contained with the the unit and held under pressure by the engines oil system, fed to each adjuster by oil ways within the cam follower cradle. The piston part, uppermost, is a very fine fit into the base and held in place by crimping. In order for them to work properly the air must be removed from the adjusters and that's what the spring loaded steel ball is for. Push that in (red arrow) and air is expelled. If they were to be left on their side or upside down the oil within will eventually drain out and air introduced.
From what I can work out they don't self bled and the oil within is not constantly renewed. So over time the oil will break down and become dirty just from the minute amount of metal on metal wear within.
Mine certainly showed as much as I cleaned them out and they took a good bit of working before they stopped showing any wisps of dirty oil. There is a special Honda tool that is used to push the ball valve in. I machined one up in aluminium with a bit of tig rod set in the middle but in use it wasn't as good as just using a neatly shaped bit of 1.6mm tig rod. Using this I was really able to see what was coming out each time I purged them after draining.
As per the manuals I used kerosene. I had three little vessels filled. Then, after they had been left upside down to drain any residue left over I re-bled them using Penrite fully synthetic full zinc bike oil. I figure that since the oil in these adjusters might never get changed out it makes sense to have some decent oil with good anti wear additives... plus I happened to have a container of it because I use it in our Honda big red quad bike
The adjusters were now all clean, lubed and showing no movement when pressed, which is what is required when bled. I then cleaned the rest of the parts and reassembled. I mounted them on the wall facing up - ready for when I need to fit them to the heads.
Interesting bit of info I found whilst doing some googling on these units I discovered that the Honda Valkyrie 1500, a sort of sportier cruiser version of the touring goldwings, has apparently got slightly hotter cams. I have not found any definitive info on exactly what the difference is. More lift or duration etc. But more interesting is that they also ditch the hydraulic lash adjusters and instead use simple screw and nut type adjusters on the rockers as per many other Honda bikes. See here...
So my future plan if this engine setup works out ok would be to locate a pair of Valkyrie heads/cams/followers and have a play with them. At the same time I could setup these BMW itbs that hannah so kindly brought back from the UK...
They'll need the tabs lengthening so to space them apart a touch further to suit..
Other parts, this time delivered by the postman...
Bosch style (but not price) Idle air control valve, various sensor plugs and some shiny new exhaust gasket rings and nuts.So the heads are ready to go back on but before I do I wanted to sort some other little jobs out while the engine is compact and easy to move on the bench. This morning I made this...
It's designed to stop oil surging back up the filler tube. It really is probably not needed actually bu I see no harm it being there as a belt and braces add on. I'e still yet to decide on the final height and extension of the filler..
Oil height and volume is going to be more than sufficient I think. I'm not sure what the height was in the original configuration and I seem to have foolishly thrown away the original dipstick so I cant check that. Dipstick went in here..
I'd like to have the oil height maybe an inch below the crank throw. I'll have a think about this. Anyway - lots of room for oil. I think about 4 litres at least.
I also need to add a vent to the crankcase. Most likely it will be here, right below where the little owl is sitting...
Because there is a useful casting that would shield the vent hole from oil splash..
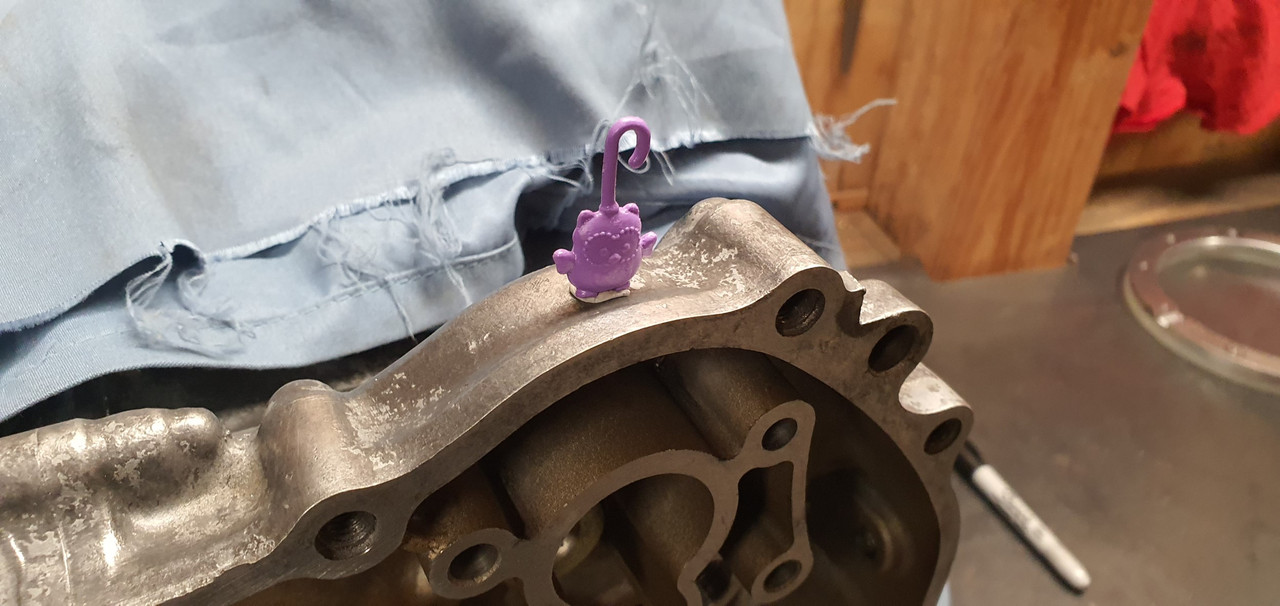