Meet Ralph - 1970 ST project
Moderator: Bootsy
Re: Meet Ralph - 1970 ST project
Lovely work. Re: bending pipe, is filling them with sand then applying heat a valid approach? I ask because I’ve only read about doing that.
John
John
Re: Meet Ralph - 1970 ST project
Thanks,
I think its a valid approach. I did spend some time looking at bending pipe a while ago, I even knew the difference between Tube and pipe at one point.
I seem to remember 'Homebuilt by Jeff' using the sand approach on his 911 roll bar and it giving an improvement but my take away from the video was that he'd been through a lot of pain so that I didn't have to. To be fair he probably didn't have Tubecraft in Woking 15mins away.
I think its a valid approach. I did spend some time looking at bending pipe a while ago, I even knew the difference between Tube and pipe at one point.
I seem to remember 'Homebuilt by Jeff' using the sand approach on his 911 roll bar and it giving an improvement but my take away from the video was that he'd been through a lot of pain so that I didn't have to. To be fair he probably didn't have Tubecraft in Woking 15mins away.
Re: Meet Ralph - 1970 ST project
Bit of a tidying day...
2021-12-08_05-00-16 by richard cannings, on Flickr
and some drilling.
2021-12-08_05-00-04 by richard cannings, on Flickr

and some drilling.

-
- DDK 1st, 2nd and 3rd for me!
- Posts: 2036
- Joined: Thu Jul 08, 2021 8:18 am
- Location: Lichfield
Re: Meet Ralph - 1970 ST project
It's starting to look like a car! It's going to look ace with those wheel arches on but I don't envy you getting them to look flush and tidy... A hairy moment coming up when you make the cut. 

1970 911T, Signal orange (Restoration thread)
1988 3.2 Carrera backdate, Black
2001 996 Turbo, Lapis blue (am I allowed to put that here?)
I'm looking for a pre-impact bumper 911S or other high-revving 911 to restore - please let me know if you see one.
1988 3.2 Carrera backdate, Black
2001 996 Turbo, Lapis blue (am I allowed to put that here?)
I'm looking for a pre-impact bumper 911S or other high-revving 911 to restore - please let me know if you see one.
Re: Meet Ralph - 1970 ST project
I have been using an Rtech DC TIG for about 6 or 7 years - no issues to date. I generally have it set to 9A for really thin or fragile sheet metal or to build up around blown holes prior to filling them, 13A if 9 doesn't work, 17 if 13 doesn't work. Either 17 or 22A to tack very solid 1mm ish sheet metal (new or original), 17A for short seam welds e.g. 1cm long - that's as high as I go. I tried the fancy pulse functions at the beginning, but didn't find them to be useful. The only function that I set is current ramp up, but I dont really know whether it is having any benefit.rich73 wrote:Really happy with the lower power output, I've found that even on 1mm butt welds I'm not going down to the minimum setting using 0.8 wire.
Maximum output is ridiculous(180A), just a shame I wont be using it much.
Rich

I'm a bit surprised that you use the lowest current setting on your MIG - perhaps only for seam welding? I have an old Butters AC transformer-based MIG. I have never had any success seam welding thin circa 1mm sheet using MIG - I almost always burn through at some point. Consequently, I only ever seam weld using individual tacks. I have no idea what the currents are, but I have it set at 2 (out of 5) for building up, 3 for tacking 1mm ish sheet (butt weld), 4 for plug welding with 7mm holes only because the highest setting 5 trips the fuse

It was Barry that suggested that I turn it up as high as possible for plug welding, and make a switch to 0.8mm wire, and I haven't looked back since. My plug welds are now almost entirely and consistently flat and neat, needing next to no grinding, whereas they used to look like irregular splodges

Dean
1973T Targa MFI 334 met blu- under restoration https://www.ddk-online.com/phpBB2/viewt ... 28&t=67060
1980 924 Turbo, blu/grn tartan - restored
1973T Targa MFI 334 met blu- under restoration https://www.ddk-online.com/phpBB2/viewt ... 28&t=67060
1980 924 Turbo, blu/grn tartan - restored
Re: Meet Ralph - 1970 ST project
Feeling more confident about welding the arches, I've been using TIG more and I'm starting to get the hang of using hammer and dolly to remove the distortion. Main thing I need to do now is get the positions correct.
I tend to use 25 to 30A on the TIG for 1mm steel and I've started using 1mm filler rods which work much better than 1.6 for me. I know you can use MIG wire but like the rods.
I now realise now important minimising the gap is.
2021-12-13_05-33-12 by richard cannings, on Flickr
Not so pretty where filling gaps....
2021-12-15_01-53-53 by richard cannings, on Flickr
Replaced lower sections of the rear wings, one looked pretty good but was pitted so replaced both.
2021-12-15_01-52-27 by richard cannings, on Flickr
2021-12-15_01-52-40 by richard cannings, on Flickr
2021-12-15_01-54-08 by richard cannings, on Flickr
On the new MIG I'm using setting 1(of10) and this works well on 1mm steel for but welds, I'll have a try a higher setting for plug welds on a rest piece and let you know how I get on.

I tend to use 25 to 30A on the TIG for 1mm steel and I've started using 1mm filler rods which work much better than 1.6 for me. I know you can use MIG wire but like the rods.
I now realise now important minimising the gap is.
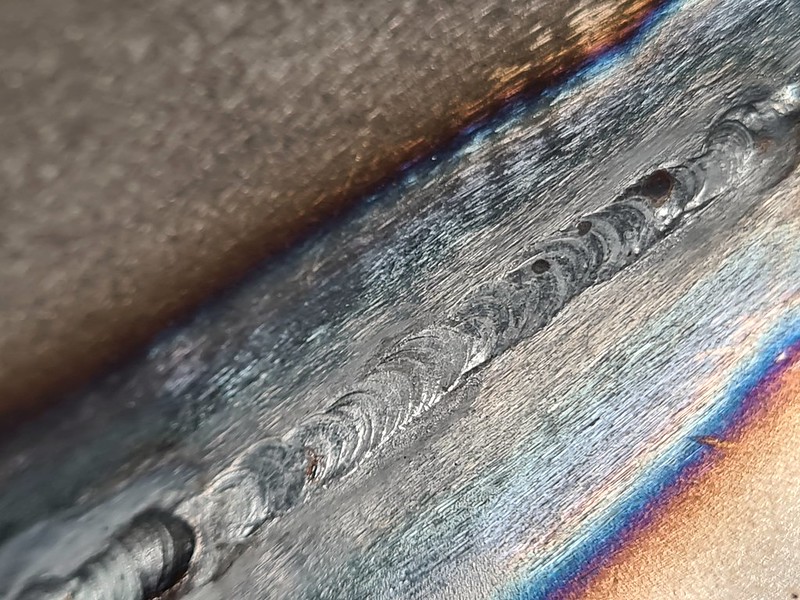
Not so pretty where filling gaps....

Replaced lower sections of the rear wings, one looked pretty good but was pitted so replaced both.



On the new MIG I'm using setting 1(of10) and this works well on 1mm steel for but welds, I'll have a try a higher setting for plug welds on a rest piece and let you know how I get on.
-
- DDK 1st, 2nd and 3rd for me!
- Posts: 2036
- Joined: Thu Jul 08, 2021 8:18 am
- Location: Lichfield
Re: Meet Ralph - 1970 ST project
Where filling gaps - does the bead level off much if you give it a quick blast with the tig after? Might be quicker (and quieter) than grinding.
1970 911T, Signal orange (Restoration thread)
1988 3.2 Carrera backdate, Black
2001 996 Turbo, Lapis blue (am I allowed to put that here?)
I'm looking for a pre-impact bumper 911S or other high-revving 911 to restore - please let me know if you see one.
1988 3.2 Carrera backdate, Black
2001 996 Turbo, Lapis blue (am I allowed to put that here?)
I'm looking for a pre-impact bumper 911S or other high-revving 911 to restore - please let me know if you see one.
Re: Meet Ralph - 1970 ST project
I Think it does but I've become a little obsessed with getting as little heat as possible into the panel. I'll give that a go tomorrow and see how I get on.
TIG weld really is soft though, 80 grit sanding disk will flatten quite quickly.
Rich
TIG weld really is soft though, 80 grit sanding disk will flatten quite quickly.
Rich
Re: Meet Ralph - 1970 ST project
Ooo, those TIG welds are looking good
I think that it is possible to flatten the larger beads for sure, but I think it will be at the expense of more distortion because you need more current or heating time to melt them. I find it better just to take them off with the grinder (power file or flap disc).
I use 1mm Tungstens and 1mm rod when the gap is zero to around 0.5mm or for pin holes, or 1.6mm rod if the gap is wider or for filling holes up to maybe 3 or 4mm dia. I was taught to TIG on aluminium, without filler rod, by Contour Autocraft, but I have since found that when I try this on steel, the join tends to be thin and sink a little bit. It also takes a while to eliminate the gap on steel, whereas a quick brush with a file gets you there quickly an Al. MIG wire tends to take the curved shape of the reel, which isn't very good for feeding accurately when visibility is already limited by the helmet, or working at a difficult angle. By the way, I dont use my helmet for MIG tacking any more - it is much quicker and easier, I find, just to close my eyes
Loving all this welding chat!


I think that it is possible to flatten the larger beads for sure, but I think it will be at the expense of more distortion because you need more current or heating time to melt them. I find it better just to take them off with the grinder (power file or flap disc).
I use 1mm Tungstens and 1mm rod when the gap is zero to around 0.5mm or for pin holes, or 1.6mm rod if the gap is wider or for filling holes up to maybe 3 or 4mm dia. I was taught to TIG on aluminium, without filler rod, by Contour Autocraft, but I have since found that when I try this on steel, the join tends to be thin and sink a little bit. It also takes a while to eliminate the gap on steel, whereas a quick brush with a file gets you there quickly an Al. MIG wire tends to take the curved shape of the reel, which isn't very good for feeding accurately when visibility is already limited by the helmet, or working at a difficult angle. By the way, I dont use my helmet for MIG tacking any more - it is much quicker and easier, I find, just to close my eyes

Loving all this welding chat!


Dean
1973T Targa MFI 334 met blu- under restoration https://www.ddk-online.com/phpBB2/viewt ... 28&t=67060
1980 924 Turbo, blu/grn tartan - restored
1973T Targa MFI 334 met blu- under restoration https://www.ddk-online.com/phpBB2/viewt ... 28&t=67060
1980 924 Turbo, blu/grn tartan - restored
-
- Nurse, I think I need some assistance
- Posts: 18926
- Joined: Mon Mar 10, 2008 6:26 pm
- Location: West Midlands
Re: Meet Ralph - 1970 ST project
Interesting part of this project!
I'm old enough to have done a fair bit of panel welding using gas welding. Hard to control and limit distortion, but the welds flatten and dress very readily.
I've done long butt joins (about 700mm long) and needed very little lead to finish.
I presume the TIG gives the same but less heat?
Although more convenient MIG is a pig to grind off well and quietly.
If you can, why not TIG such panels?
I have never TIG welded.
I'm old enough to have done a fair bit of panel welding using gas welding. Hard to control and limit distortion, but the welds flatten and dress very readily.
I've done long butt joins (about 700mm long) and needed very little lead to finish.
I presume the TIG gives the same but less heat?
Although more convenient MIG is a pig to grind off well and quietly.
If you can, why not TIG such panels?
I have never TIG welded.
73T 911 Coupe, road/hillclimber 3.2L
Lola t 492 / 3.2 hillclimb racer
Boxster 987 Gen II 2.9
Lola t 492 / 3.2 hillclimb racer
Boxster 987 Gen II 2.9
-
- DDK 1st, 2nd and 3rd for me!
- Posts: 2036
- Joined: Thu Jul 08, 2021 8:18 am
- Location: Lichfield
Re: Meet Ralph - 1970 ST project
After only ever gas welding when I was younger, MIG welding feels like doing neurosurgery with a baseball bat.911hillclimber wrote:Interesting part of this project!
I'm old enough to have done a fair bit of panel welding using gas welding. Hard to control and limit distortion, but the welds flatten and dress very readily.
I've done long butt joins (about 700mm long) and needed very little lead to finish.
I presume the TIG gives the same but less heat?
Although more convenient MIG is a pig to grind off well and quietly.
If you can, why not TIG such panels?
I have never TIG welded.
1970 911T, Signal orange (Restoration thread)
1988 3.2 Carrera backdate, Black
2001 996 Turbo, Lapis blue (am I allowed to put that here?)
I'm looking for a pre-impact bumper 911S or other high-revving 911 to restore - please let me know if you see one.
1988 3.2 Carrera backdate, Black
2001 996 Turbo, Lapis blue (am I allowed to put that here?)
I'm looking for a pre-impact bumper 911S or other high-revving 911 to restore - please let me know if you see one.
-
- Nurse, I think I need some assistance
- Posts: 18926
- Joined: Mon Mar 10, 2008 6:26 pm
- Location: West Midlands
Re: Meet Ralph - 1970 ST project
Once the shock of my screamer 3.2 engine has left the house, I'll ask for a TIG welder.
Seems to be a system in line with gas welding.
MIG is a bit blunt but very convenient to use, eyes closed or masked!
Seems to be a system in line with gas welding.
MIG is a bit blunt but very convenient to use, eyes closed or masked!
73T 911 Coupe, road/hillclimber 3.2L
Lola t 492 / 3.2 hillclimb racer
Boxster 987 Gen II 2.9
Lola t 492 / 3.2 hillclimb racer
Boxster 987 Gen II 2.9
Re: Meet Ralph - 1970 ST project
I learnt to weld with oxy acetylene and TIG is quite a similar process. I've found less heat distortion and a much cleaner weld with TIG than oxy, quite a bit of faff involved though. Things need to really clean, grinding Tungsten's is a pain and Argon is expensive.....
I'd defiantly recommend it though.
Torsion hole alignment tool in operation today, arrived on Saturday as part of the packing for Spin bike but fits perfectly.
2021-12-16_05-35-29 by richard cannings, on Flickr
2021-12-16_05-35-44 by richard cannings, on Flickr
Definitely going with TIG to weld them on as I'm getting more confident with sorting distortion.
Plan is to weld the fronts first but its nice to get the rears out of the way. Don't have the wheels yet put was planning to put a 7 inch fuch(16") on tomorrow to get an idea of clearance. Haven't checked offsets yet but I'm assuming 9" wide will have an extra inch at the front and the back , therefore only stick out an extra inch?
I'd defiantly recommend it though.
Torsion hole alignment tool in operation today, arrived on Saturday as part of the packing for Spin bike but fits perfectly.


Definitely going with TIG to weld them on as I'm getting more confident with sorting distortion.
Plan is to weld the fronts first but its nice to get the rears out of the way. Don't have the wheels yet put was planning to put a 7 inch fuch(16") on tomorrow to get an idea of clearance. Haven't checked offsets yet but I'm assuming 9" wide will have an extra inch at the front and the back , therefore only stick out an extra inch?
-
- Me and DDK sitting in a tree! KISSING
- Posts: 2685
- Joined: Thu May 21, 2009 2:54 pm
- Location: Kent
Re: Meet Ralph - 1970 ST project
Perfect part for the torsion bar hole. Enjoying this thread ... 

70T barn find...... to ST.
1998 C2 996 Kettle
1998 C2 996 Kettle
Re: Meet Ralph - 1970 ST project
Thanks for the torsion bar alignment pointers Dave.
Think I've found my favourite ST image so far tonight.
toad hall daytona-1973 beat up (1) by richard cannings, on Flickr
Hadn't planned to base my car on any specific one but keeping this in the bag just in case panel gaps don't quite work out.
Think I've found my favourite ST image so far tonight.

Hadn't planned to base my car on any specific one but keeping this in the bag just in case panel gaps don't quite work out.