Driveshafts. Connecting the scooby shafts to the imp axles.
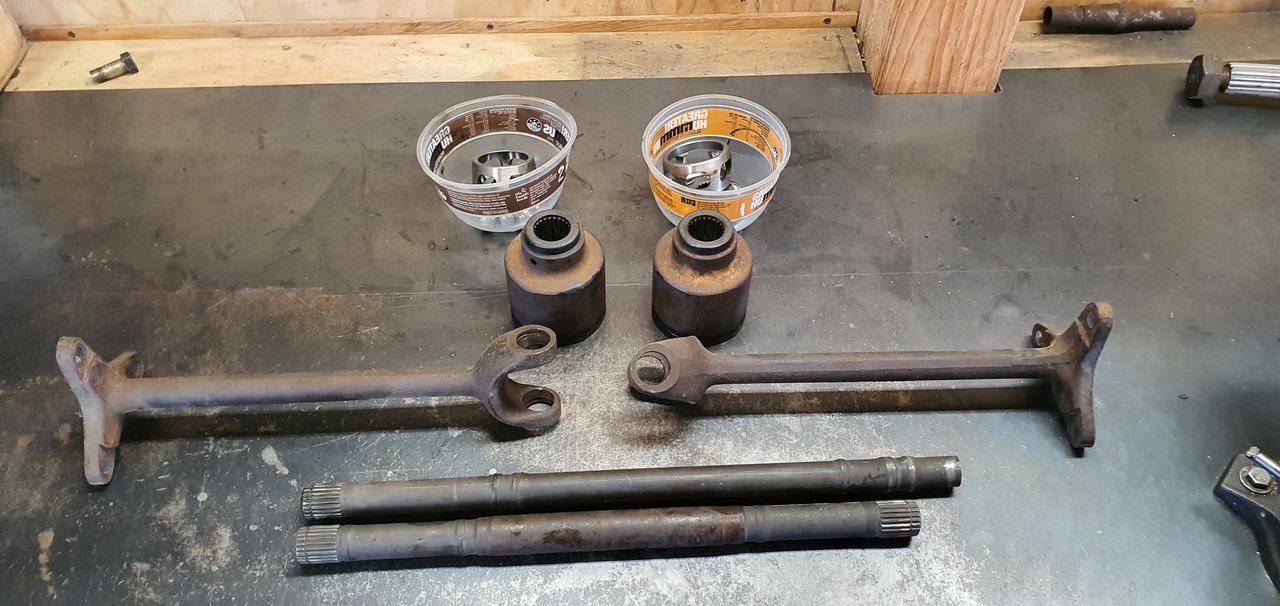
A job I wasn't sure which direction I'd take as there's so many different ideas out there on the nerdnet showing 'the best' way to join shafts.
First thing I did was to double check the suspension travel allowed by the stock shock absorbers and then use those datum points to work out if there was any growth in the length of shaft required as the wheel moves through it path up and down. There was minimal amount, like maybe 5mm at the very most. I guessed as much because the stock Imp driveshaft doughnuts don't allow for much sideways travel.
I then cut one of my 22mm scooby shafts down in length so I could work out the lengths required with the CV joint in place. This move I soon regretted.
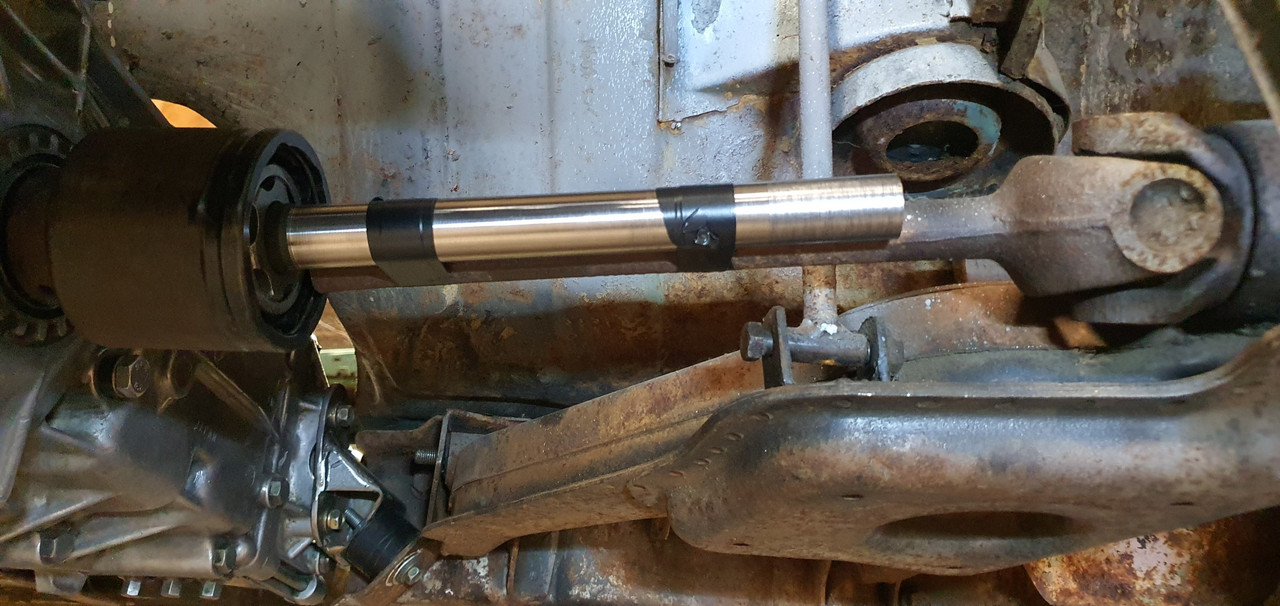
I was allowing for plenty of plunge into the CV joints to make sure the whole joint could be removed from the box stub axle with the box pushed sideways when removing the transmission. I was happy with the length and then decided to go visit a local hotrod builder friend for some advise. He's well known about for his many many full scratch builds and has done heaps of driveshafts in his time (a fellow machinist by trade too)
I showed him the two ways I was considering doing the join. He showed me a better way.
Shrink some bored out yokes cut off from some spare axles. Plenty of meat, will never let go and even if they somehow did loosen and spin they cant come out because there's not enough travel in the CV joint to allow them to. No welding needed. He's run axles done in the same way with some serious big block power and they never let go. Just has to be accurate and luckily its the sort of machining/fitting job I like.
But i needed to start with almost full length scooby shafts to do it, of which I was now down on.. Roll eyes and back to the wreckers to see this beauty get pulled from the hedge...
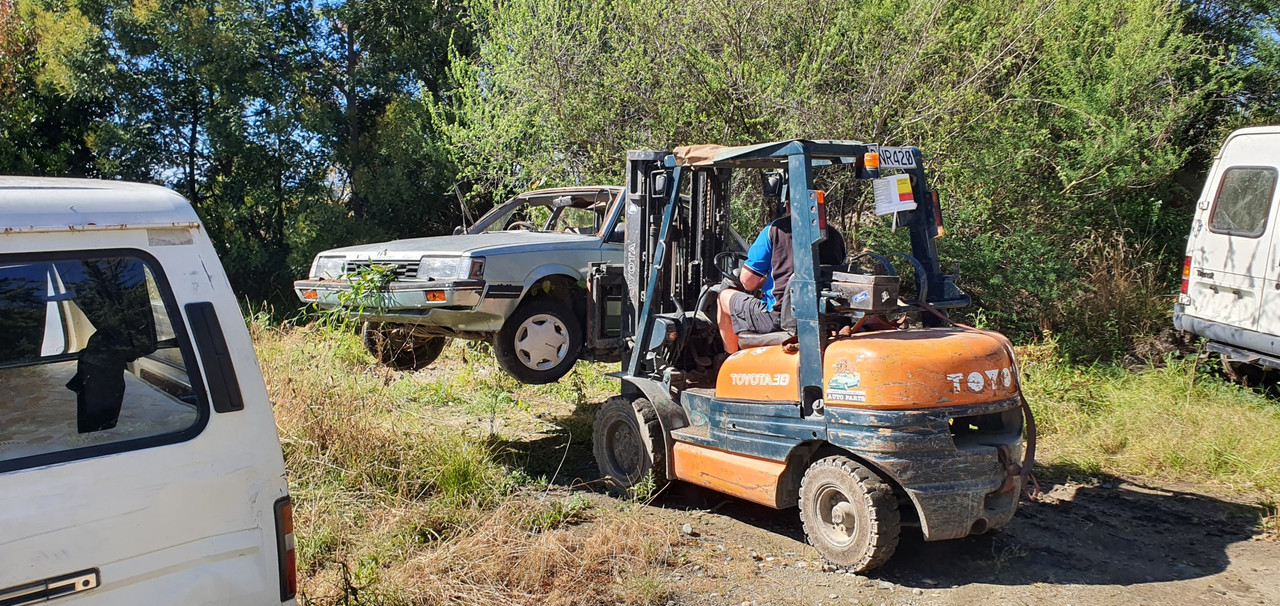
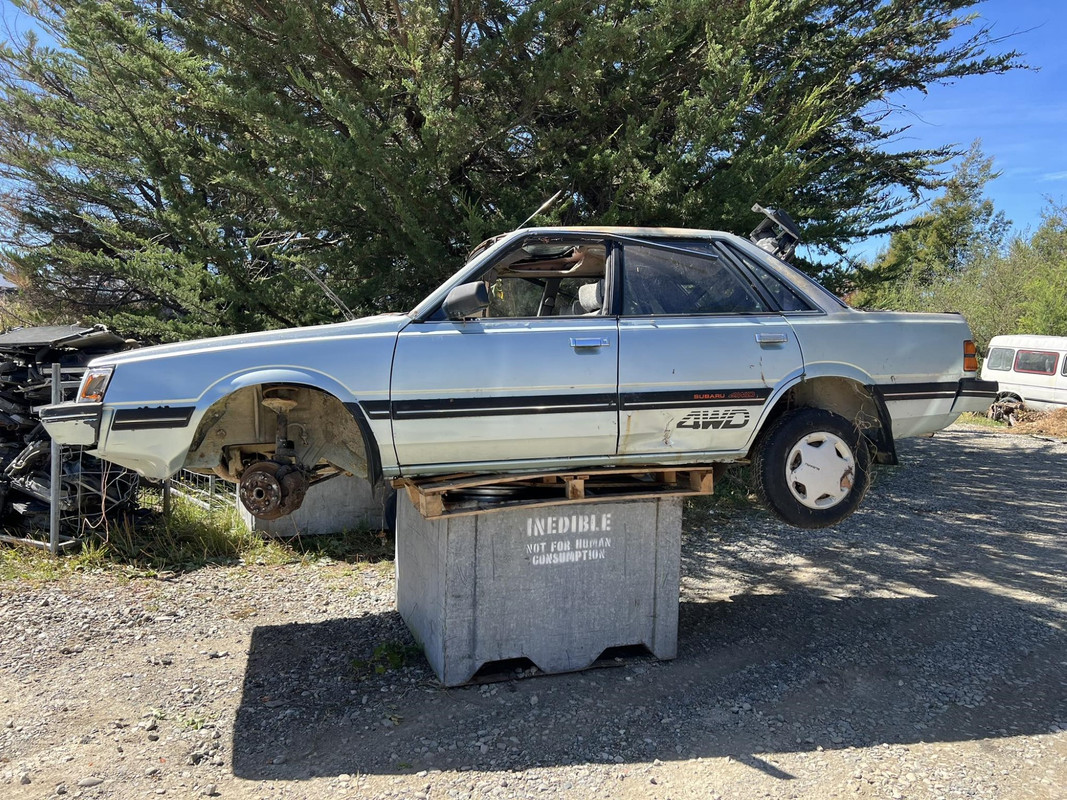
Hannah helped me remove the shafts. It was her birthday too so wow, what a treat. She got visit the wreckers and get oily.
Got home and the shafts didn't fit my CVs. Bigger diameter end. Really weird because I checked online... ha. It lies. Turns out some late 4wd Leones had even bigger axle ends than the Imprezzas. Also odd is that one shaft is 22mm and the other side 24mm, although both the same length.
Back to the wreckers.
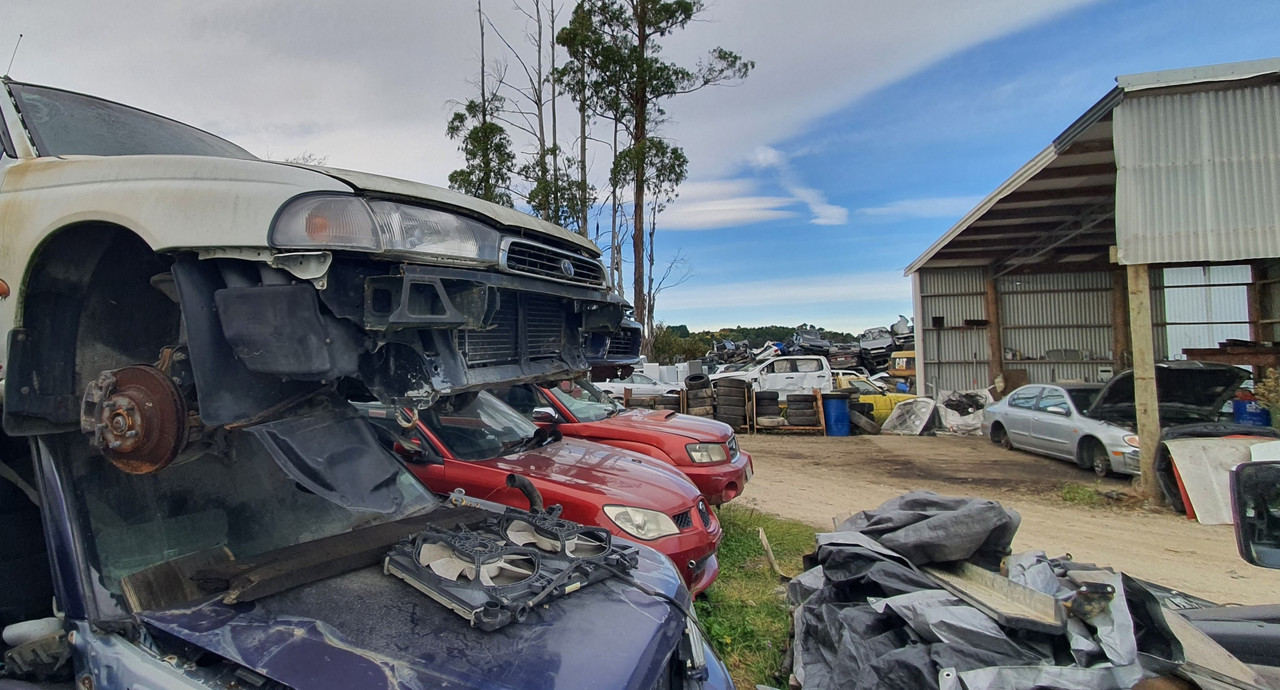
This time I got larger 25mm shafts with the smaller ends from front wheel drive Imprezzas. I grabbed two pairs. Same again, 22mm on one side and 25 on the other. Now I had two of each. Got home and spent some time cleaning them up, outside because petrol fumes.
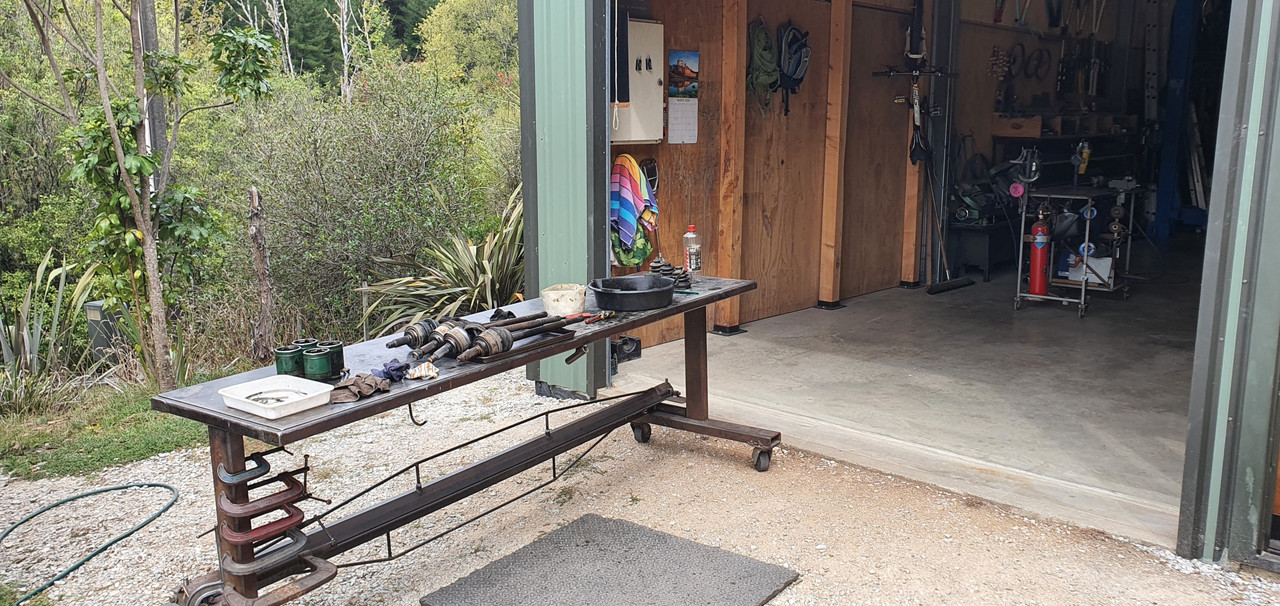
Cleaned up the spare pair of axles in the lathe to make sure I had an accurate clamping spot for the later boring.
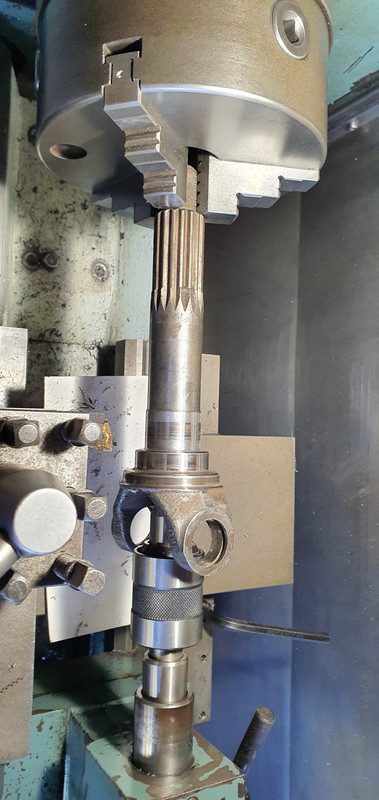
Good quality steel! I turned them down to less than the 23mm bore size and chopped the yokes off.
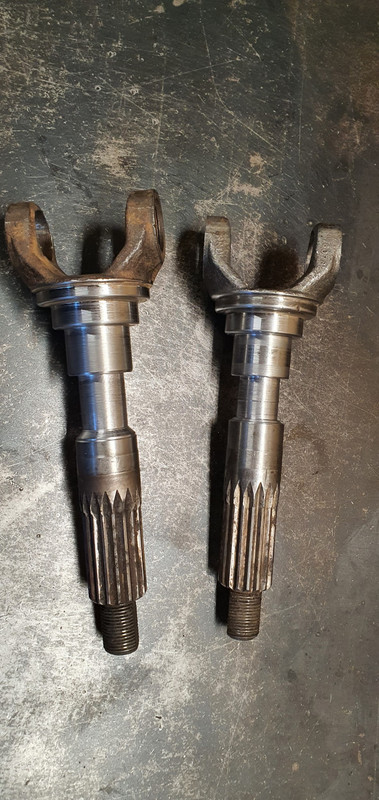
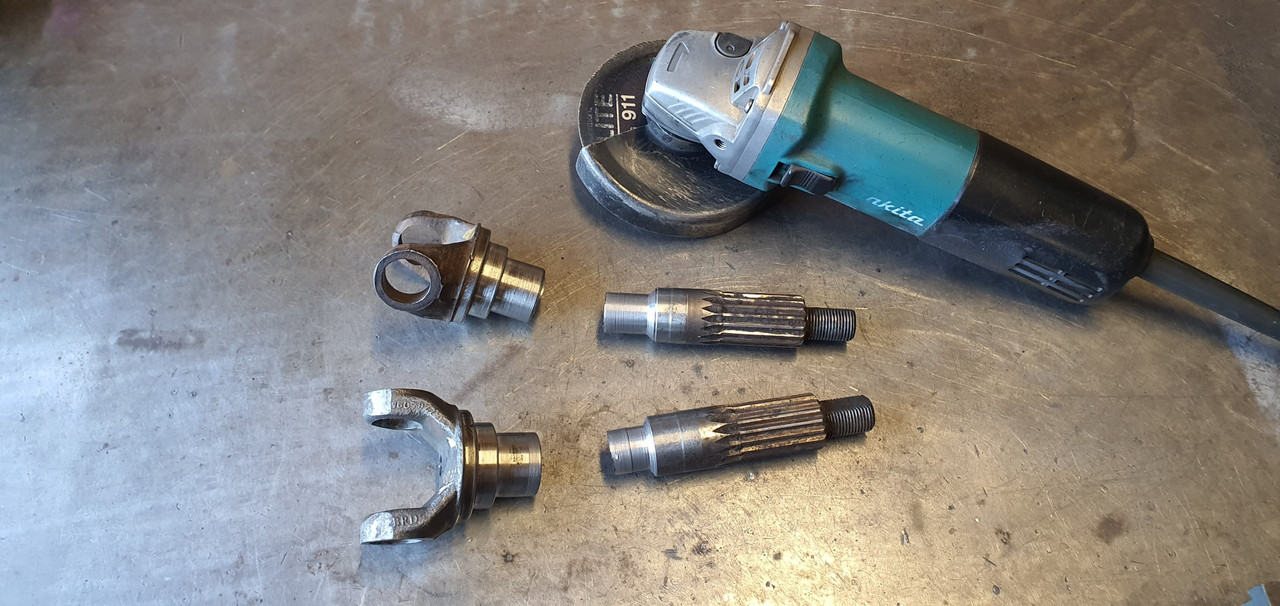
Made lots of swarf
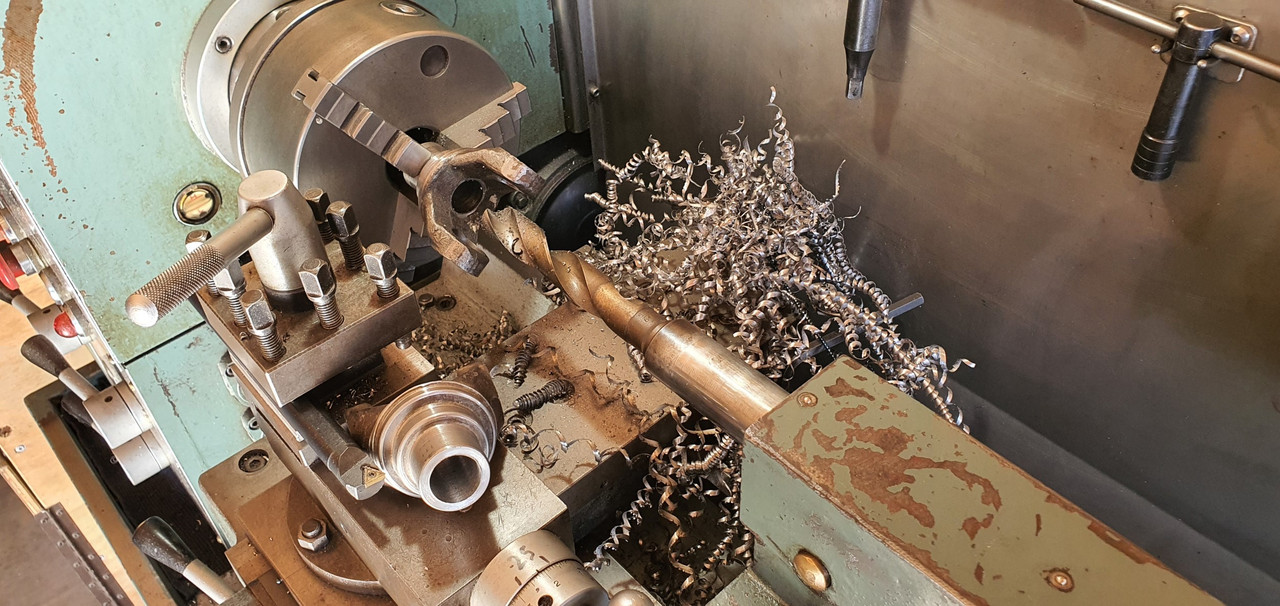
Bored out to bang on 23mm with nice radius.
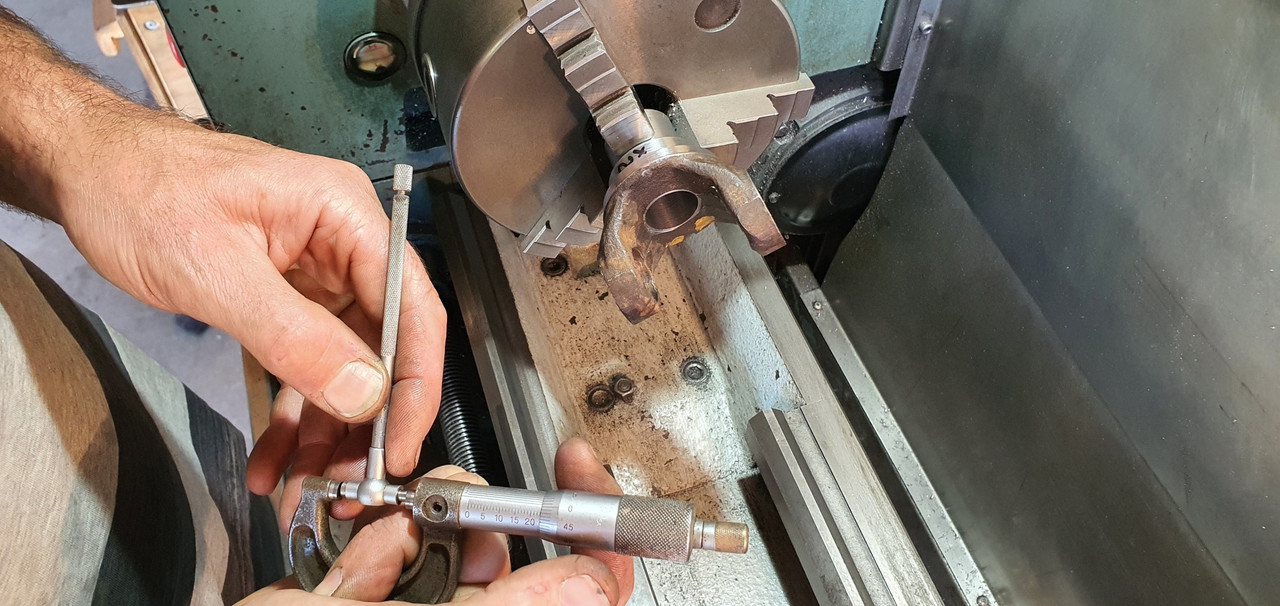
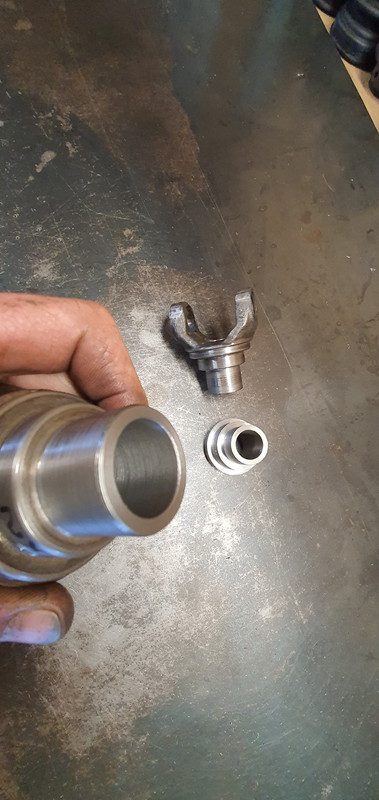
Double checked and triple checked I had my lengths required correct. Chopped the two 25mm scooby shafts down to length and turned a step down on one end of each, a radiused step to stop any stress risers.
I went for .0015"~.002" interference. Go online and see the debates between all the barries about what a good shrink fit should be
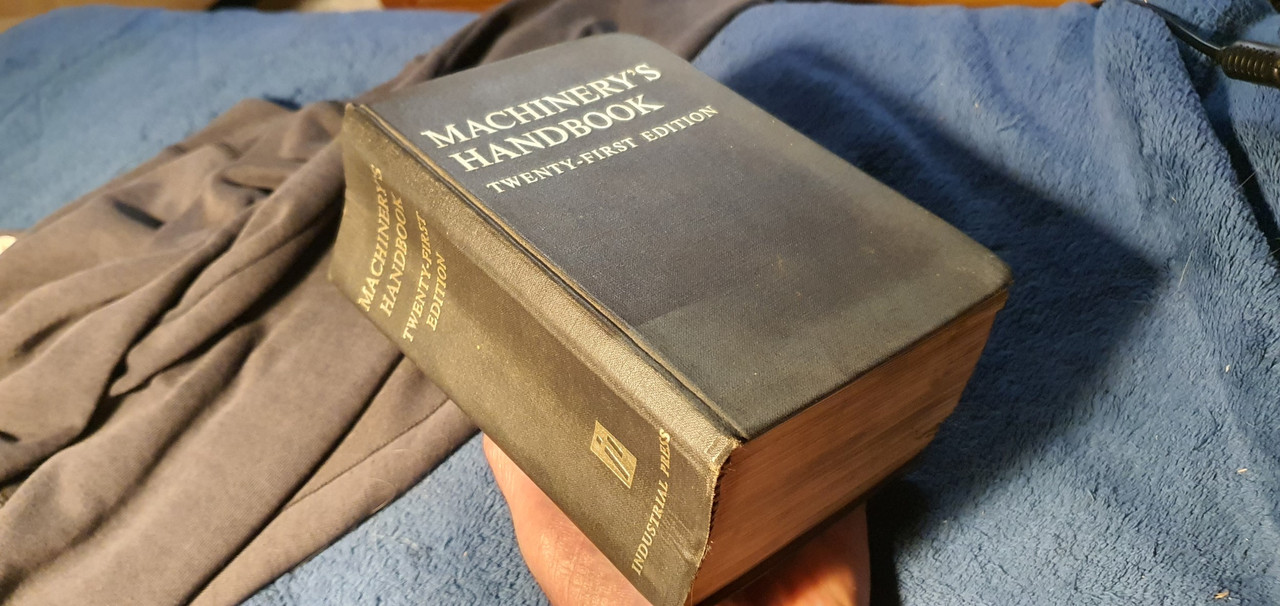
I wanted it tight, but not stressed. Luckily the axle is of good steel.
I also made a sample first, using one of the cut off bits of scooby shaft and some 4340 I machined to the same outer dimensions as the yoke.
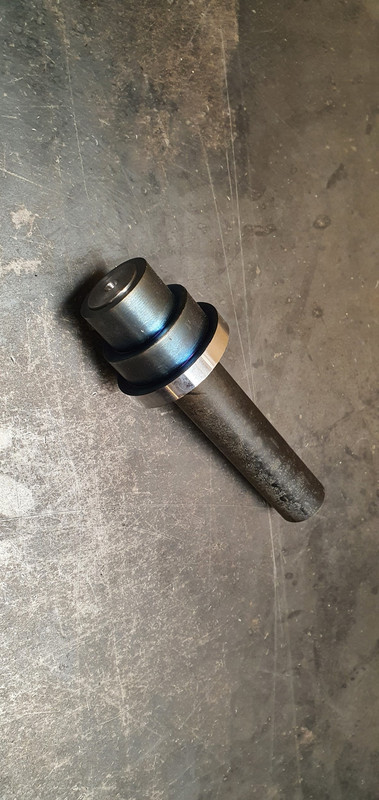
This way I was able to test how hot I needed to get it to expand enough to drop in place. I'll take this to a local engineers who have a press with a pressure gauge and see how much force it takes to wreck this thing

Here's about a one hundredth of a millimetre (iirc) getting removed..
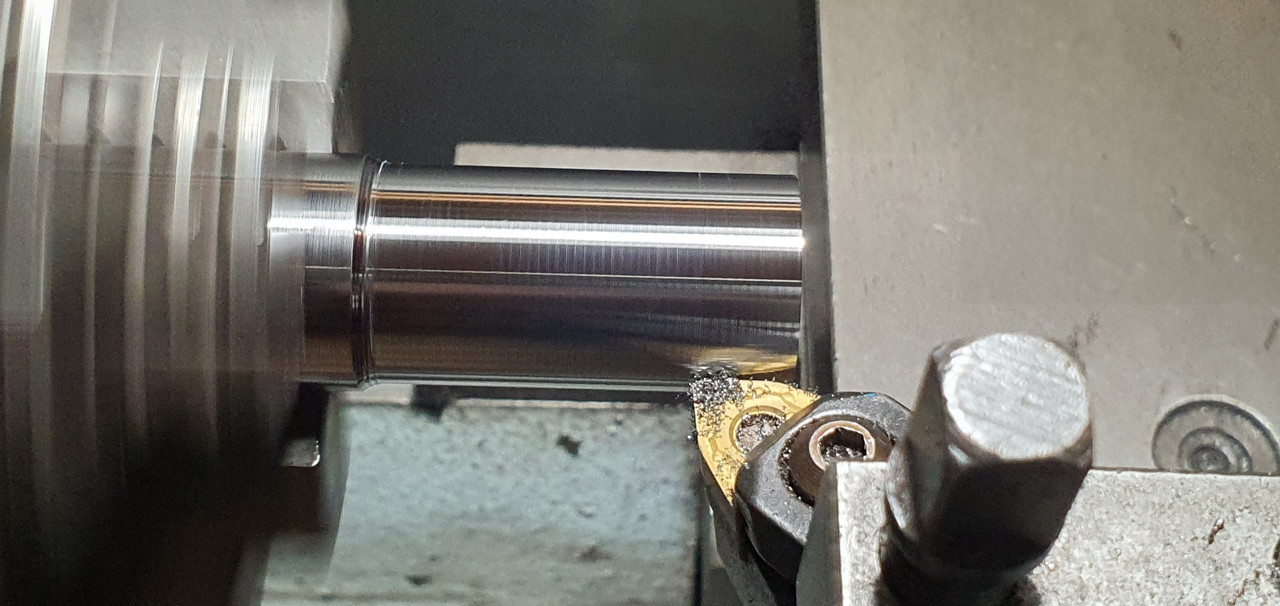
Then things got hot.. photos taken after it was done because I had to move bloody quick! Hannah would grab the torch off me and I would drop the yokes in place. It was a tense bit of time. If the yokes teetered and grab they'd pull the heat so quick and shrink in place before getting to the shoulder. No removing them without damage and I only had the one pair of spare axles.
It went well. I was happy and relieved.
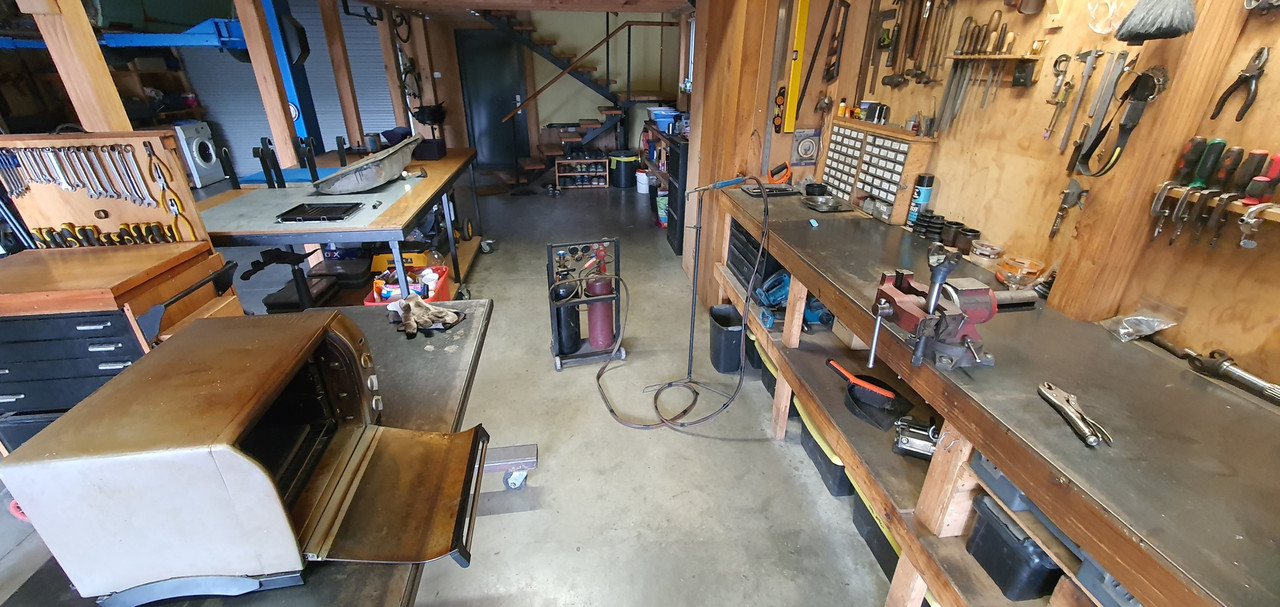
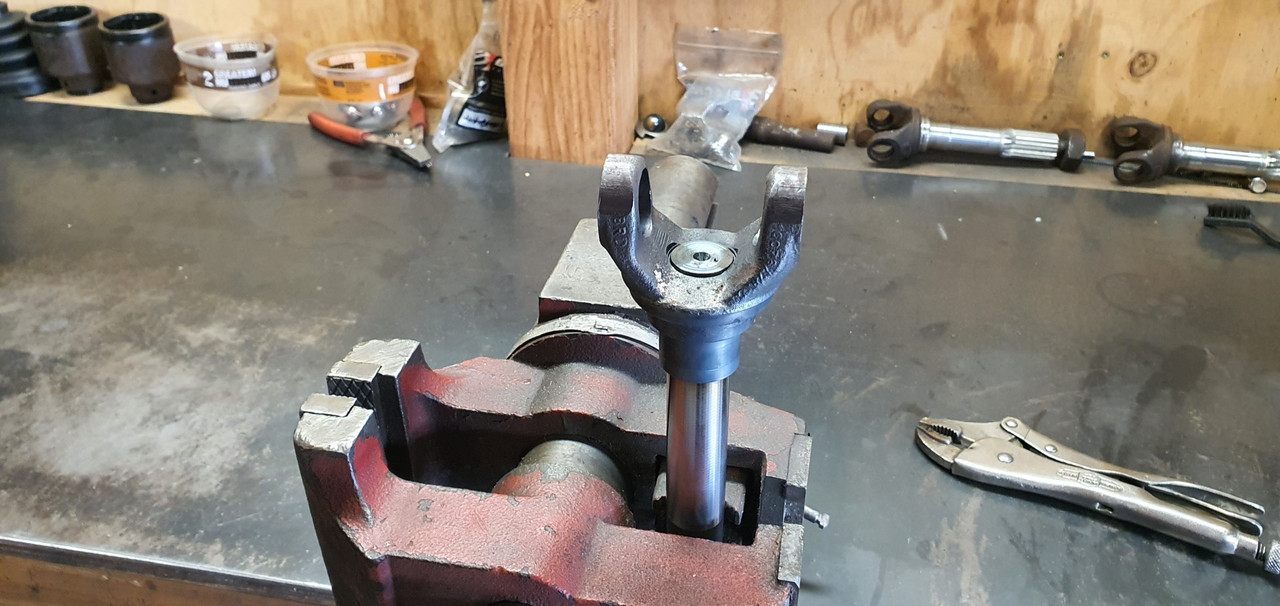
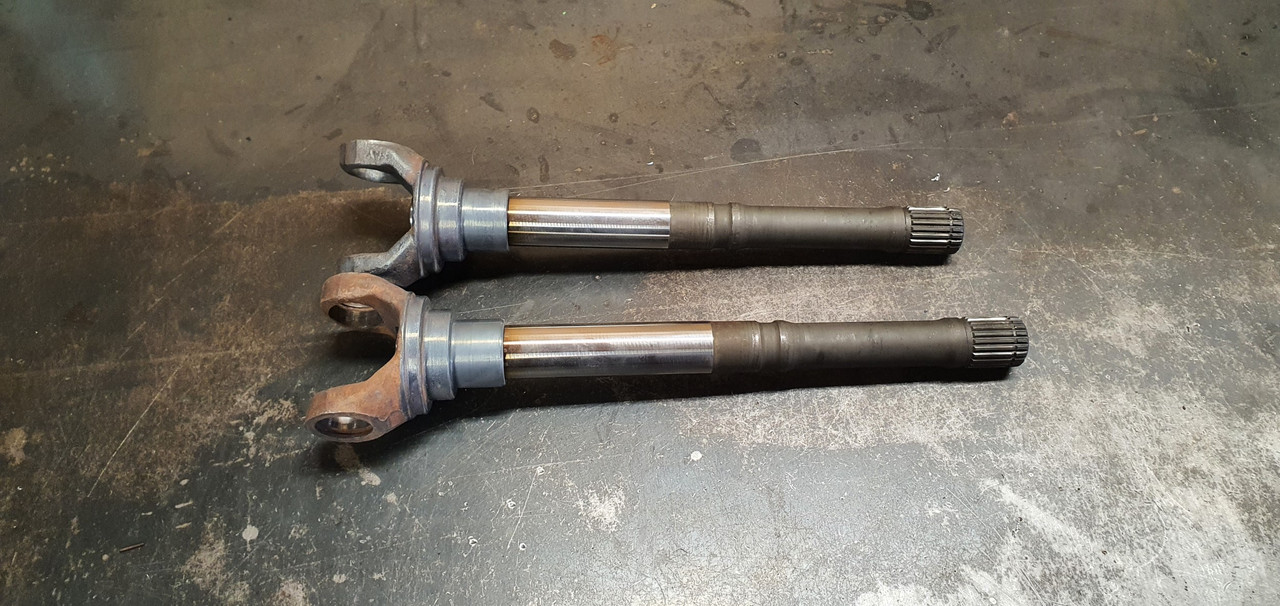
The light rust flashing off on one is simply due to that one having been left nearer the front of the workshop to cool down and it was a chilly damp start to the morning. They wired brushed up neat as, got painted with black epoxy and when that was set they had new universal joints fitted. I cant try them on the car until I remove the existing axles from the hubs but it should be fine.
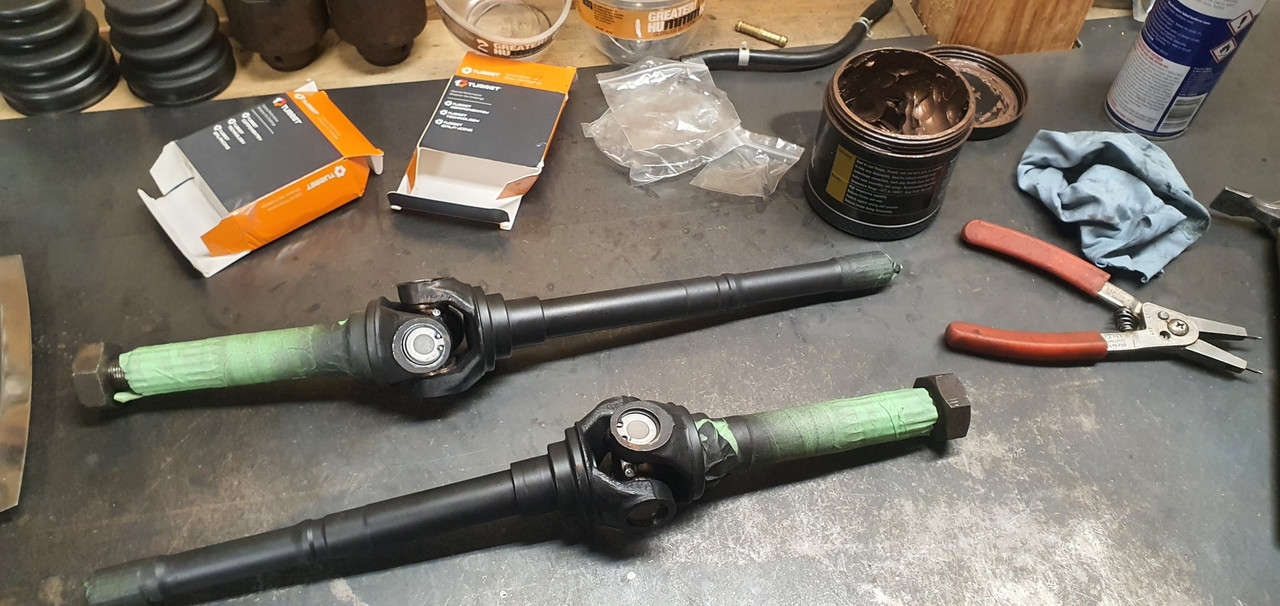
Next up was to sort the fuel tank out to suit fuel injection. I brought the blue imp in and checked a few ideas out on what I could do.
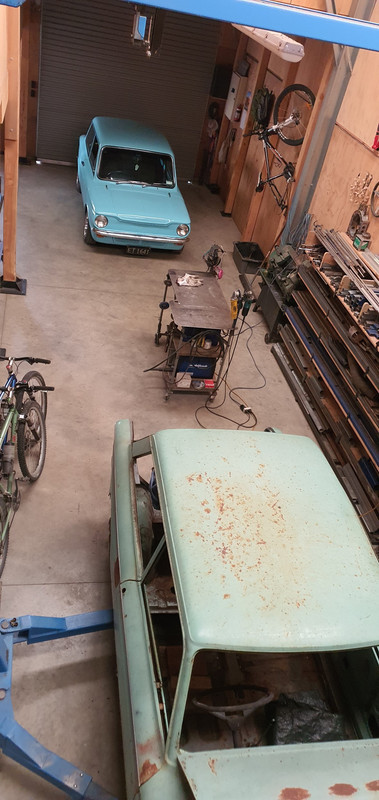
I don't really have room for a surge tank and I never liked the noise on my Viva from the external fuel pump anyway. Nor did I like the way the fuel in the surge tank heats up.
Enter the humble Nissan Micra k11 intank fuel pump and surge container...
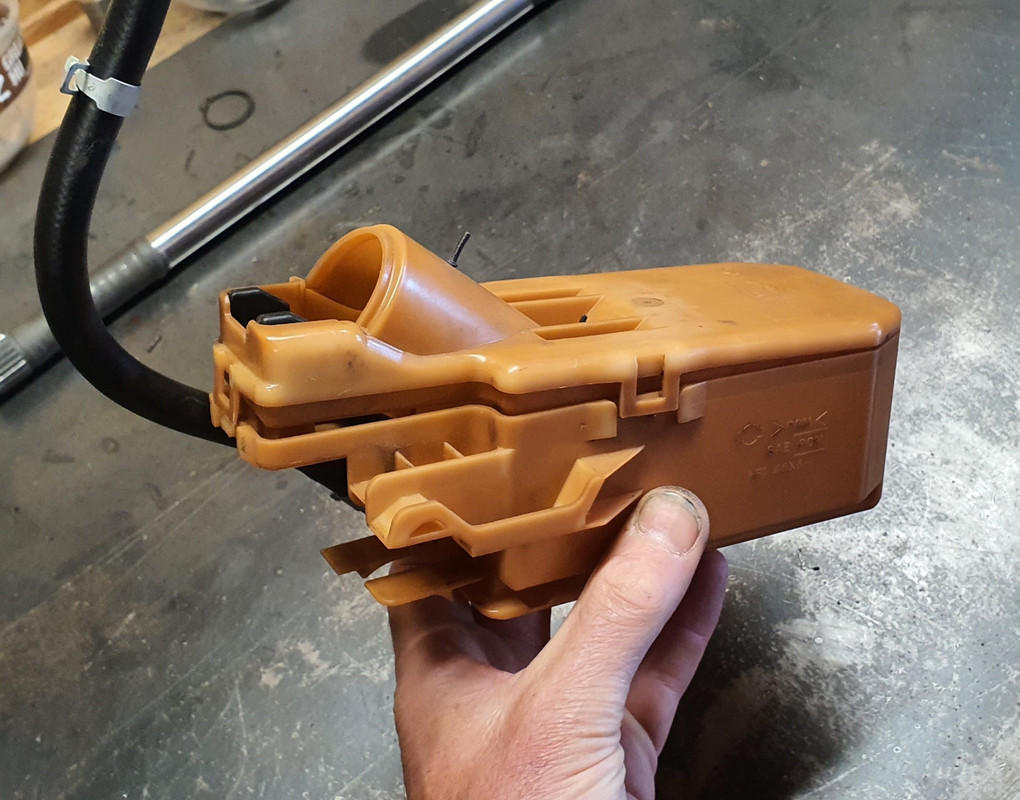
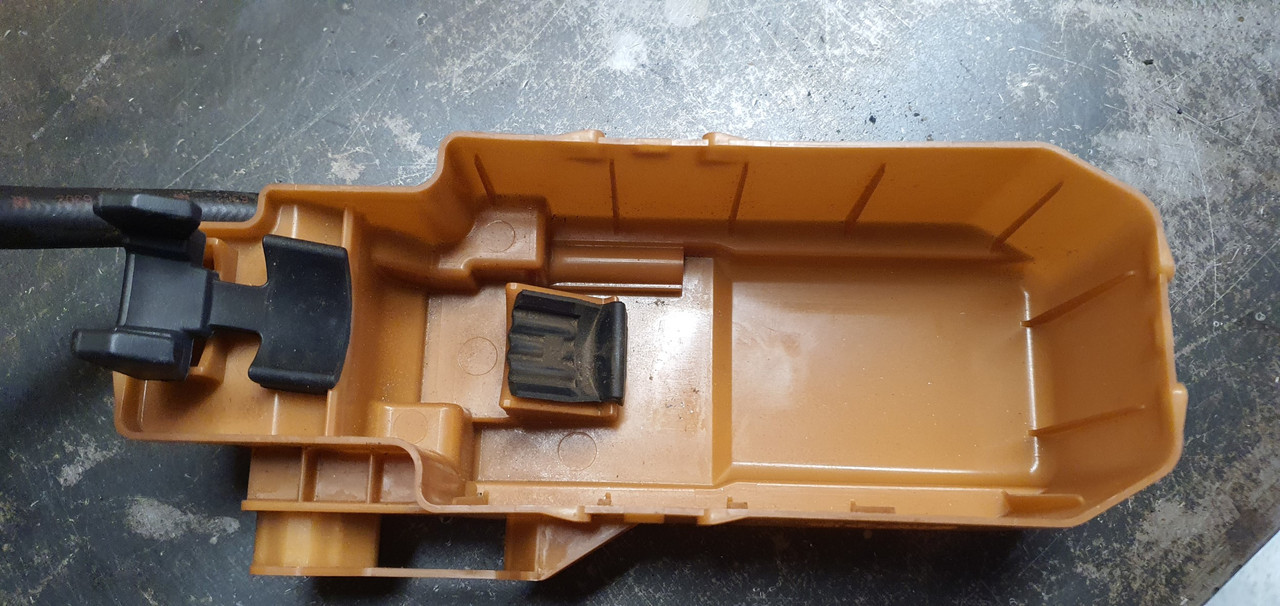
It actually looked like it was just going to fit into the pressed depression at the bottom of the imp fuel tank..
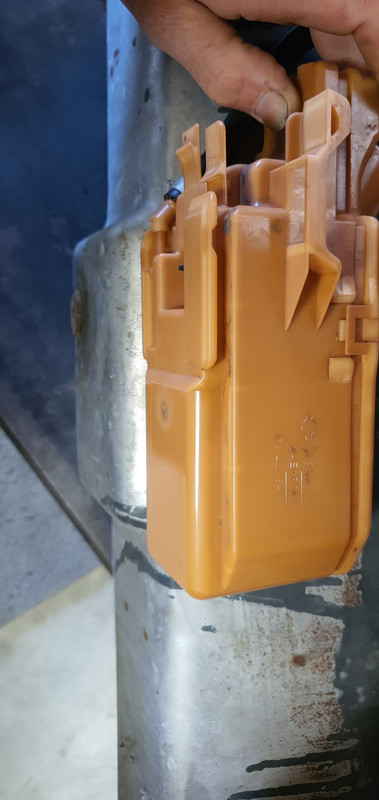
With enough room to run the imp fuel float sender next to it.
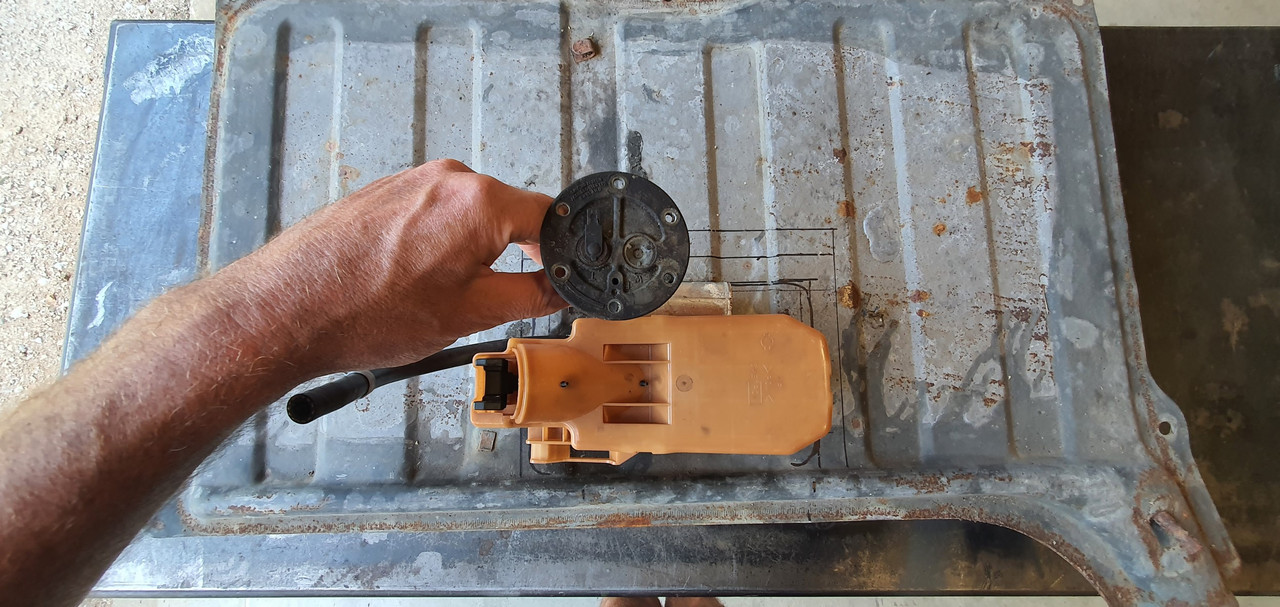
Cut a hole..
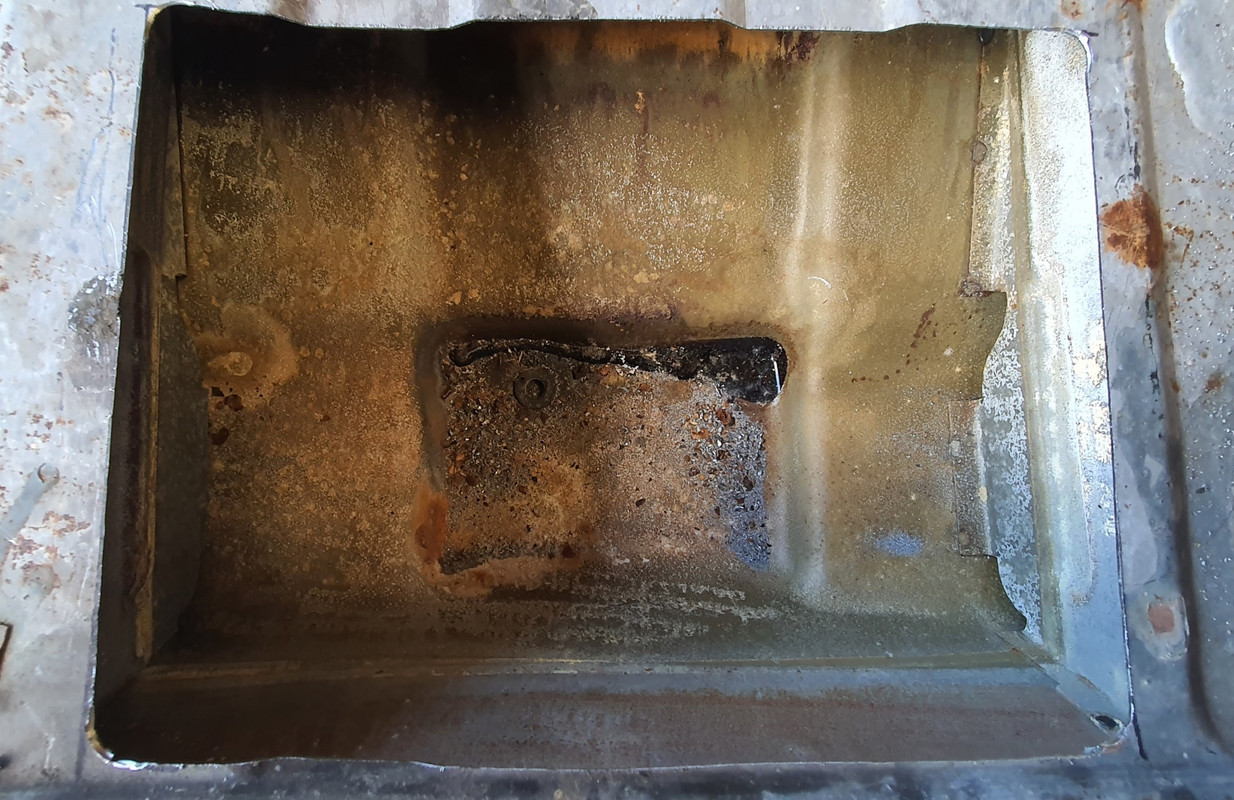
It fits. I'll cut the bracket off the side at bottom of pic and it'll move sideways a bit more..
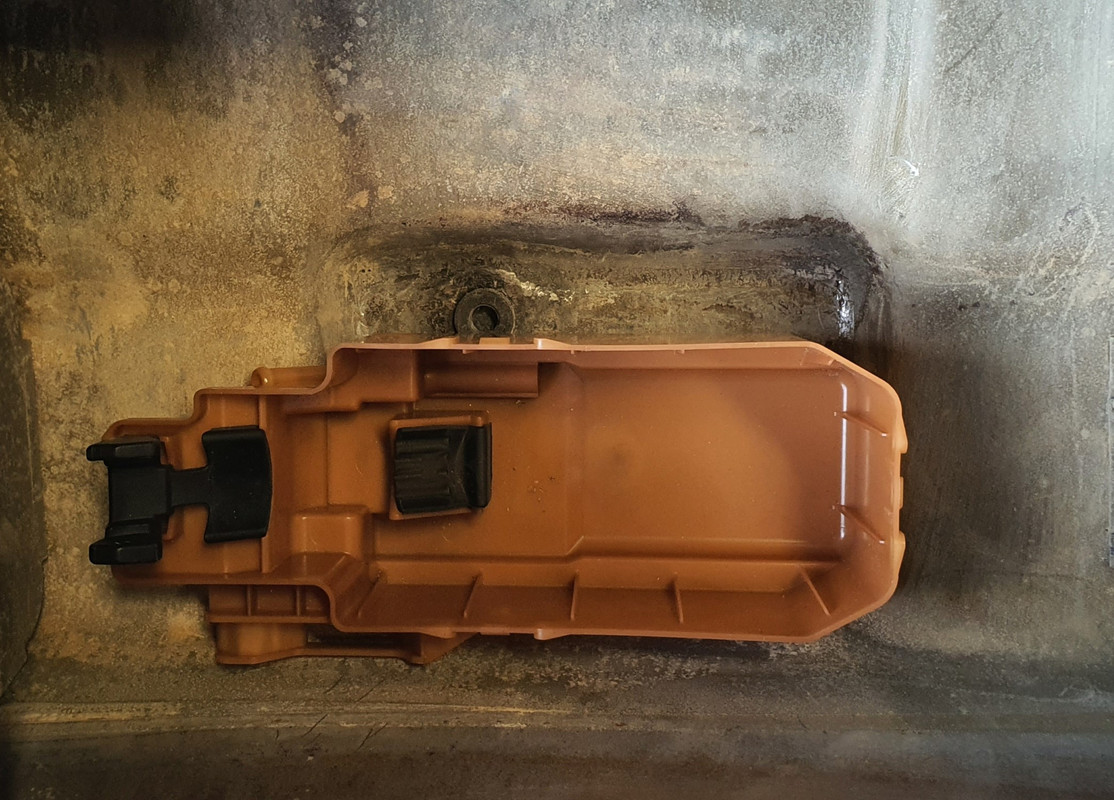
Made some metal brackets
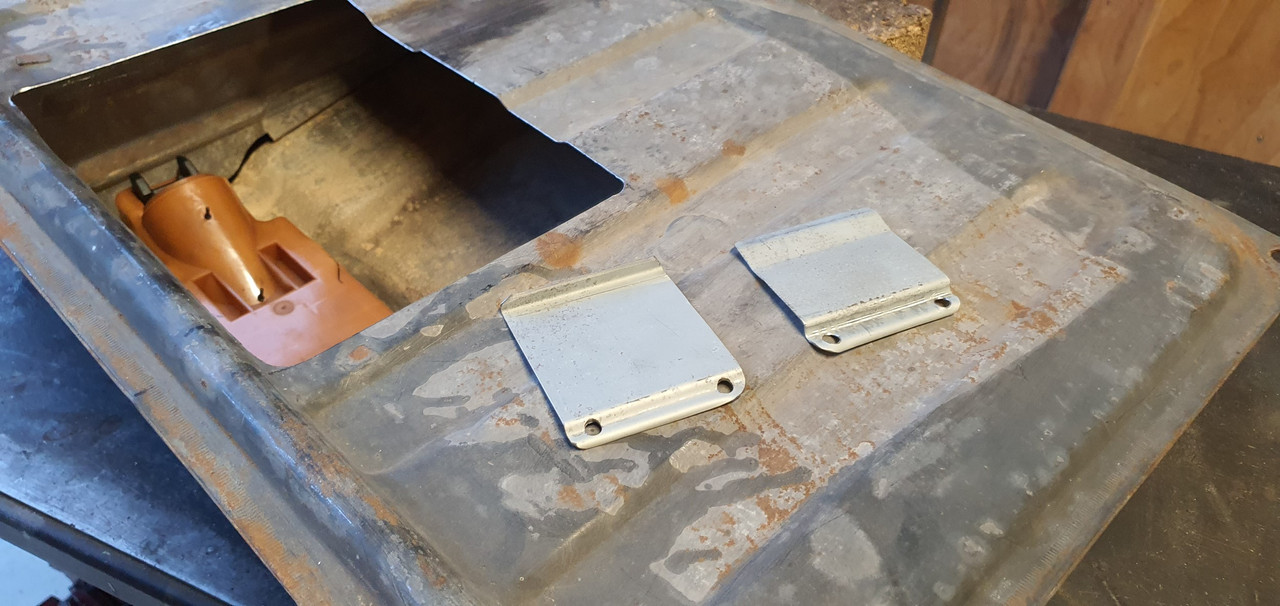
Welded them in and now I have a cradle that takes two cable ties across the top to secure.
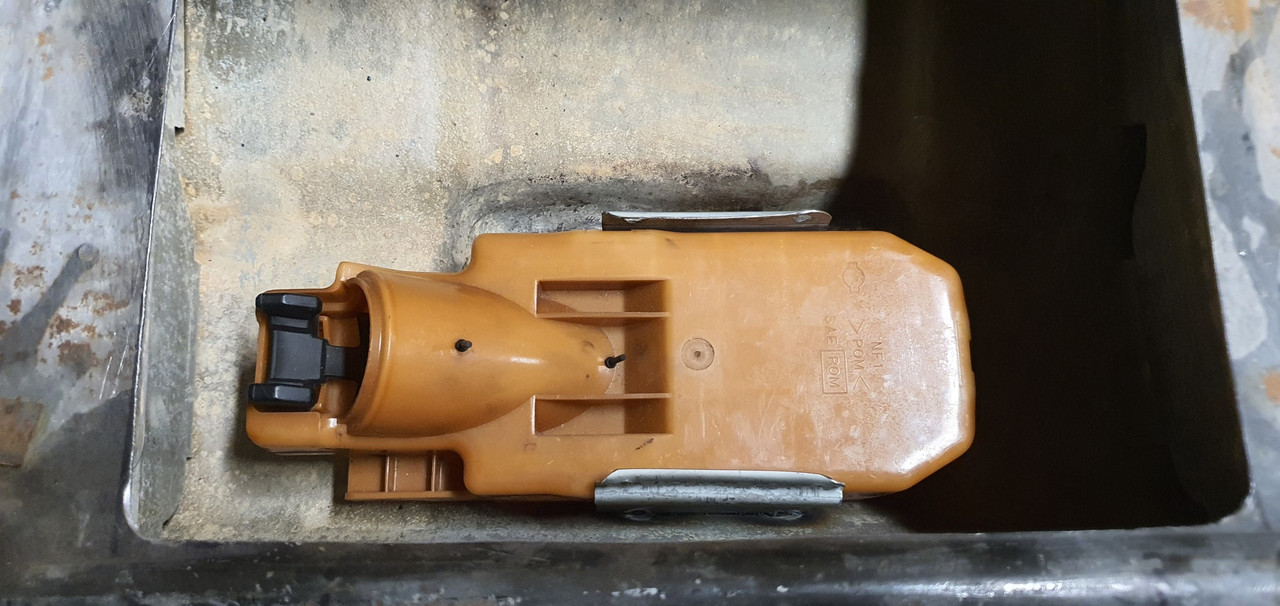
I needed a flange....
Made this. Its designed to recess the lid about 10mm below the tank top. I want to keep the tank top as flat as possible. It'll have the usual layer of foam over top but I don't want things sticking up proud when the 'frunk' is being used (cant be tearing those bags of concrete now eh....)
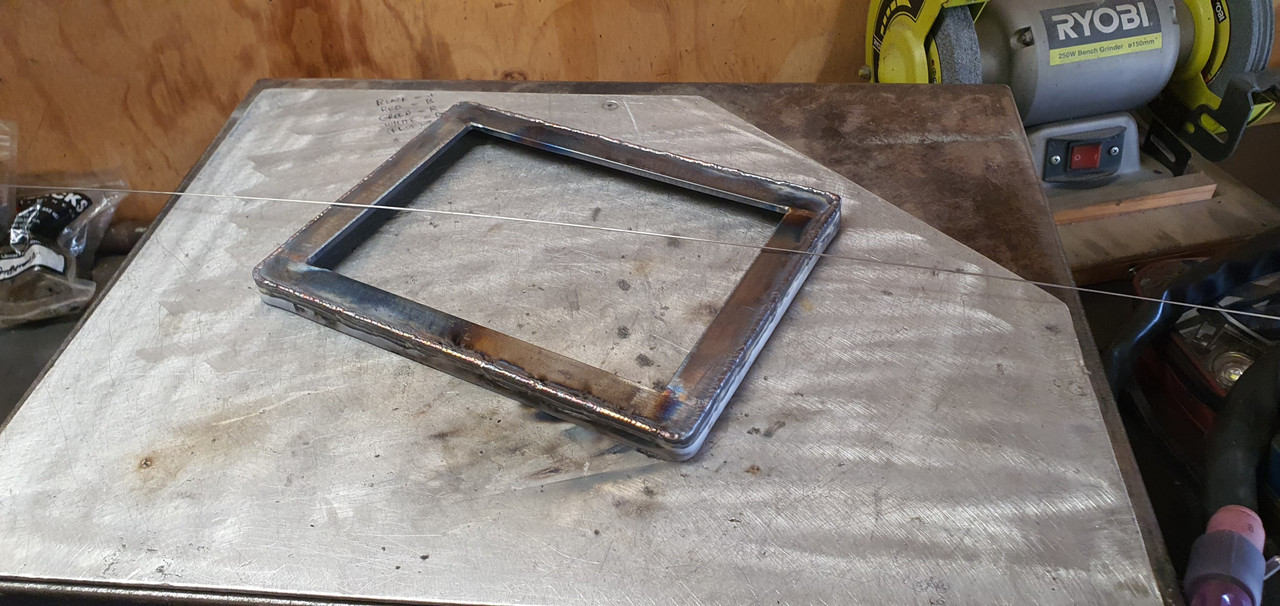
Many holes drilled and tapped..
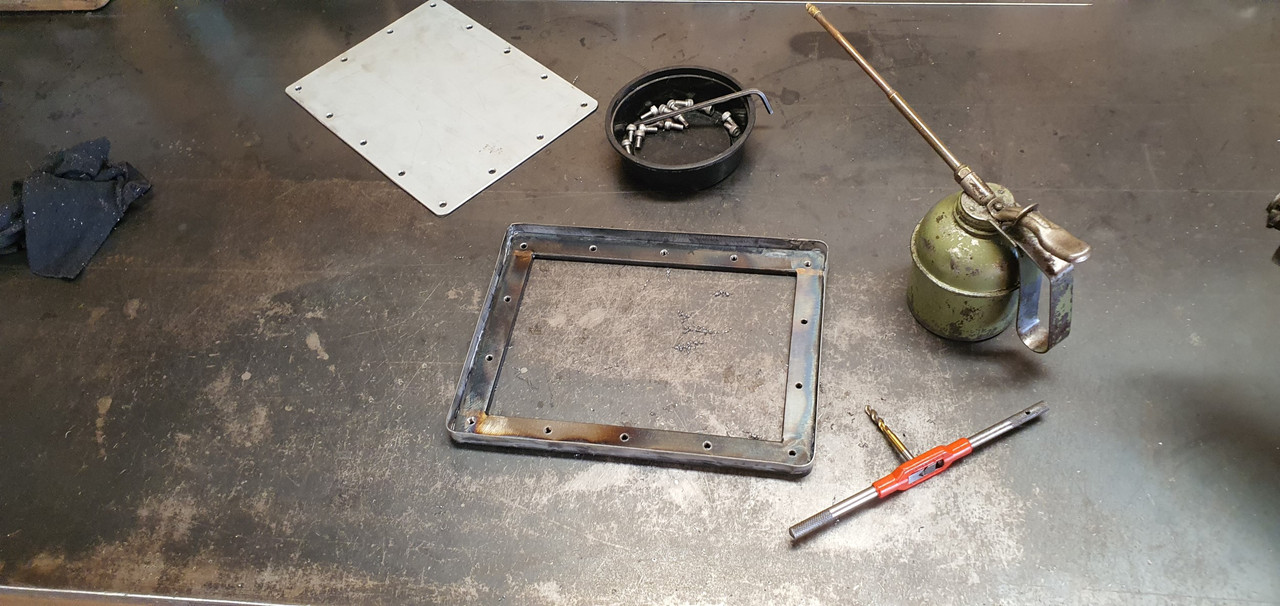
Carefully welded in place. Was a tricky job. Thin steel on the tank that had some sort of (probably poisonous) coating. But happy with result.
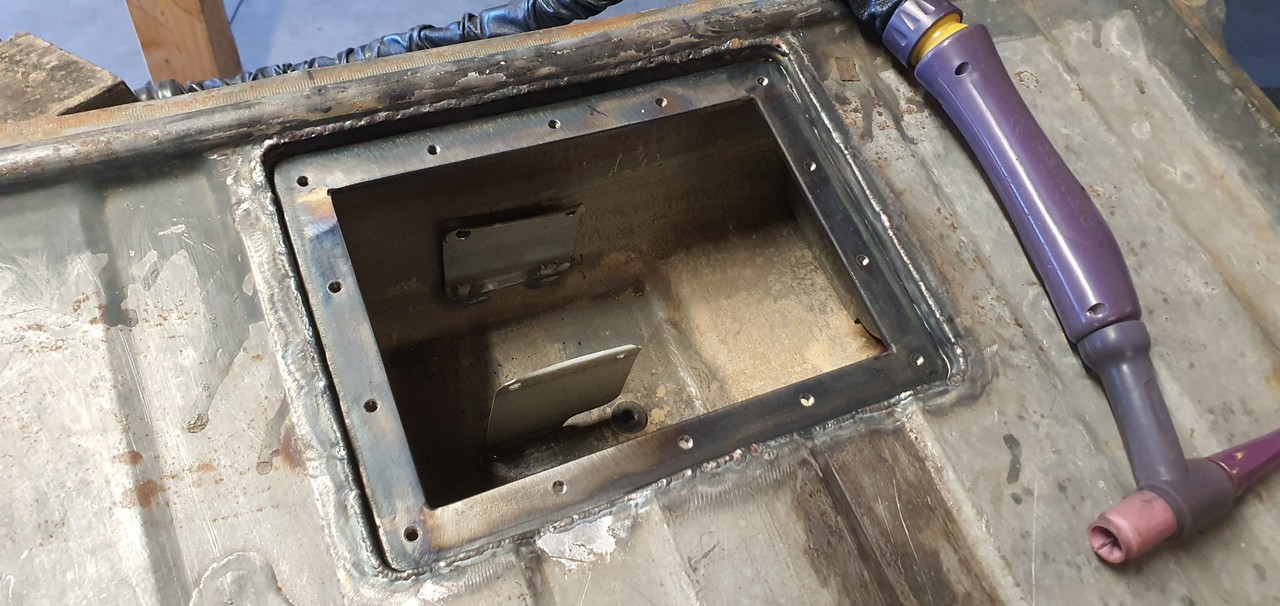
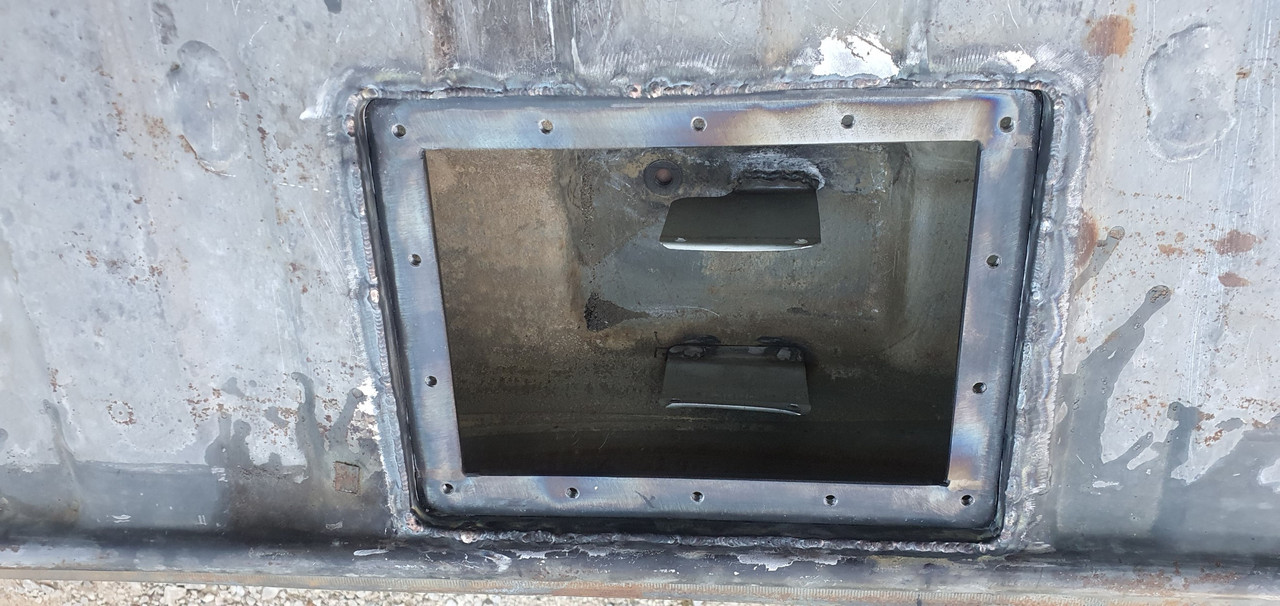
I made another hole...
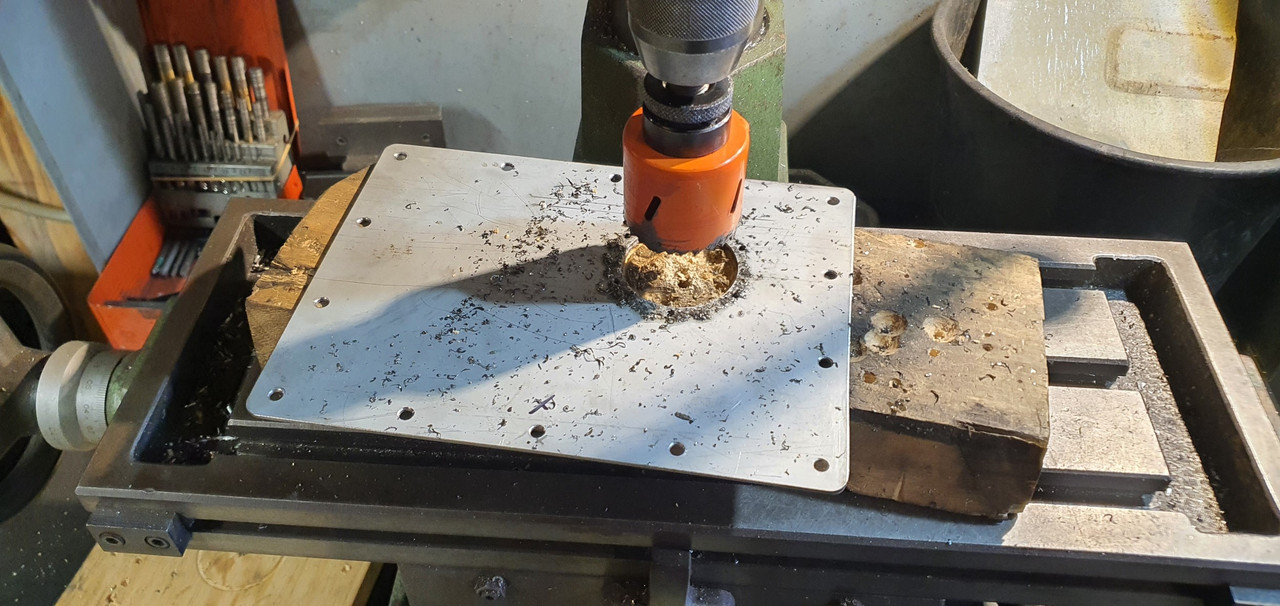
That takes the sender. Drilled and tapped more holes to suit. Now I needed to get fuel from the outside in and from the inside out. I machined up these in stainless..
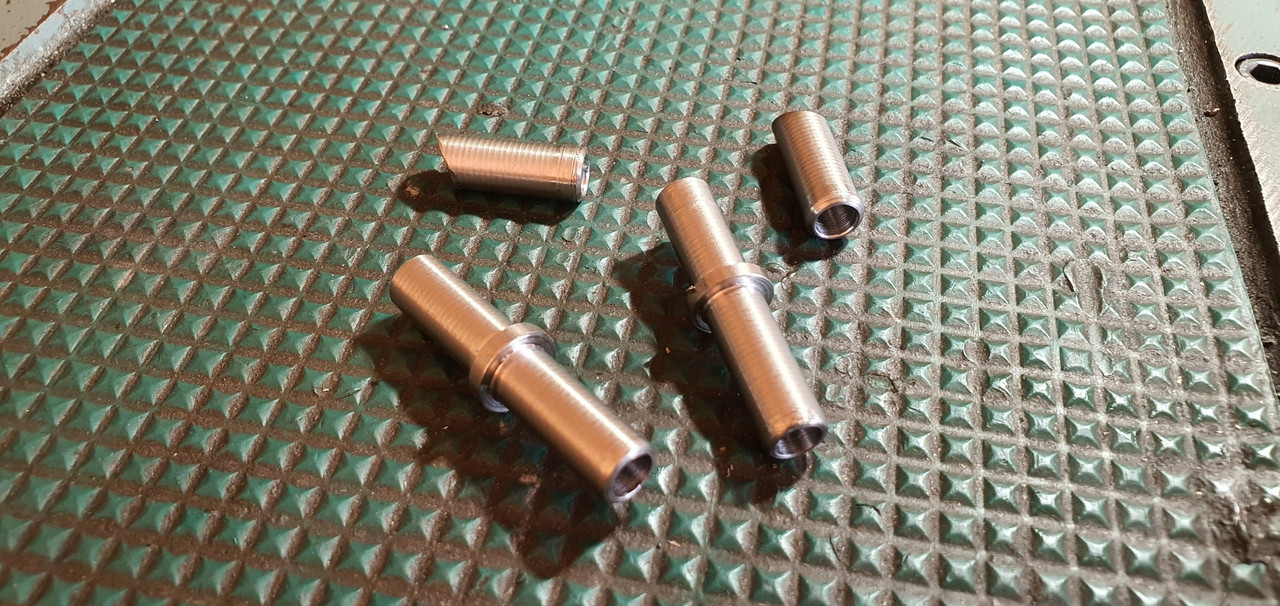
Thought of a neat way to hold the little bits together for tacking. Blue tack. Or blue tack tack?
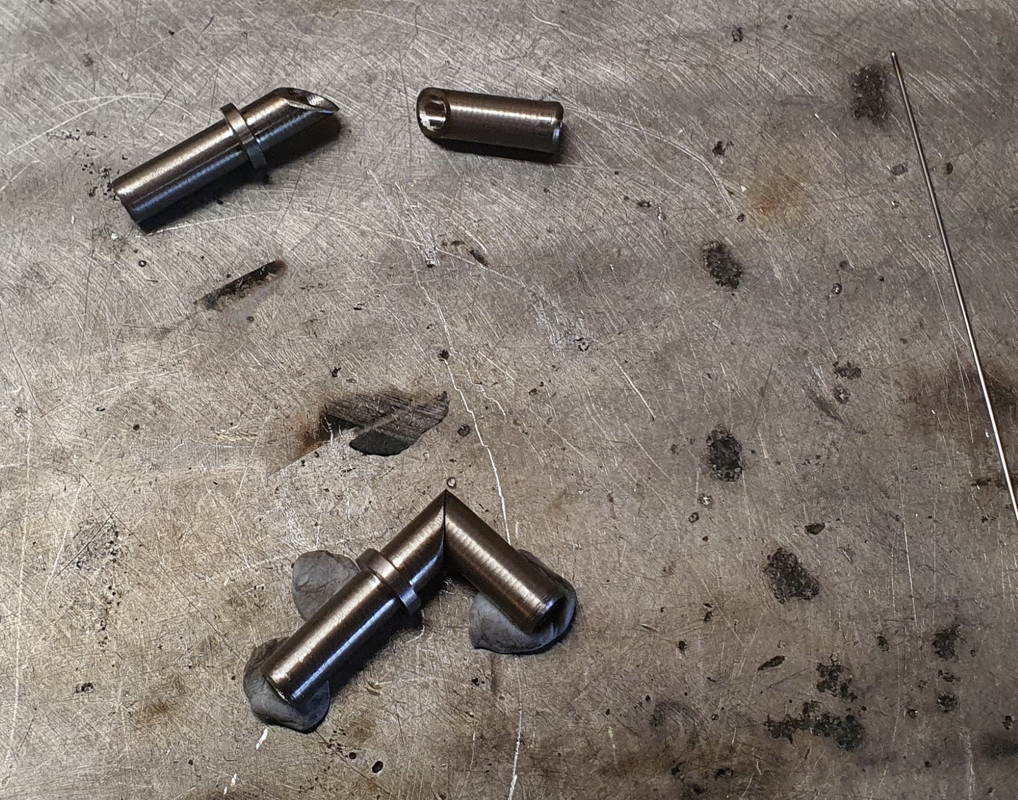
welded up..
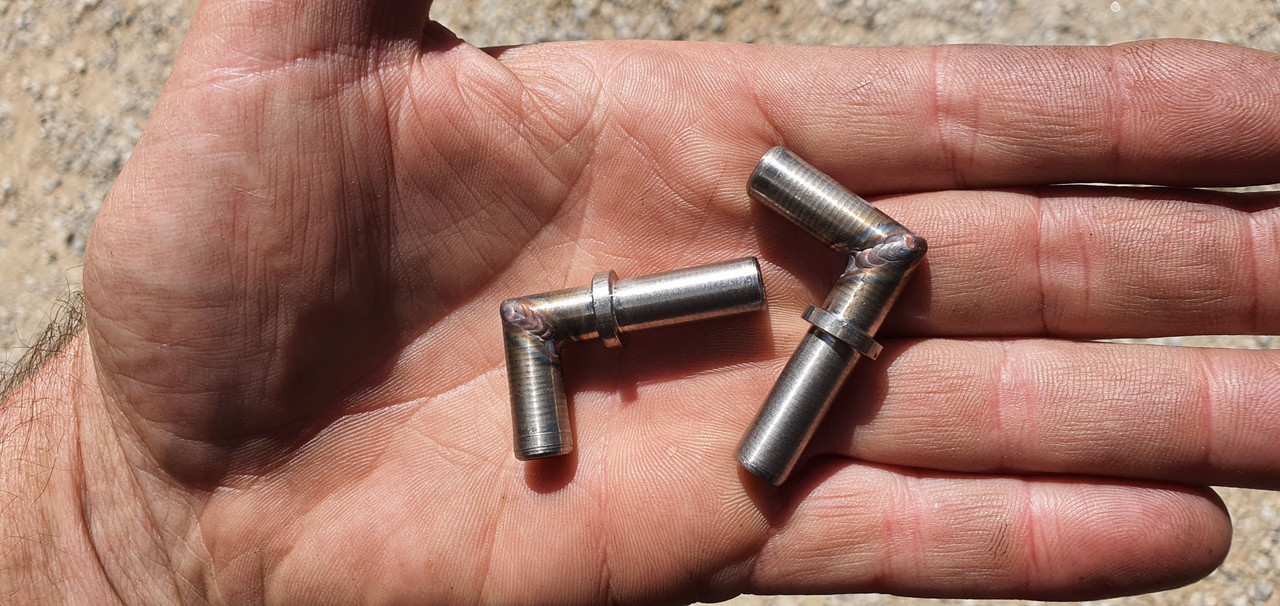
I made an angled recess into the hatch cover so the fuel hose goes even further below the tank line.
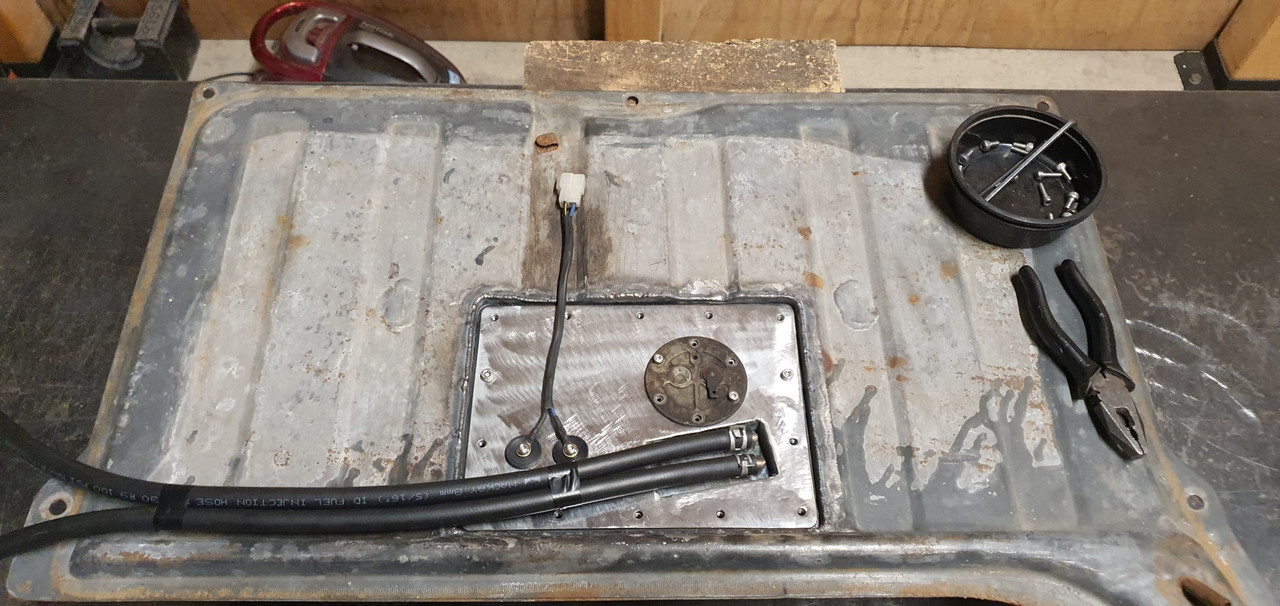
Visible in that photo are the cable connections. Again - I needed to get power in. I machined some shouldered fittings in plastic..
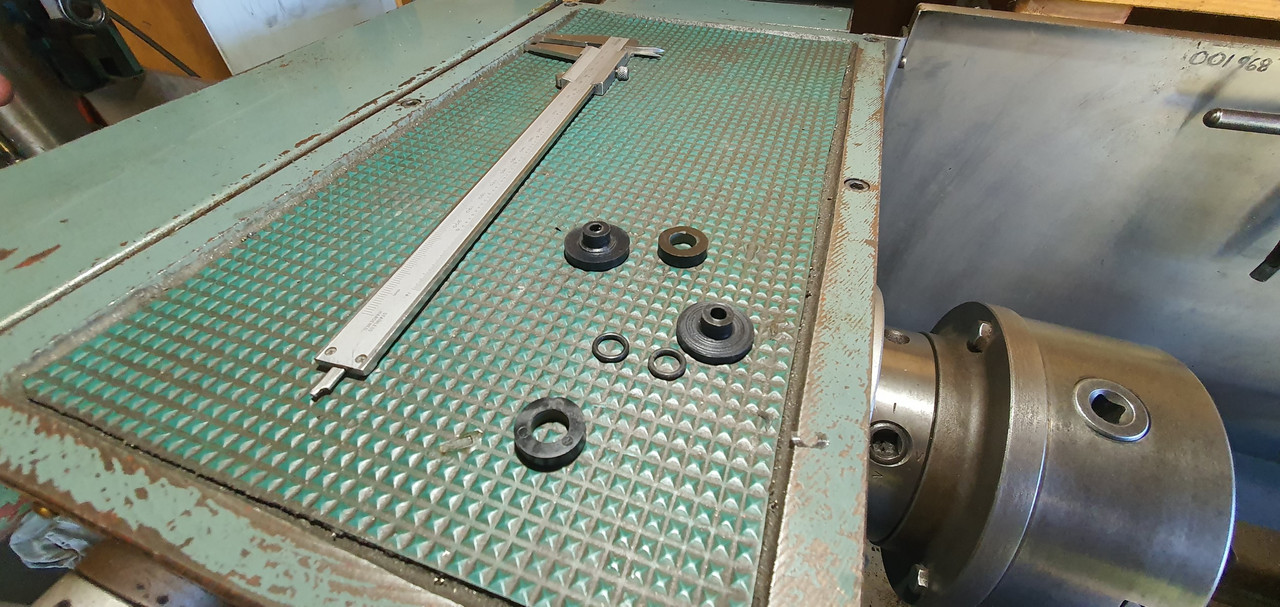
Luckily the micra pump so handily just uses a simple connector with 6.3 spade terminals.
Under the lid...
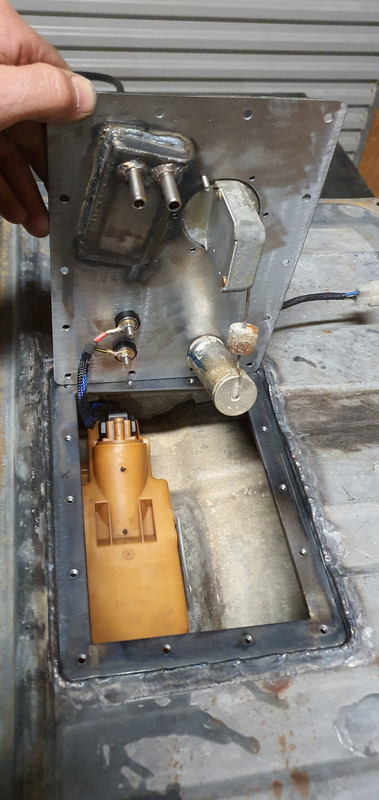
Tank hard work done. I'll paint bits and cut some gaskets.
Speaking of gaskets. One of mine between my oil filter pedestal and the block is weeping oil. Plus one of the bolt heads weeps. Typical. Put a Japanese engine in a British car and turn your back for a minute...
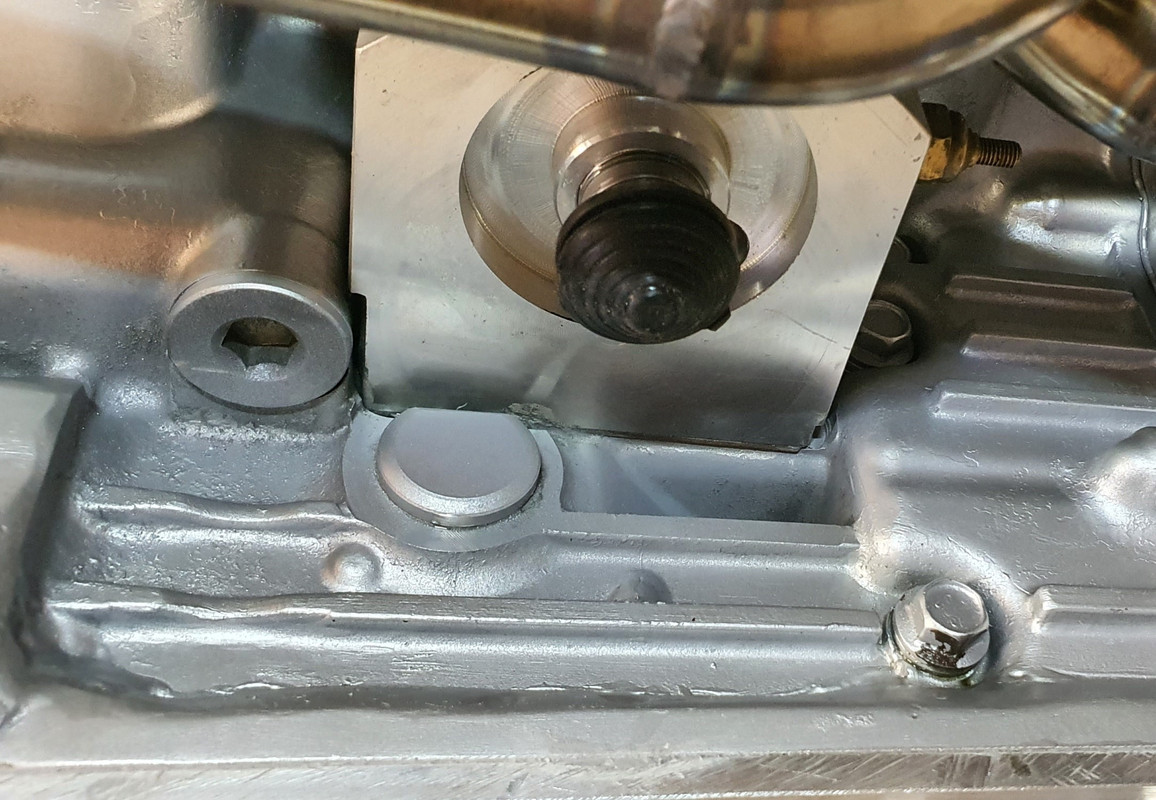
I've already drained the oil cleaned it up and ran a smear of paintable sikaflex along it and around the bolt head. I didn't take photos because not really exciting. I'll paint it silver and no one will know.
Except you the reader.