1975 914 1.8 Restoration
Moderator: Bootsy
Re: 1975 914 1.8 Restoration
I'm easily persuaded !!
Porsche 964 1993
Porsche 944 1986 - sold
Porsche 914 1972
Porsche 944 1986 - sold
Porsche 914 1972
Re: 1975 914 1.8 Restoration
I've not made as much progress as I would have liked with my 914 since my last update, which was almost a year ago (embarassingly). However, I have made some progress, so an update of my DDK thread is rather overdue.
After looking at the many rotisserie designs available, every one I looked at had features which I thought I would modify if I bought it. Most of them only seemed to be available via ebay, and there seemed to be a considerable amount of competition between their makers to make the cheapest. Some looked ridiculously flimsy to me, and others were not bad designs, and seemed reasonable value for money, at around £400.
The biggest let down of all the designs I saw was that whoever came up with them seems to have given little or no consideration to making them easy to store without wasting lots of space when not in use. Most seemed to have sacrificed disassembleability for low cost, with very awkward to store fabrications. In the end I decided to make one, by converting parts I had already made for the modular stillage / trolley I'd made the the body shell when it went to be stripped. I also decided to include bearings so it is as easy as possible to turn the shell, with the idea being that is little of the welding as possible would need to be done 'out of position' if the shell was very easy to turn.
The end result cost maybe an extra £250 in box section, bearings and laser cut parts, and all breaks down ito long straight parts or small fabrications for storage whenever I get the bodywork finished:
I decided to pick up on the suspension mouints at the front rather then the bumper mounts, as they needed no restoration, and I hadn't decided at the time exactly how I was going to mount the early front bumpers I'm converting to, or whether they would be steel or fibreglass:
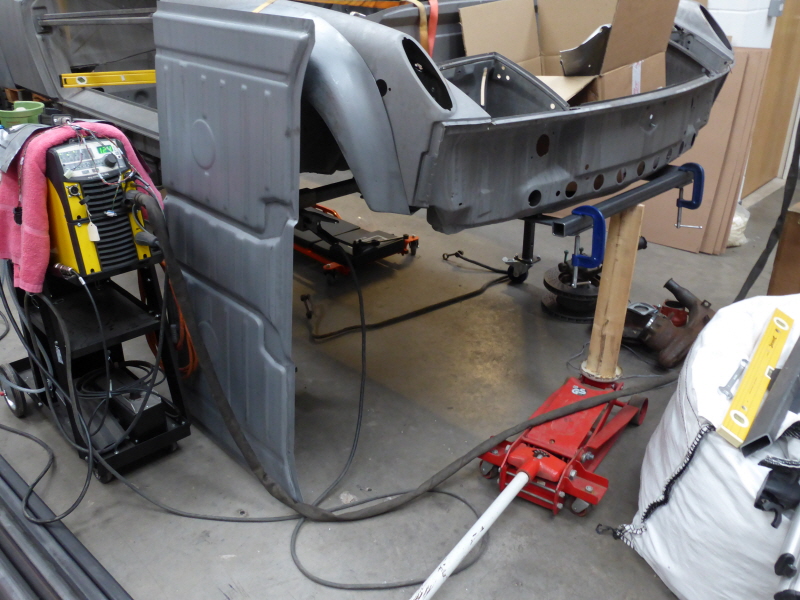
The beginnings of a foldable 'A frame' with an indexable plate on the FWD rear wheel bearing assemblies which the shell will pivot on:
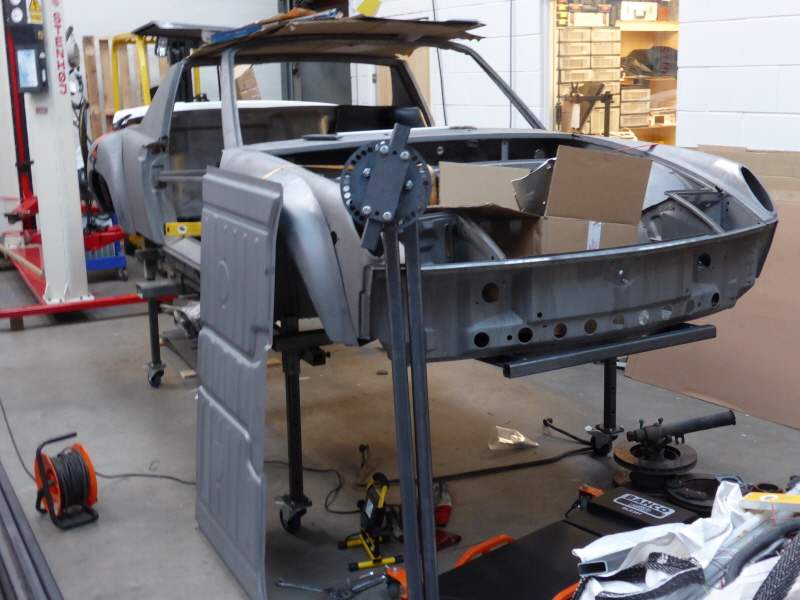
Here it is assembled. The height at which the front of the shell pivots is adjustable, currently by slackening bolts and jacking the shell up or down. A screw thread adjuster would be a nice add on, but probably not with the effort. The round steel discs on the tube sticking out to the right at the front make a sliding counterweight which gives fine adjustment of the C of G. A gate latch bolt locates in the indexing plate every 10 degrees:
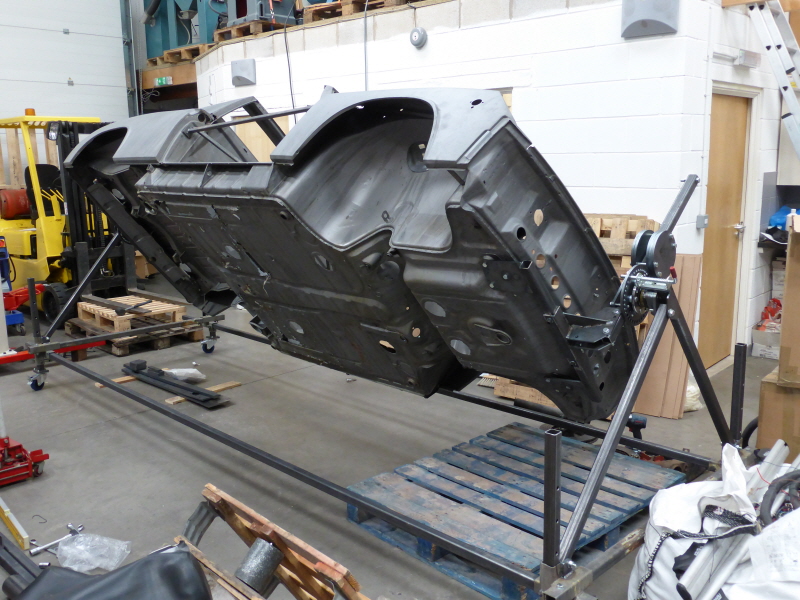
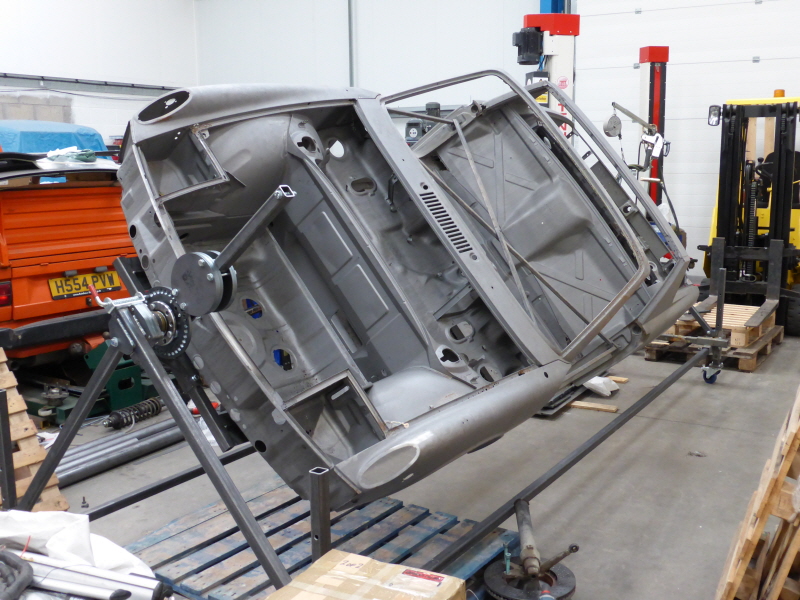
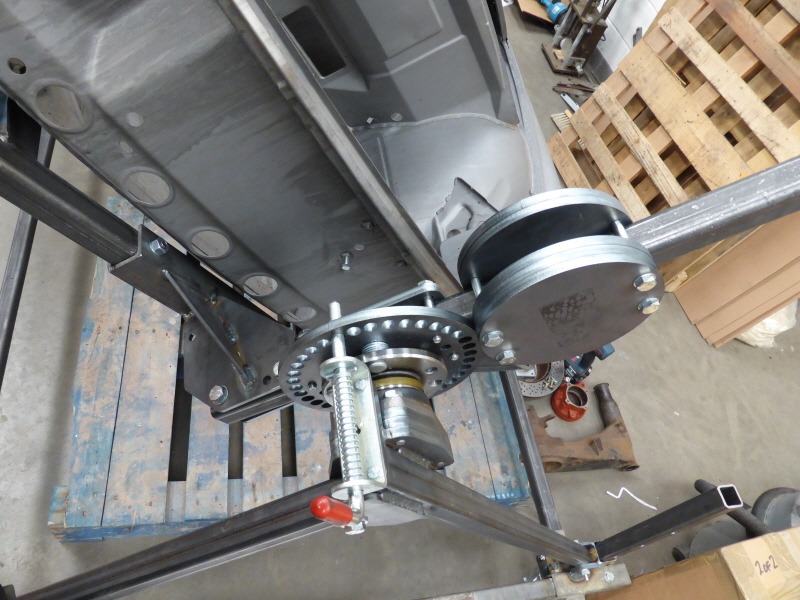
After a bit of playing around with the coarse and fine adjustment, I got the C of G spot on. If I spin the shell, it carries on rotating for a good few minutes. At first this was just amusing, but it had an unexpected advantage. All sorts of bits were falling on the floor from inside the closed sections in the shell. Almost all ash from the pyrolysis oven. I kept spinning it, for maybe half an hour, and afterwards swept up maybe half a dust pan of bits.
Many months after finishing the rotisserie, I finally had time to make a start on the bodywork. However, even before welding anything on the shell, I decided to put a couple of days practice into tig welding 0.9mm steel to find the optimum tig settings and procedures.
My best results were with pulsed tig, using very short bursts of about 80A, followed by a long gap. This effectively produces a series of overlapping tacks, with time inbetween each pulse to move and reposition if the access is awkward, while putting in minimal heat.
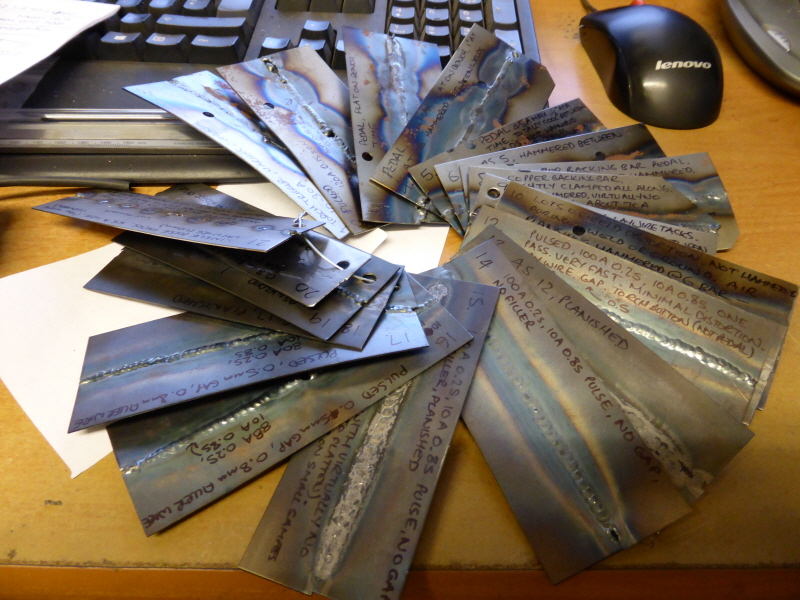
My tig experimenting showed four real revelations (to me!), so were time well spent before doing any actual bodywork:
1. Using copper backing bars. I expected them to work well, having never tried before, but they proved far more useful than I expected. If they can be clamped up to the work tightly enough, it was possible to get rid of almost all the distortion, as the copper sucks almost all of the heat out of the surrounding steel despite a far higher welding current being needed.
2. How copper backing bars allow a gap between two thin panels to be filled, say if two panels are not a perfect fit together. I bridged a gap of around double the steel thickness, and got a neat weld too. Pretty sure I couldn't do that without the copper block behind the weld.
3. How much difference getting the tig filler wire size just right makes on thick sheet steel weld. I'd started out using 1mm ER70S, as it's the thinnest I can get easily, but it was still a bit too thick. Using straightened 0.8mm mig wire was far better (It's really easy to straighten by twisting it while in tension until it yields, which is at about 30 turns per metre - thanks Youtube).
4. Using a pedal. I've had a pedal for my tig for many years, but have never really got on that well with using it. Probably because I had learned to tig without having a pedal. However, the pedal has proven invaluable for tiging bodywork. Especially for initial tacking, which I don't find easy at all without using the pedal.
5. The 5th revelation was not to do with the actual welding, but how effective planishing tig but welds in bodywork can be. I’d bought the cheapest air planishing hammer I could find – the one everyone on US forums refers to as the ‘Harbour Freight’ planishing hammer. It was something like £100 inc VAT & delivery, new, so my expectations were not high. After changing the top tool for a flat one with no rubber grommet edge (sold as a riveter tool for an air chisel by numerous Chinese ebay sellers), and making a flat bottom tool from EN24, I tried using it to planish tig but welds. The results were amazing to me. It is relatively easy to get rid of all the distortion by hammering the weld bead flat, without stretching the base metal, and doing so gets rid of any need to grind the weld bead:

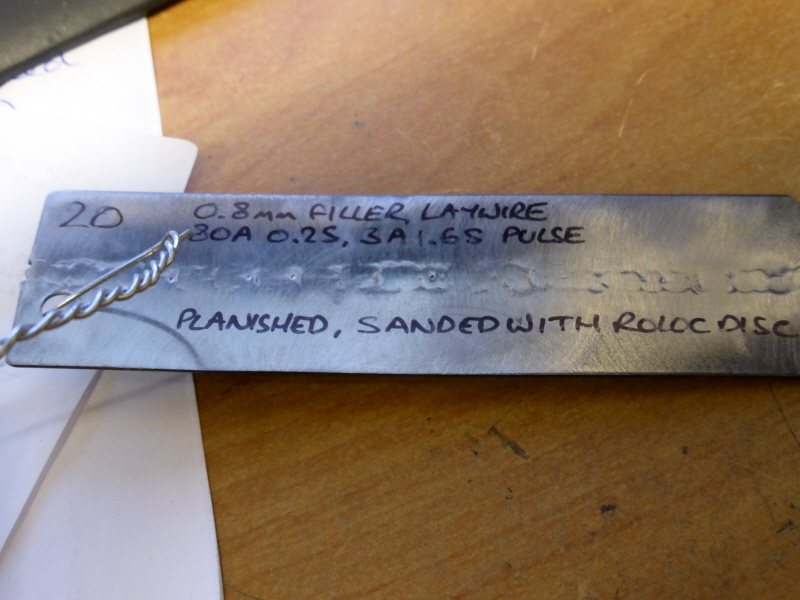
I have taken all the photos of the actual bodywork progress so far, but don't have time to write up and upload then at the moment. I'll try to get that done in the next couple of days.
After looking at the many rotisserie designs available, every one I looked at had features which I thought I would modify if I bought it. Most of them only seemed to be available via ebay, and there seemed to be a considerable amount of competition between their makers to make the cheapest. Some looked ridiculously flimsy to me, and others were not bad designs, and seemed reasonable value for money, at around £400.
The biggest let down of all the designs I saw was that whoever came up with them seems to have given little or no consideration to making them easy to store without wasting lots of space when not in use. Most seemed to have sacrificed disassembleability for low cost, with very awkward to store fabrications. In the end I decided to make one, by converting parts I had already made for the modular stillage / trolley I'd made the the body shell when it went to be stripped. I also decided to include bearings so it is as easy as possible to turn the shell, with the idea being that is little of the welding as possible would need to be done 'out of position' if the shell was very easy to turn.
The end result cost maybe an extra £250 in box section, bearings and laser cut parts, and all breaks down ito long straight parts or small fabrications for storage whenever I get the bodywork finished:
I decided to pick up on the suspension mouints at the front rather then the bumper mounts, as they needed no restoration, and I hadn't decided at the time exactly how I was going to mount the early front bumpers I'm converting to, or whether they would be steel or fibreglass:
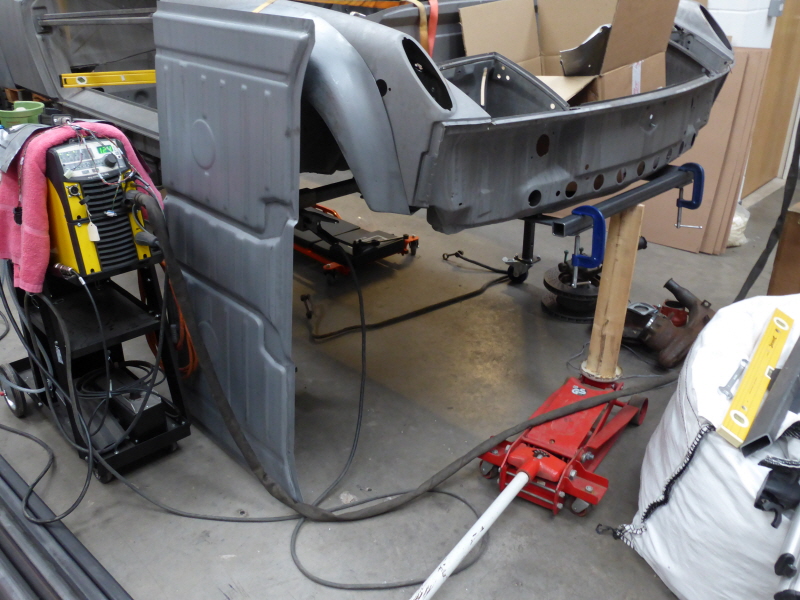
The beginnings of a foldable 'A frame' with an indexable plate on the FWD rear wheel bearing assemblies which the shell will pivot on:
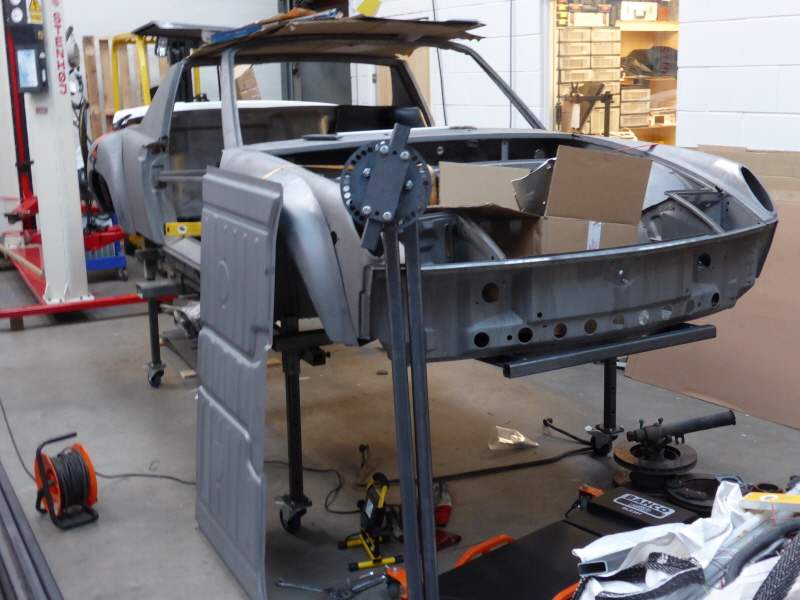
Here it is assembled. The height at which the front of the shell pivots is adjustable, currently by slackening bolts and jacking the shell up or down. A screw thread adjuster would be a nice add on, but probably not with the effort. The round steel discs on the tube sticking out to the right at the front make a sliding counterweight which gives fine adjustment of the C of G. A gate latch bolt locates in the indexing plate every 10 degrees:
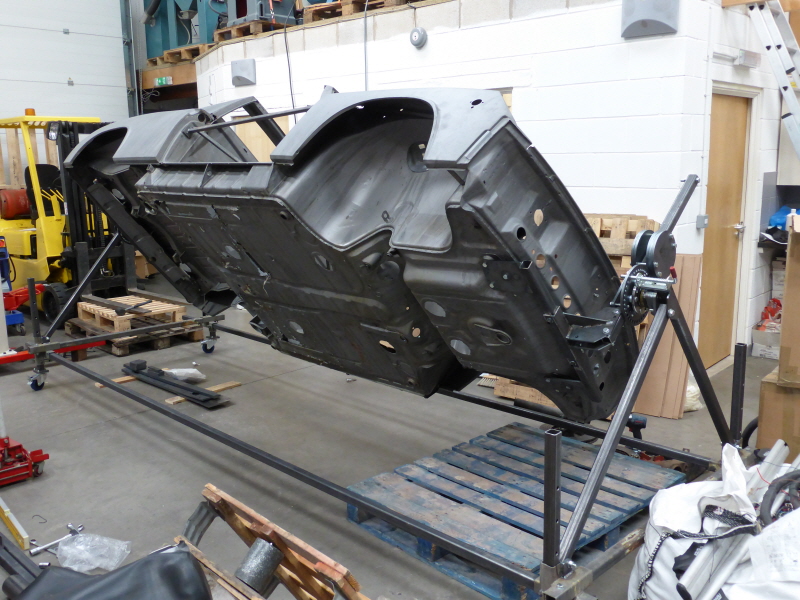
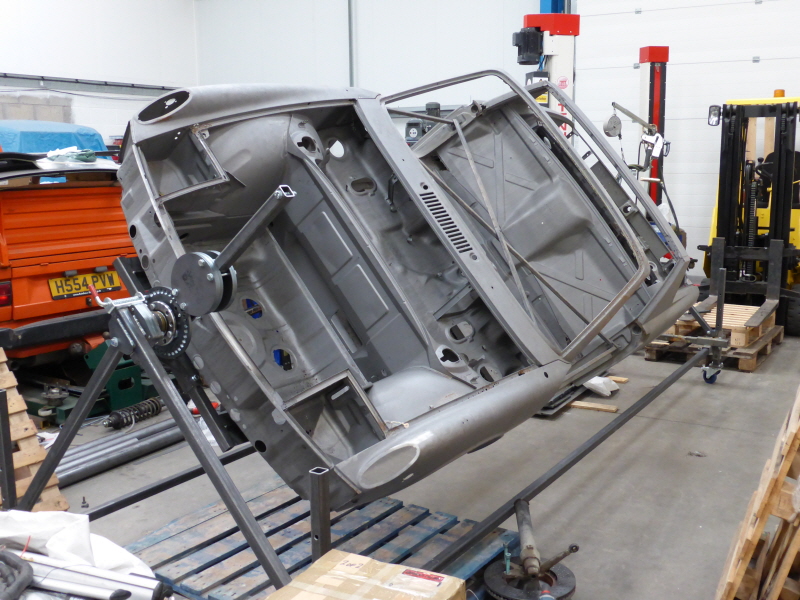
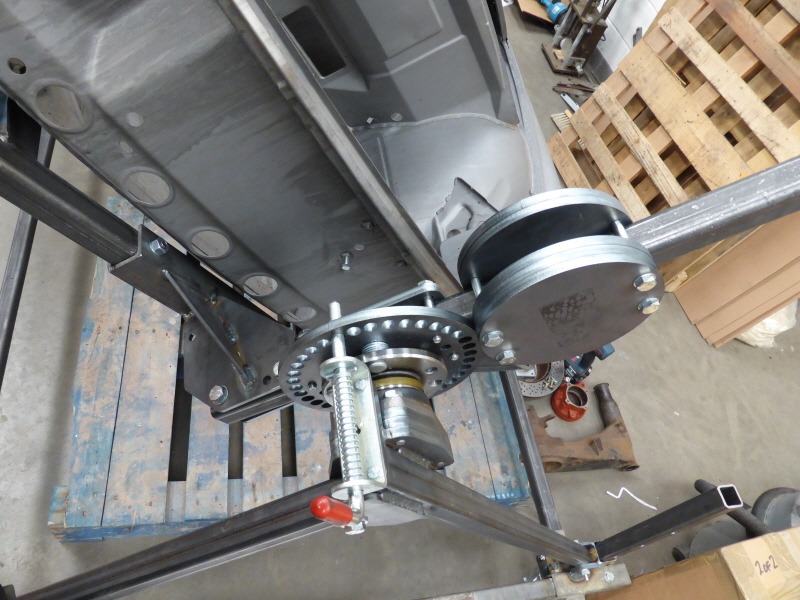
After a bit of playing around with the coarse and fine adjustment, I got the C of G spot on. If I spin the shell, it carries on rotating for a good few minutes. At first this was just amusing, but it had an unexpected advantage. All sorts of bits were falling on the floor from inside the closed sections in the shell. Almost all ash from the pyrolysis oven. I kept spinning it, for maybe half an hour, and afterwards swept up maybe half a dust pan of bits.
Many months after finishing the rotisserie, I finally had time to make a start on the bodywork. However, even before welding anything on the shell, I decided to put a couple of days practice into tig welding 0.9mm steel to find the optimum tig settings and procedures.
My best results were with pulsed tig, using very short bursts of about 80A, followed by a long gap. This effectively produces a series of overlapping tacks, with time inbetween each pulse to move and reposition if the access is awkward, while putting in minimal heat.
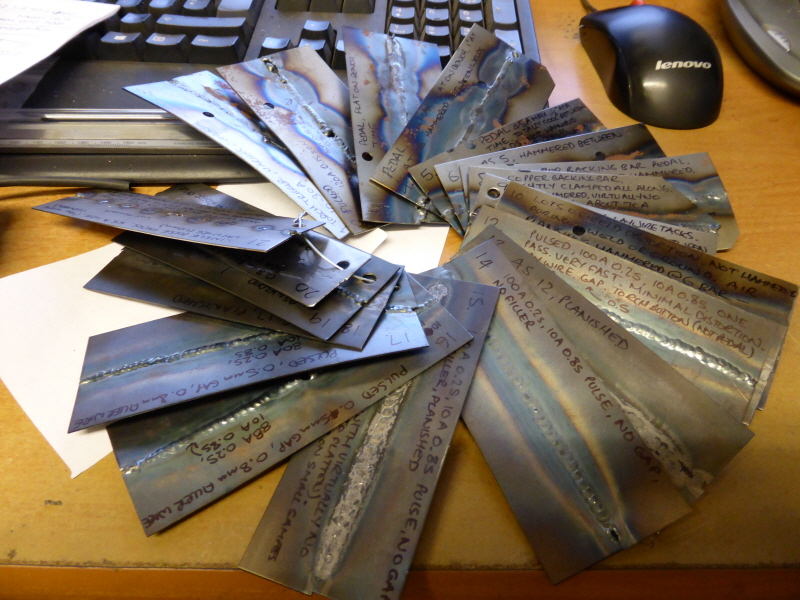
My tig experimenting showed four real revelations (to me!), so were time well spent before doing any actual bodywork:
1. Using copper backing bars. I expected them to work well, having never tried before, but they proved far more useful than I expected. If they can be clamped up to the work tightly enough, it was possible to get rid of almost all the distortion, as the copper sucks almost all of the heat out of the surrounding steel despite a far higher welding current being needed.
2. How copper backing bars allow a gap between two thin panels to be filled, say if two panels are not a perfect fit together. I bridged a gap of around double the steel thickness, and got a neat weld too. Pretty sure I couldn't do that without the copper block behind the weld.
3. How much difference getting the tig filler wire size just right makes on thick sheet steel weld. I'd started out using 1mm ER70S, as it's the thinnest I can get easily, but it was still a bit too thick. Using straightened 0.8mm mig wire was far better (It's really easy to straighten by twisting it while in tension until it yields, which is at about 30 turns per metre - thanks Youtube).
4. Using a pedal. I've had a pedal for my tig for many years, but have never really got on that well with using it. Probably because I had learned to tig without having a pedal. However, the pedal has proven invaluable for tiging bodywork. Especially for initial tacking, which I don't find easy at all without using the pedal.
5. The 5th revelation was not to do with the actual welding, but how effective planishing tig but welds in bodywork can be. I’d bought the cheapest air planishing hammer I could find – the one everyone on US forums refers to as the ‘Harbour Freight’ planishing hammer. It was something like £100 inc VAT & delivery, new, so my expectations were not high. After changing the top tool for a flat one with no rubber grommet edge (sold as a riveter tool for an air chisel by numerous Chinese ebay sellers), and making a flat bottom tool from EN24, I tried using it to planish tig but welds. The results were amazing to me. It is relatively easy to get rid of all the distortion by hammering the weld bead flat, without stretching the base metal, and doing so gets rid of any need to grind the weld bead:

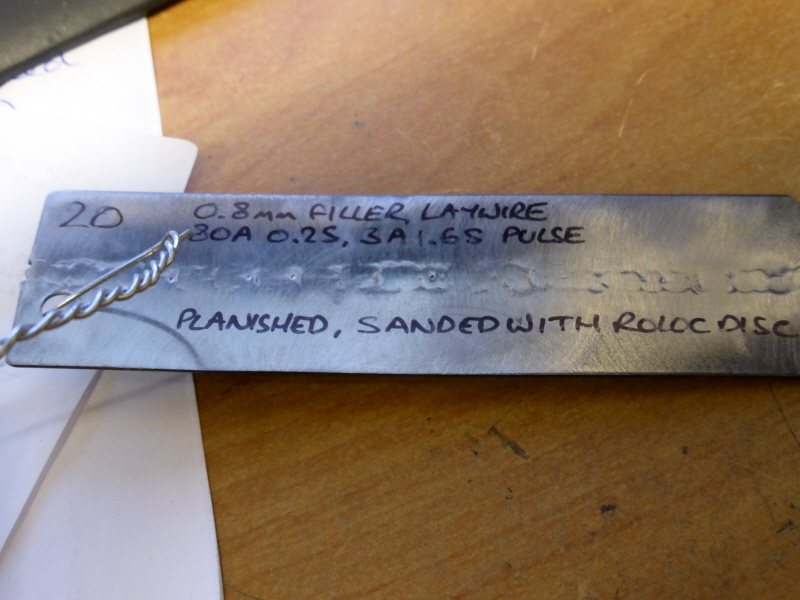
I have taken all the photos of the actual bodywork progress so far, but don't have time to write up and upload then at the moment. I'll try to get that done in the next couple of days.
Regards,
RichardJ
1975 California spec 914 1.8 restoration project
RichardJ
1975 California spec 914 1.8 restoration project
Re: 1975 914 1.8 Restoration
Great update Richard and very informative about the welding techniques.
Nathan
1975 914/4 1.8 (Needing Resto!)
2008 Cayenne GTS
1993 993 Carrera 2
1967 VW Beetle 1300 (In loads of pieces!)
1975 914/4 1.8 (Needing Resto!)
2008 Cayenne GTS
1993 993 Carrera 2
1967 VW Beetle 1300 (In loads of pieces!)
-
- DDK 1st, 2nd and 3rd for me!
- Posts: 2237
- Joined: Mon May 24, 2004 10:54 pm
- Location: london/surrey
Re: 1975 914 1.8 Restoration
Love the careful experiments with welding settings..
1974 2.7 Carrera
(full restoration. now as an RS Touring)
1963 3.8 E Type
( 11 years in the making…………………….)
1952. XK120…the next one ……….……..)
(full restoration. now as an RS Touring)
1963 3.8 E Type
( 11 years in the making…………………….)
1952. XK120…the next one ……….……..)
-
- Put a fork in me, I'm done!
- Posts: 1717
- Joined: Sat Aug 05, 2006 7:02 pm
- Location: Rochford, Essex
Re: 1975 914 1.8 Restoration
Excellent stuff. I hope we see more of this project soon.
Re: 1975 914 1.8 Restoration
Thanks. Another update with quite a few pics for now, but then it’ll be back to slow progress, as this is where I am currently up to, rather than writing up work I did weeks or months ago:
Time to actually start the bodywork. I've started at the front end, with the bonnet seal lip repairs and early bumper conversion mods. The idea was to use these fiddly bits as tig welding practice, as I've never tig'ed bodywork before. Hopefully that way I'll be half decent at it before attempting more daunting task of butt welding in the GT arches in with minimal distortion. Replacing these rusty buts with new steel:
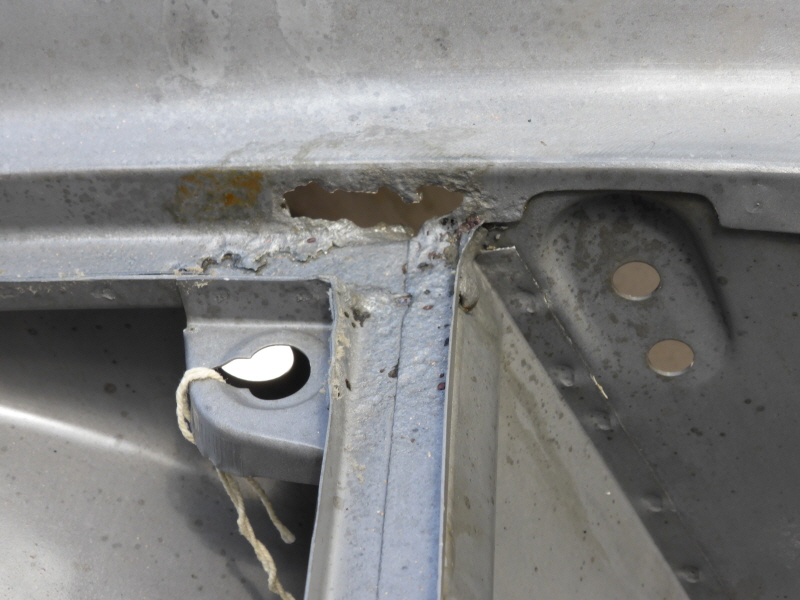
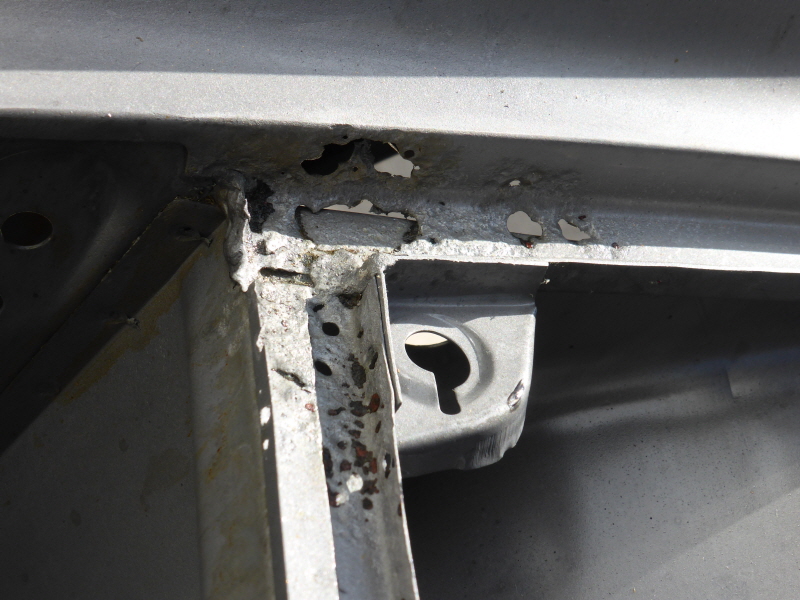
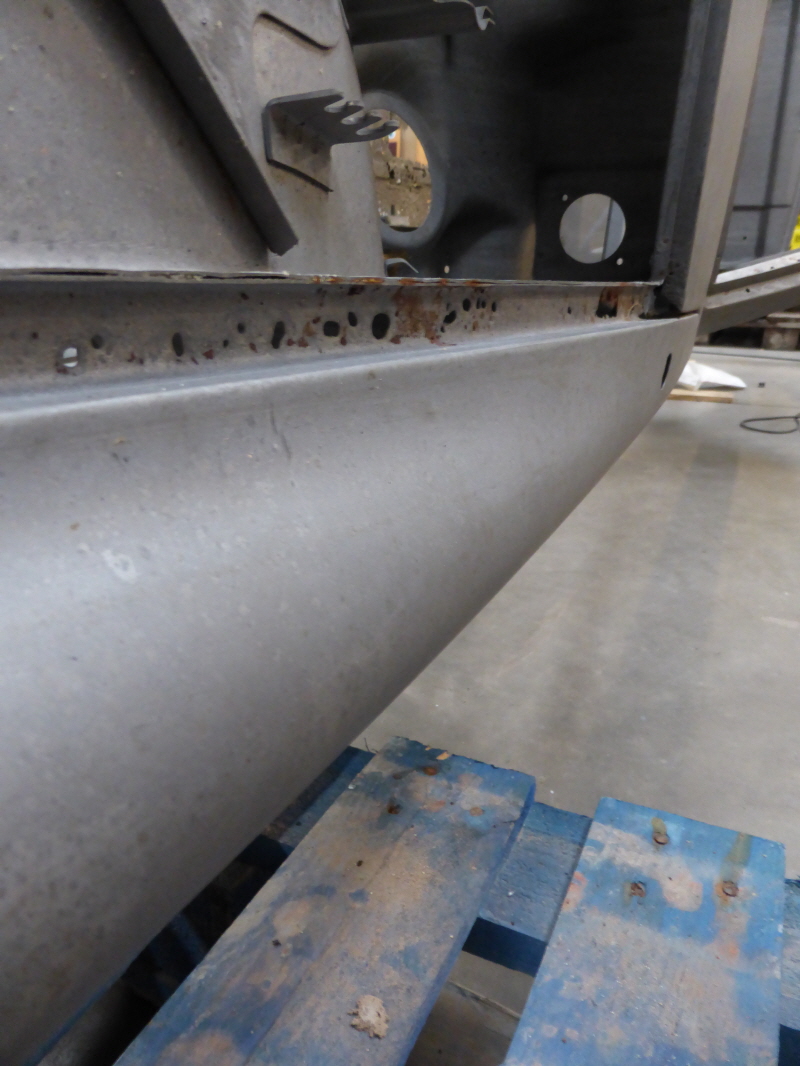
The cutting and spot weld drilling begins:
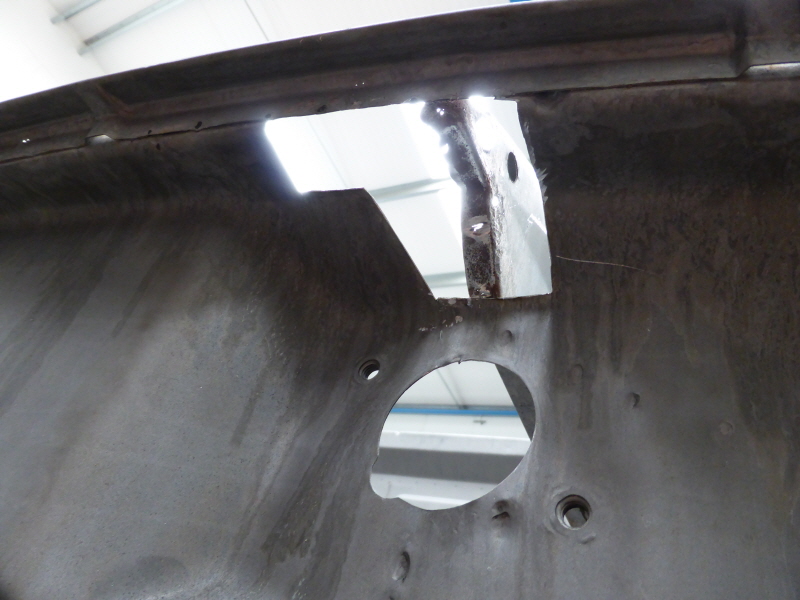
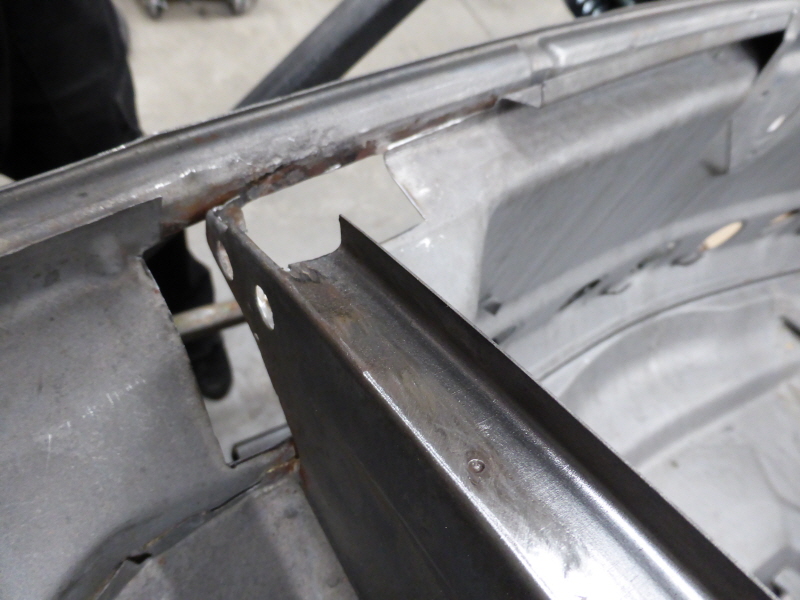
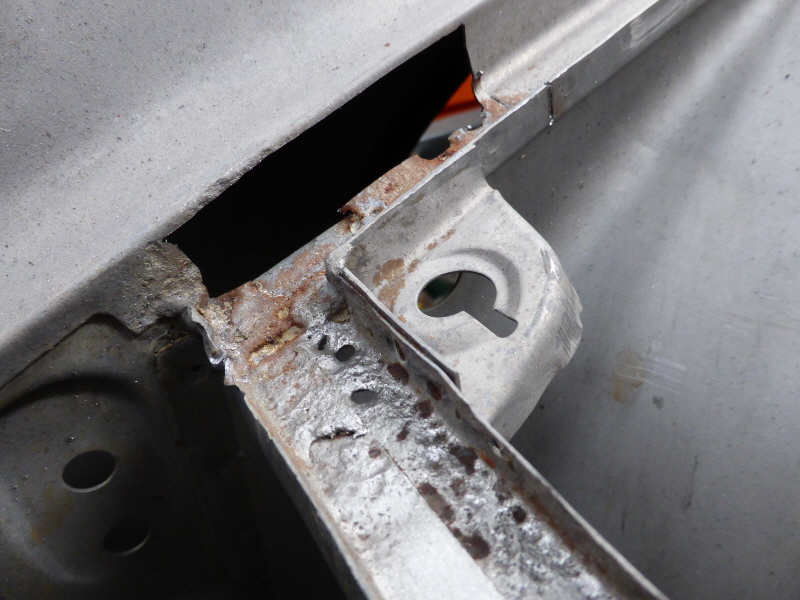
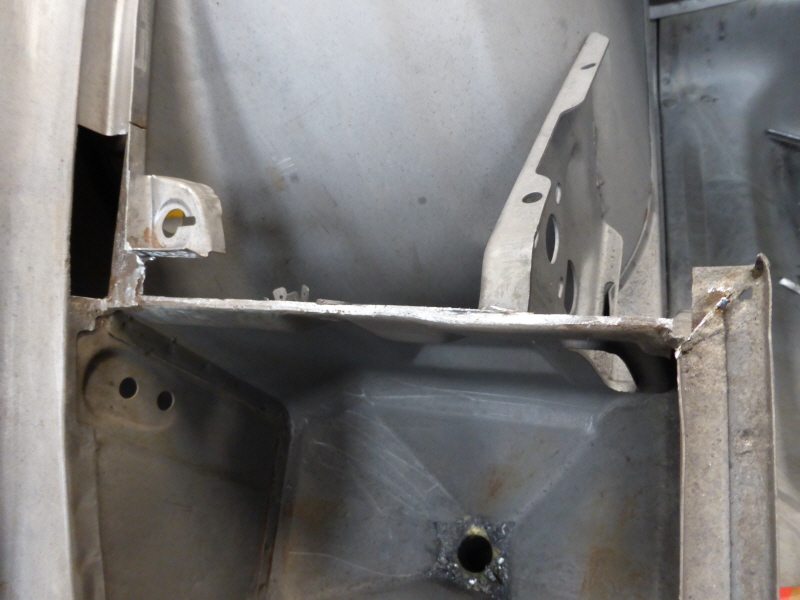
This was a pain to remove. Not wanting to damage the lip at the top of the inner wing (the new channel will be spot welded back in) meant grinding the spot welds out from inside the weather strip channel with a 3” grinding disc. Very tedious. At least cutting along the other side with a reciprocating saw was easy:
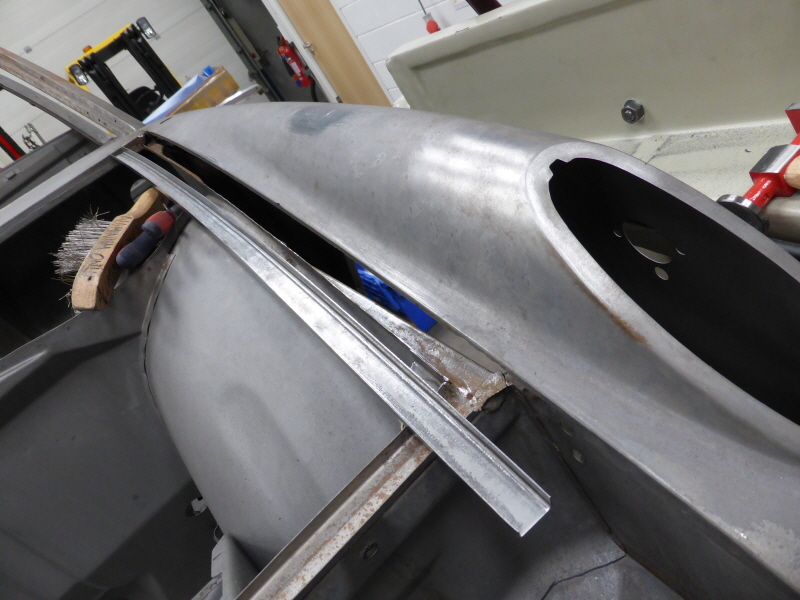
….and the fabricating:
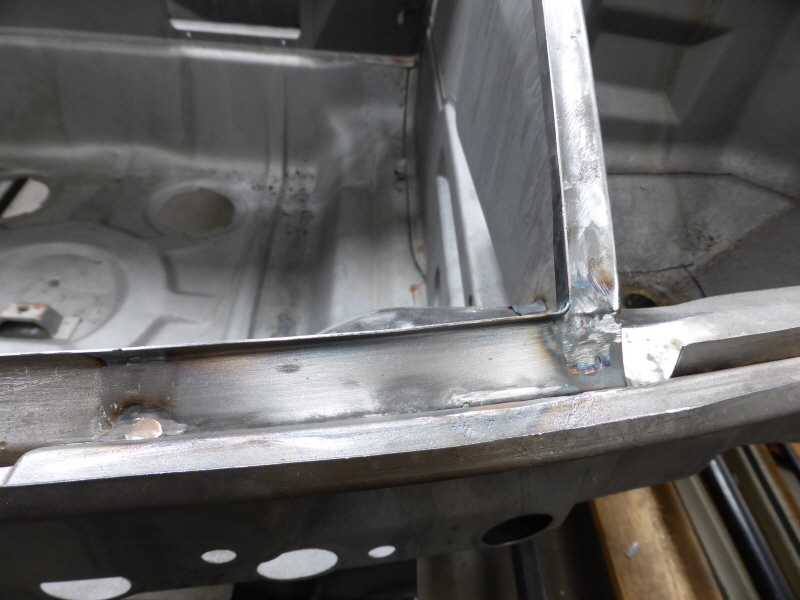
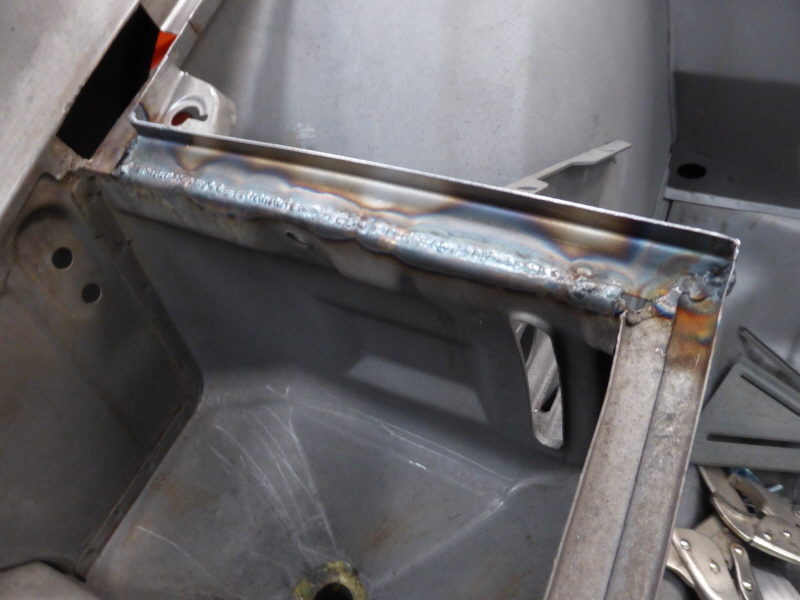
It seems Porsche / Karmann thought water flows uphill when designing the 914 bonnet weather seal channel, and the rust at all of the low points, even on a car which has spent all of its life in California or indoors in the UK, proves that it doesn’t. I have some mods planned to make sure water won’t be able to collect here again once it’s finished. As part of the early bumper conversion, I needed to at least remove the impact bumper retaining strip in front of the pop up lights:
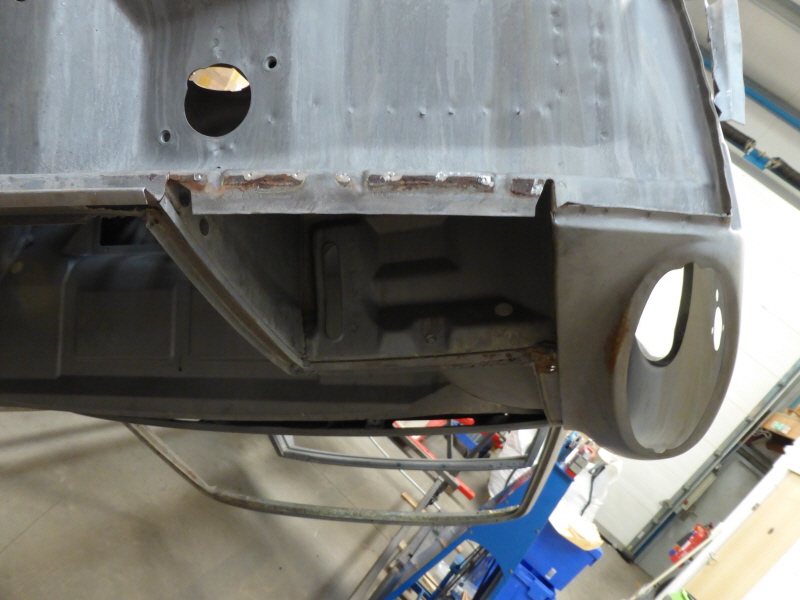
Welding up the marks left by the spot weld drill:
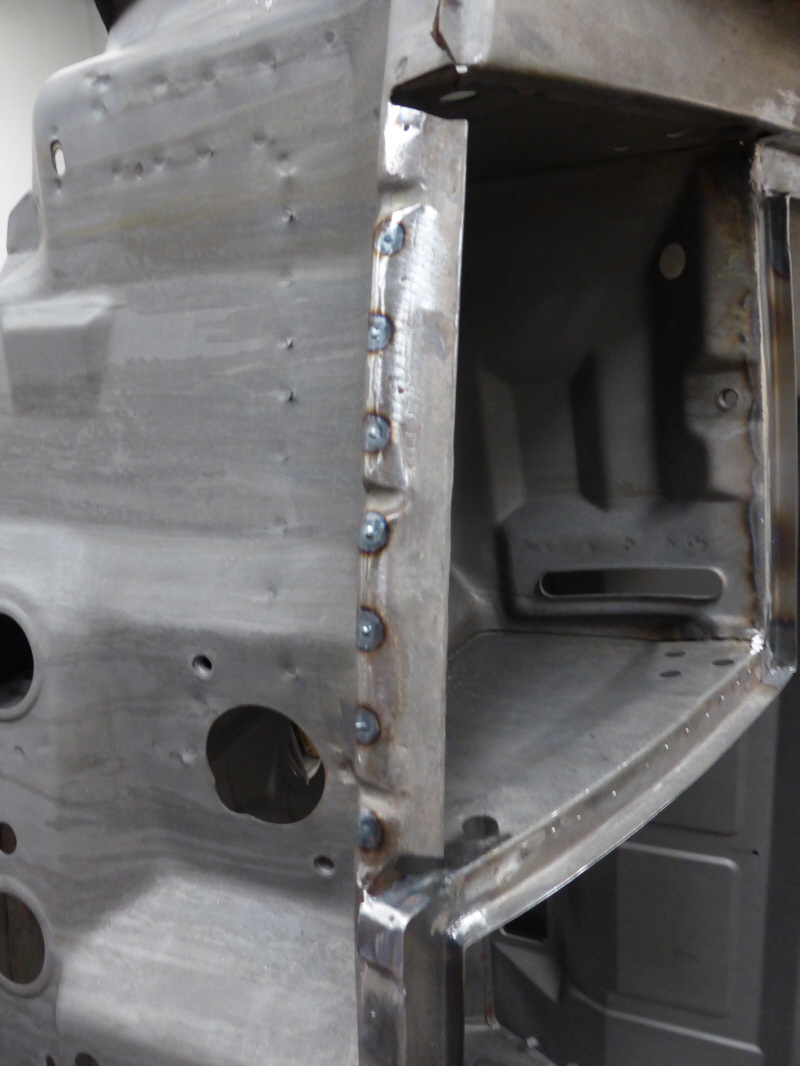
………. and cut it back along the front of the bonnet to resemble the weather strip channel on an early model. I thought about removing all of it, and replacing it with a 90 degree channel, like on the early models, however, this just introduced more undrained low spots. I decided to make the weather seal channel edge from the centre part of the impact bumper retaining strip, as it has 3 drainage channels (so not all of the impact bumper modifications on late models were bad!), and also to move the 2 other drainage channels which were originally in front of each headlight to the corners of the new weather strip channel edge:
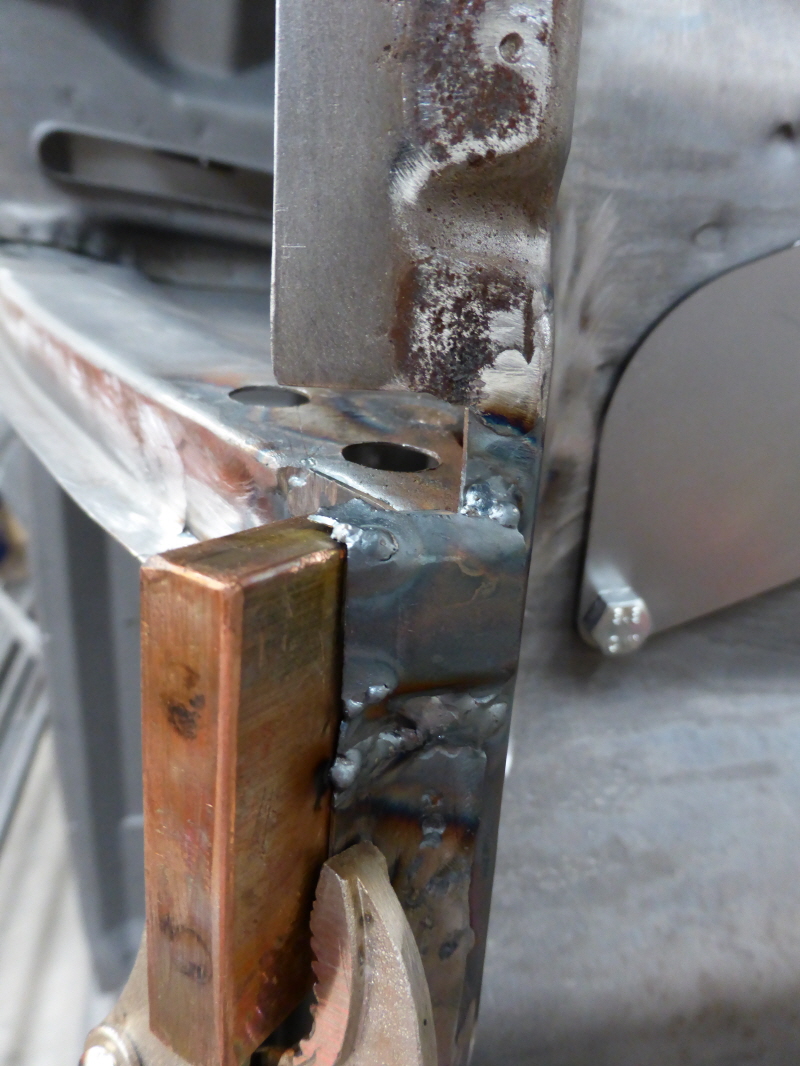
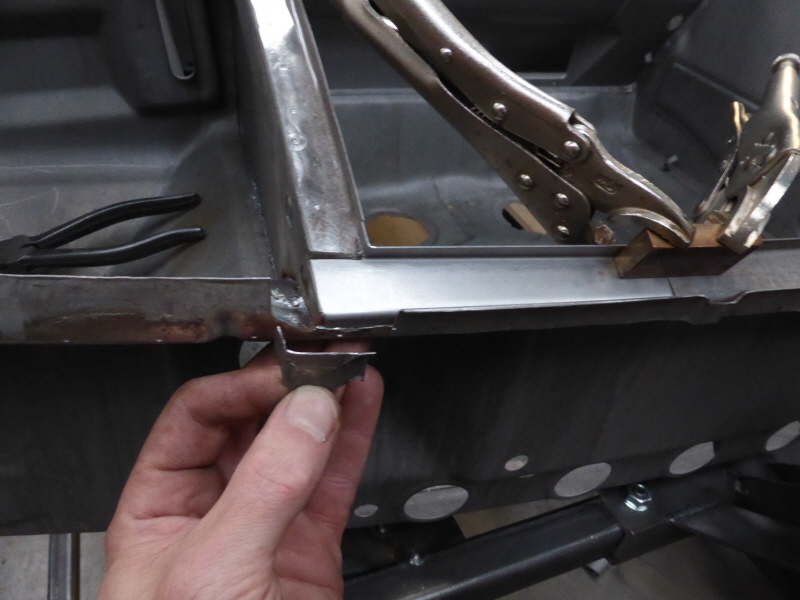
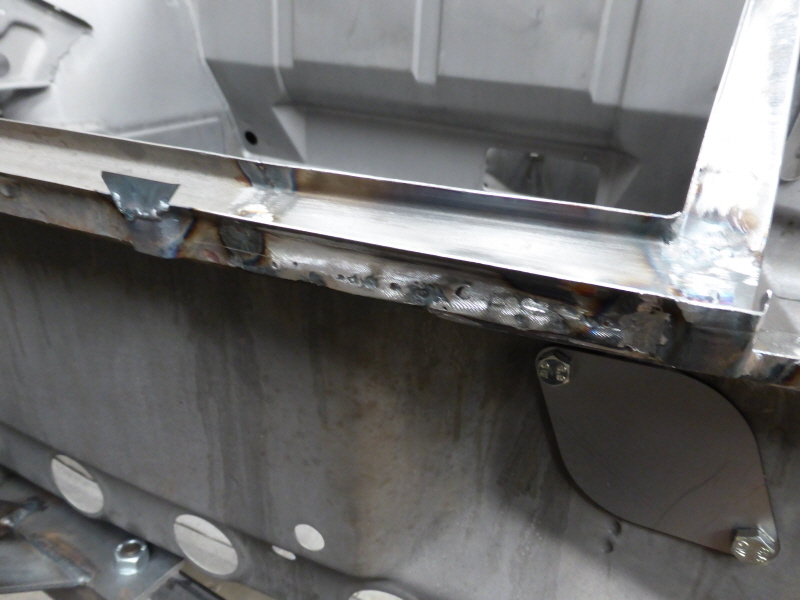
The two yellowish spots in the weld are where I’ve used silicone bronze tig wire to fill very localised pitting. Generally only where a tiny rust spot had left either very thin steel or a pinhole, and where cutting it out and welding a a new piece of steel would be more work, and not result in as neat an end result. I’d experimented with this (having never used silicone bronze before) on some very rusty remains of the floor, with good results:
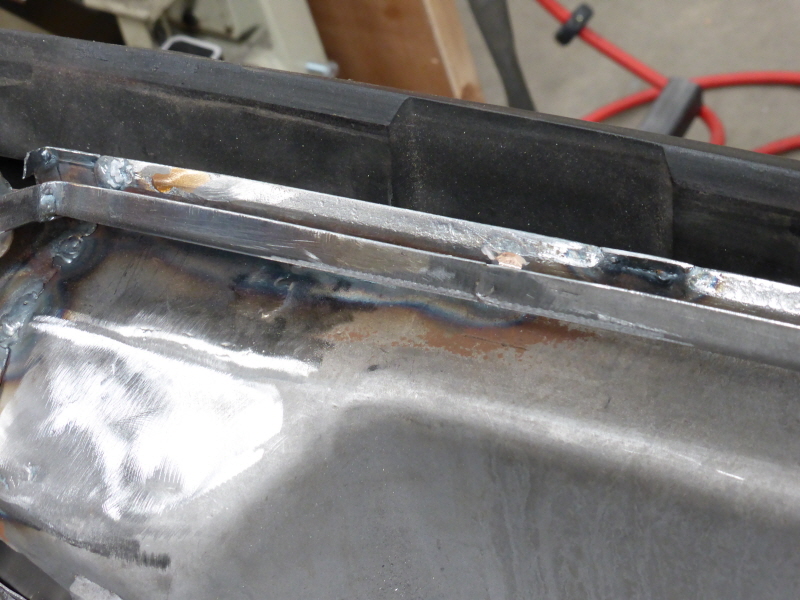
My first go at spot welding bodywork:
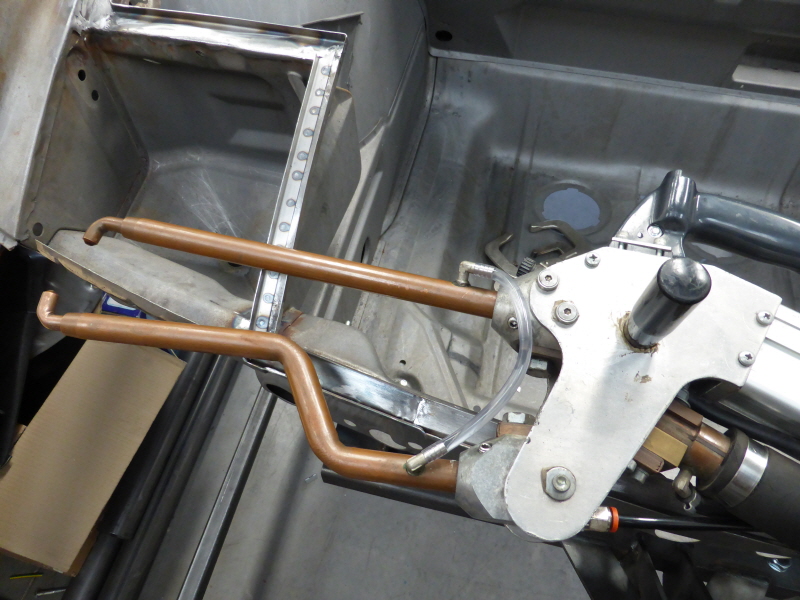
The weather seal channel repairs finished on one corner. I added 2 more drainage slots to the new channel edge at the rear of the headlight too:
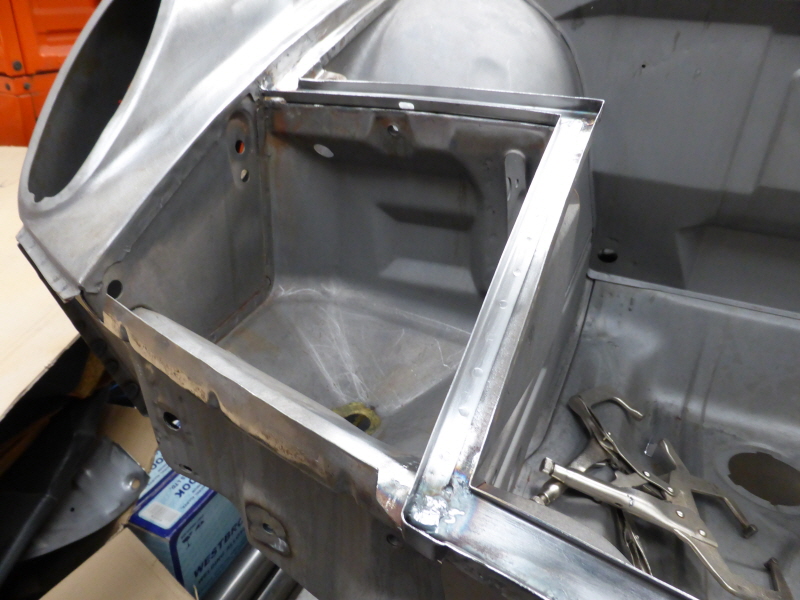
Removing the impact bumper retaining strips at the sides of the bumper:
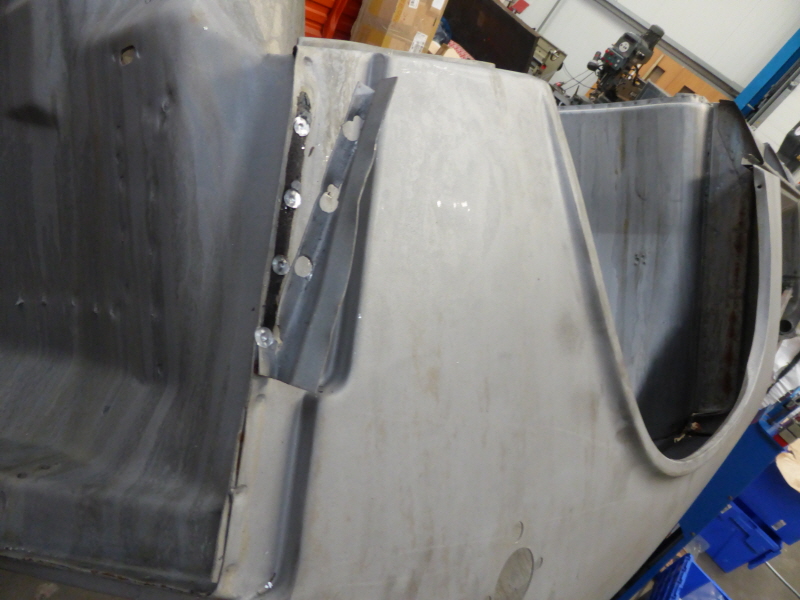
Trial fitting the early bumper mount reinforcing plates I made. I won’t weld them in until the wings are cut for the GT arches, as the access will be much better then. I messed up by copying the hole pattern for the plug welds to the inner wing from an early car, without realising the inner wing pressing is different on a late model. Of the 13 holes in the bracket, 7 of them have no steel behind them to weld to. I’ll either modify or re-make them to better suit the late model inner wings before they get welded on:
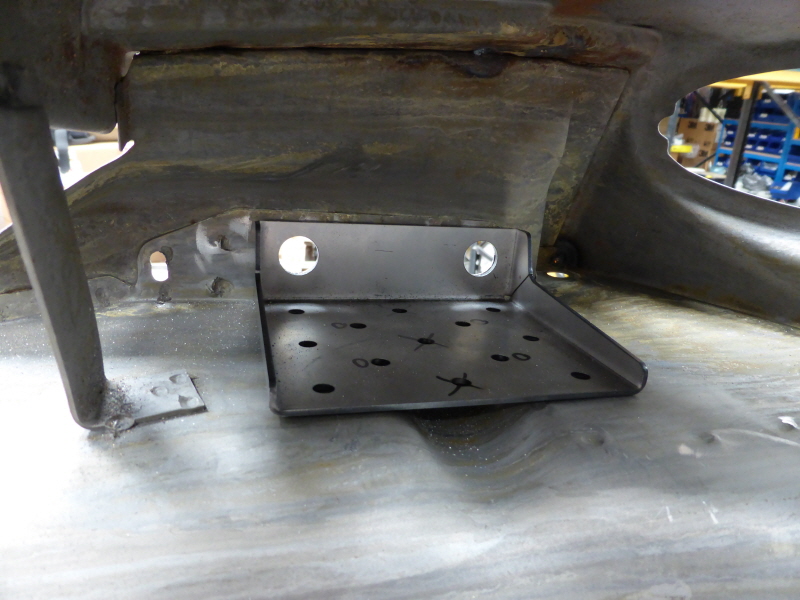
Going to trial fit the early bumper for the first time, I found that the RH fog light / horn grill nowhere near fitted the bumper. Strange, as they both appear to be original parts. I had to grind the bumper quite a bit to make enough room. Very pleased the extortionate prices put me off having the bumpers rechromed last year, as having to make more clearance for the grilles after spending so much on rechroming would have been unbelievably annoying:
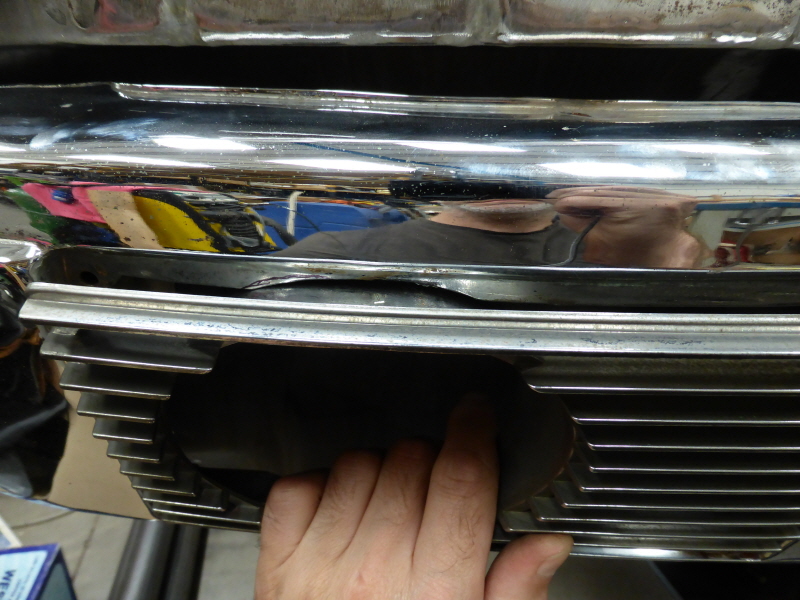
The early bumper bolted up for the first time. Sounds silly, as I know what an early model looks like, but it’s very satisfying seeing my late model start to look like one:
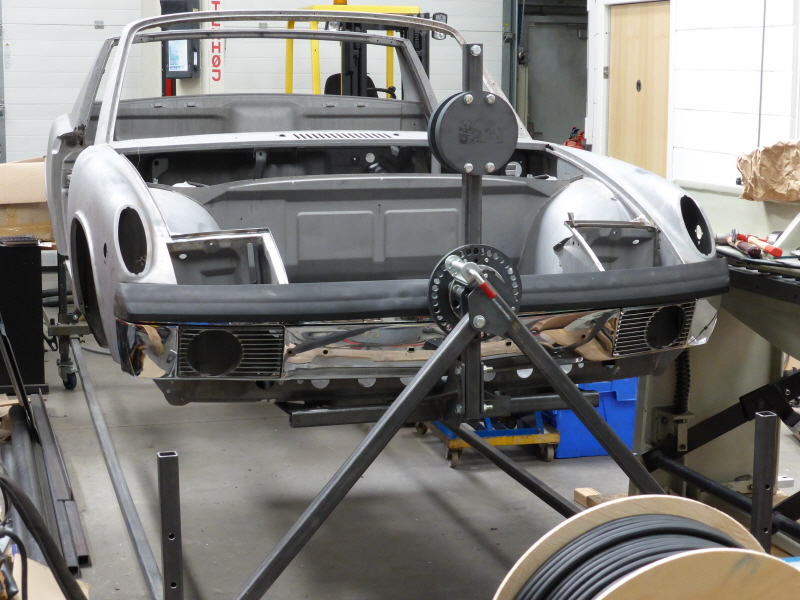
Hopefully the drainage channels I’ve added along the front of the weather seal channel won’t interfere with the fit of the bumper top. Unfortunately I can’t do a proper trial fit until the body is off the rotisserie, as I haven’t left enough space to trial fit the rubber top without it hitting the rotisserie:
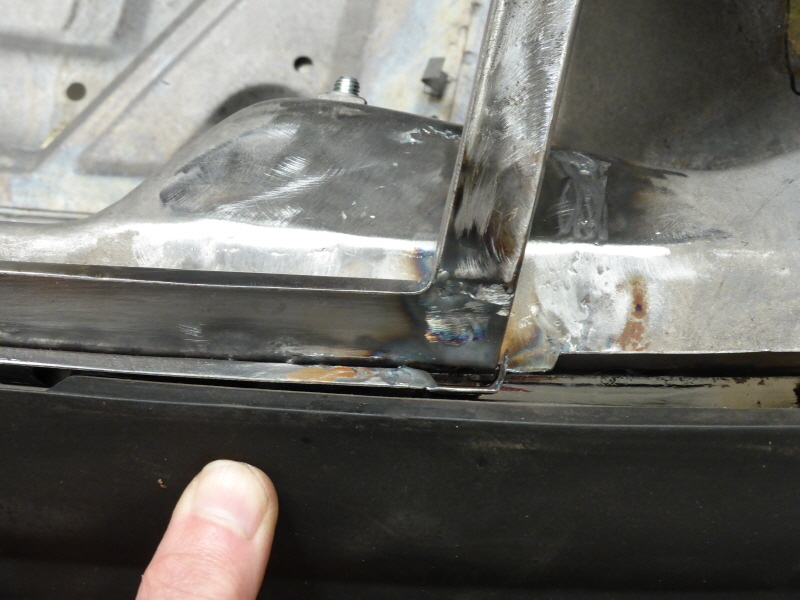
Fog light weld nuts ready to install, with access only from the front:
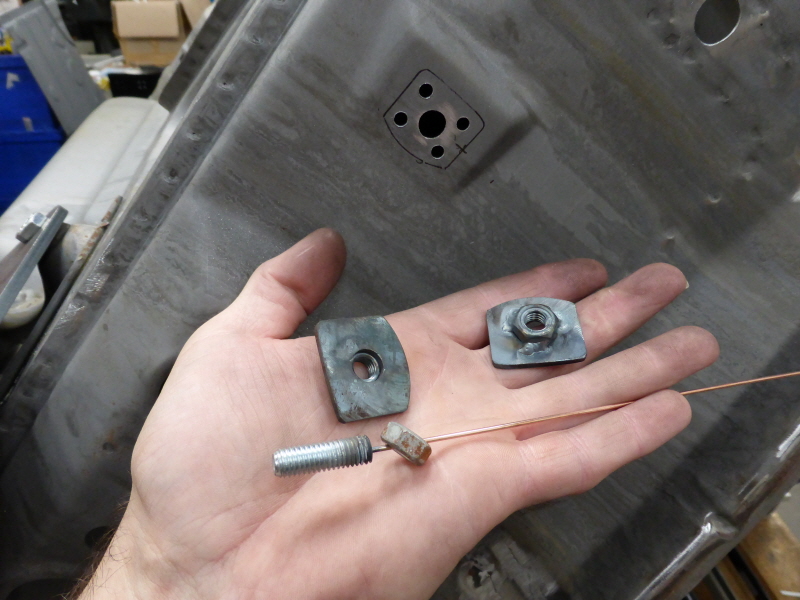
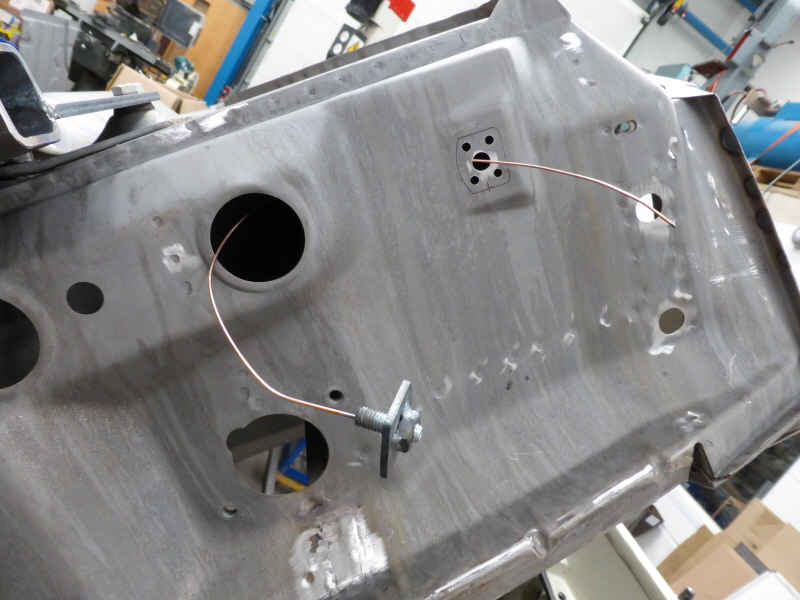
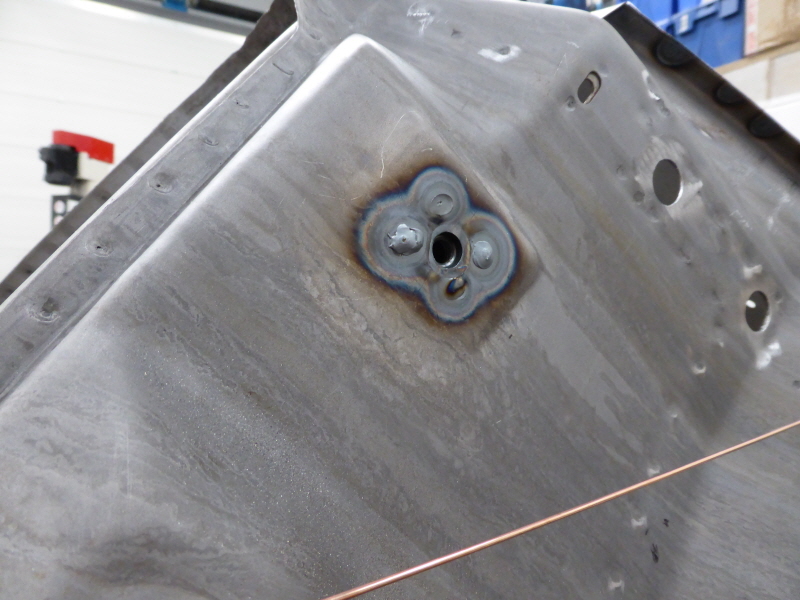
Time to actually start the bodywork. I've started at the front end, with the bonnet seal lip repairs and early bumper conversion mods. The idea was to use these fiddly bits as tig welding practice, as I've never tig'ed bodywork before. Hopefully that way I'll be half decent at it before attempting more daunting task of butt welding in the GT arches in with minimal distortion. Replacing these rusty buts with new steel:
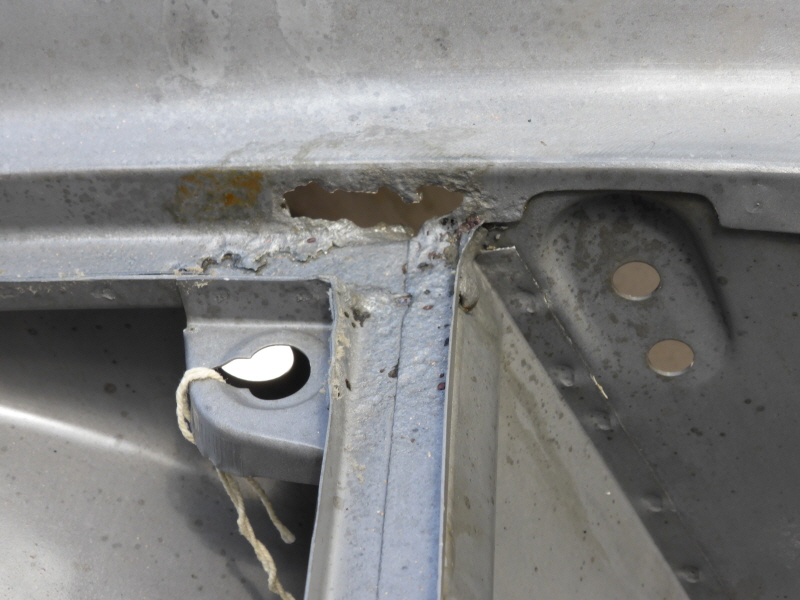
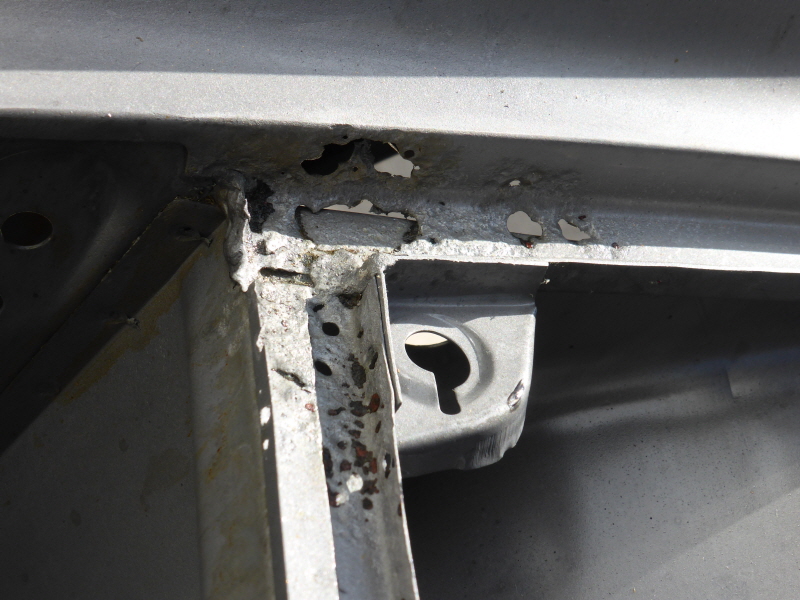
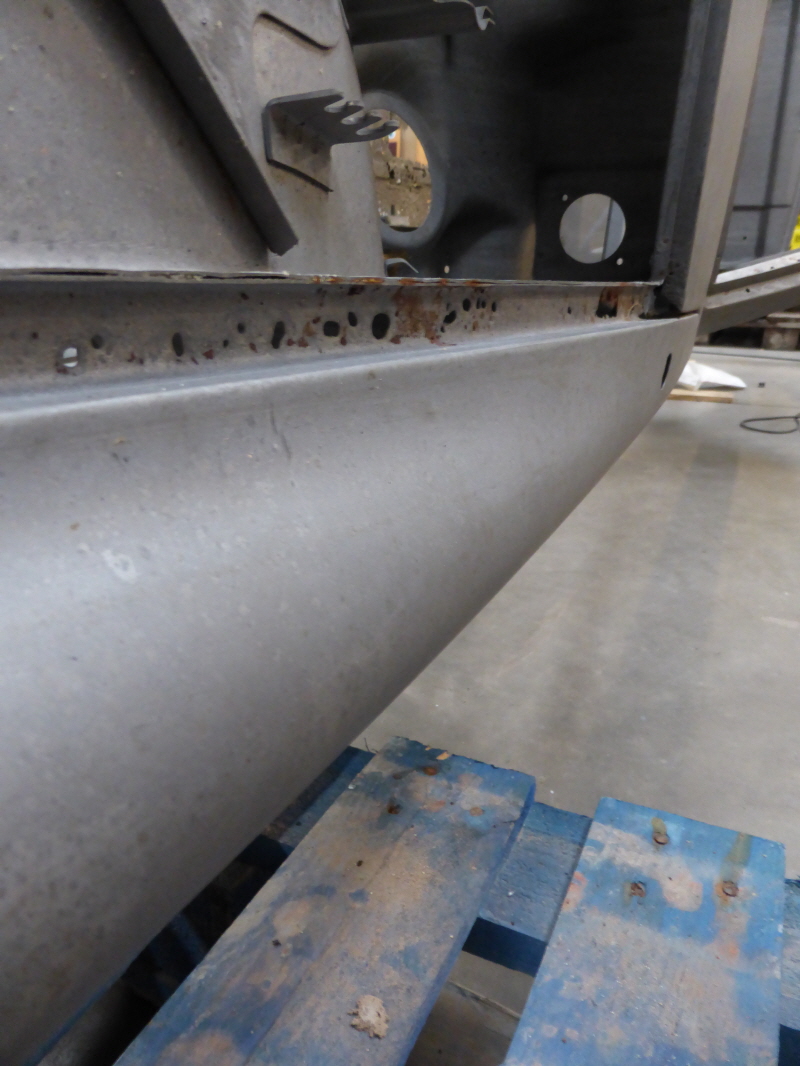
The cutting and spot weld drilling begins:
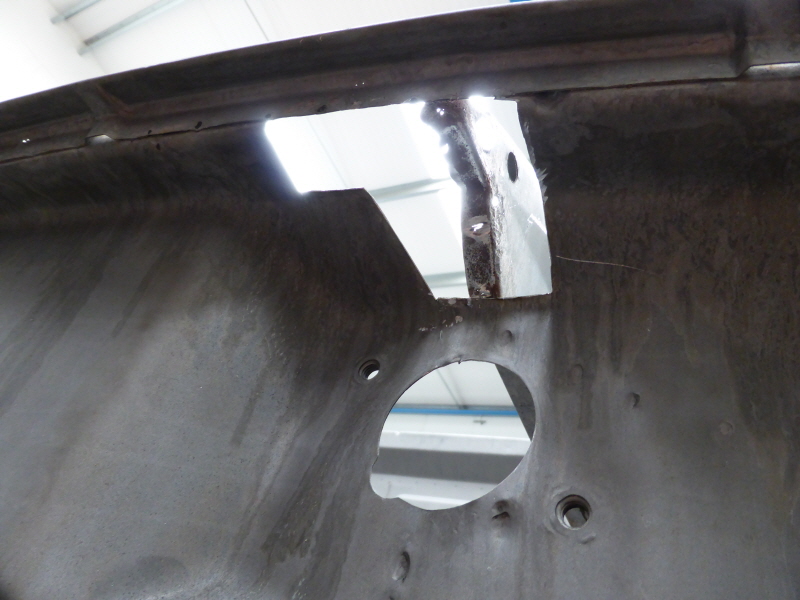
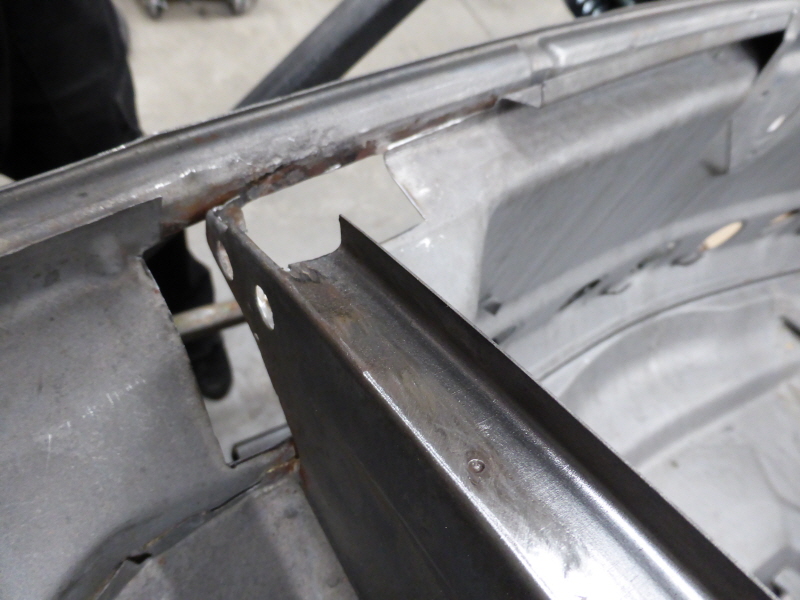
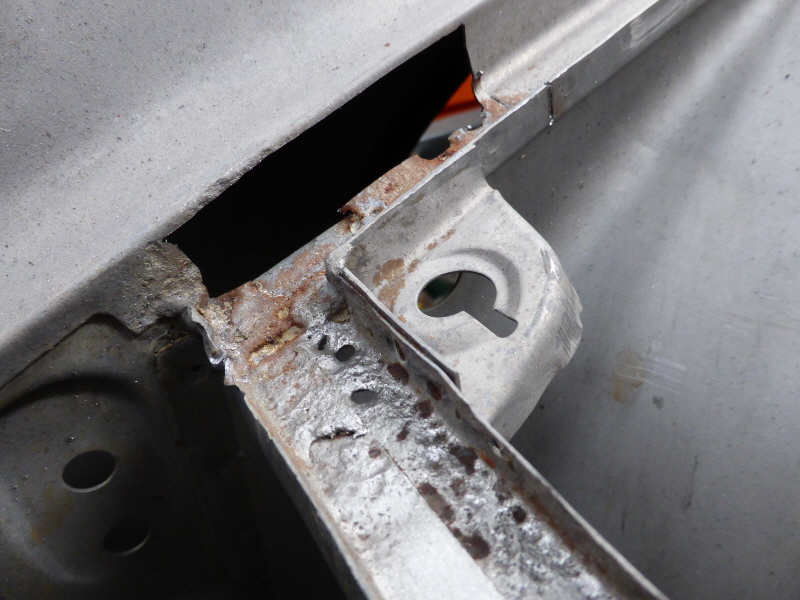
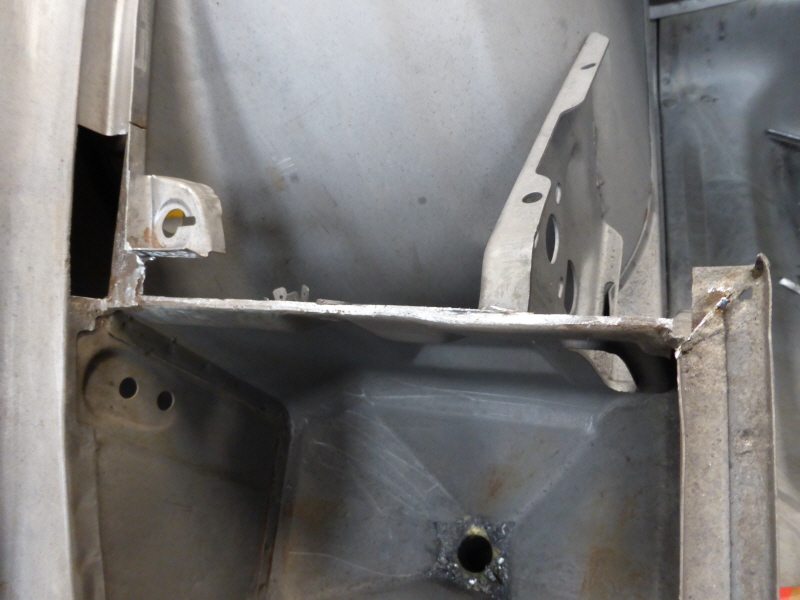
This was a pain to remove. Not wanting to damage the lip at the top of the inner wing (the new channel will be spot welded back in) meant grinding the spot welds out from inside the weather strip channel with a 3” grinding disc. Very tedious. At least cutting along the other side with a reciprocating saw was easy:
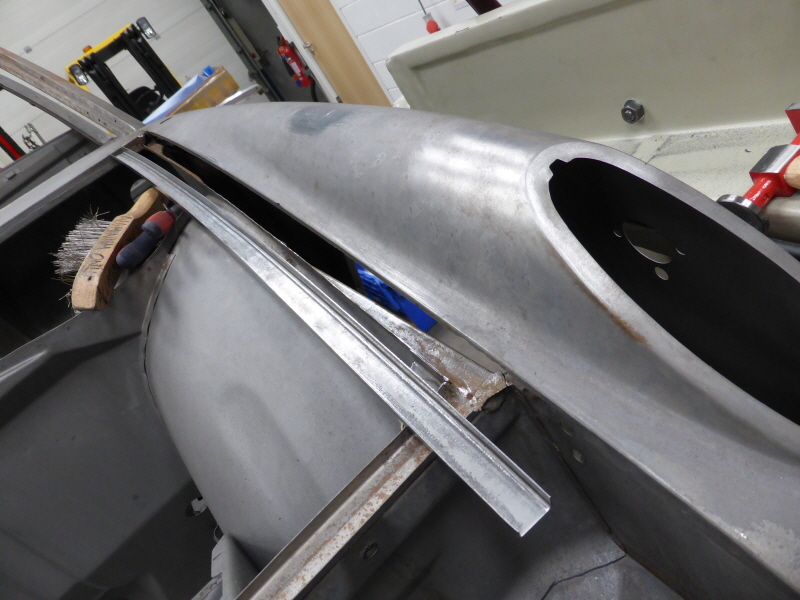
….and the fabricating:
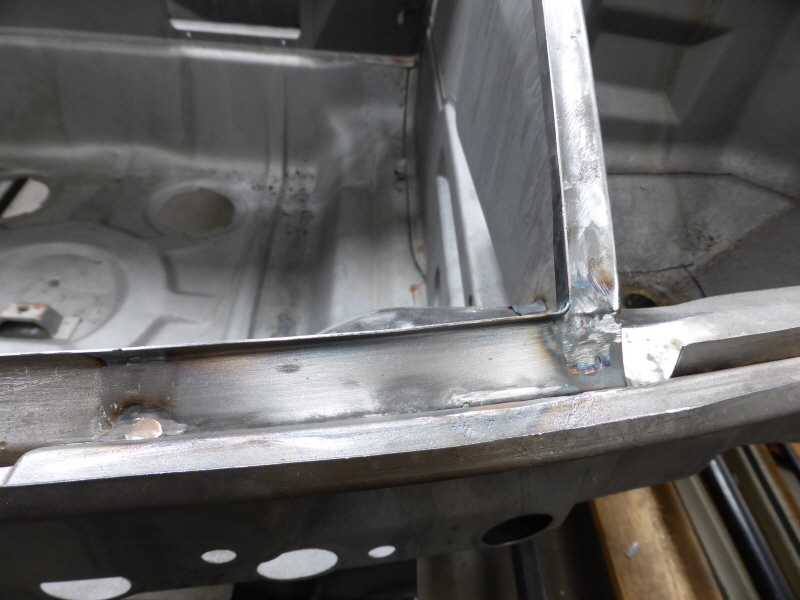
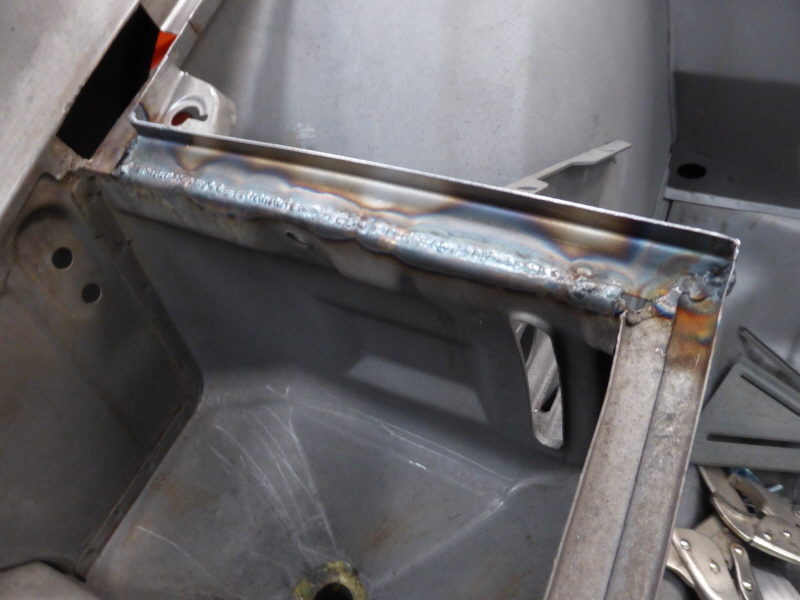
It seems Porsche / Karmann thought water flows uphill when designing the 914 bonnet weather seal channel, and the rust at all of the low points, even on a car which has spent all of its life in California or indoors in the UK, proves that it doesn’t. I have some mods planned to make sure water won’t be able to collect here again once it’s finished. As part of the early bumper conversion, I needed to at least remove the impact bumper retaining strip in front of the pop up lights:
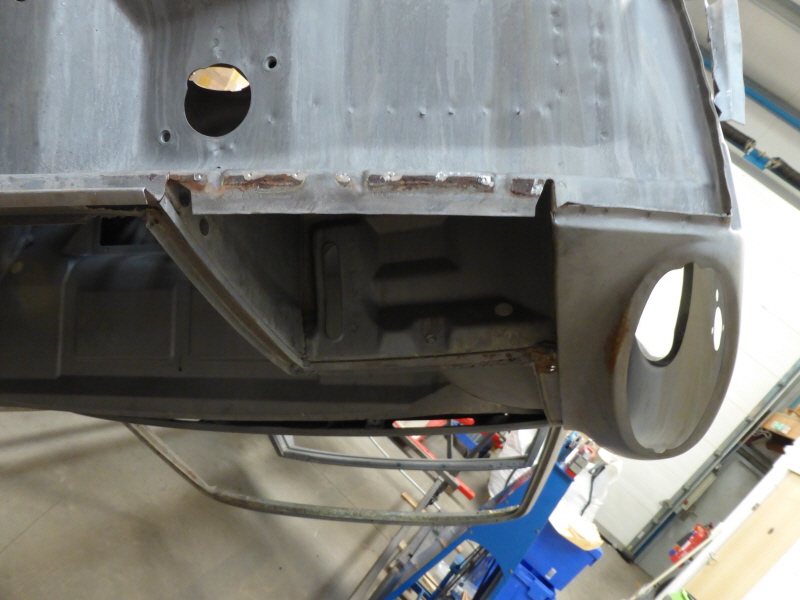
Welding up the marks left by the spot weld drill:
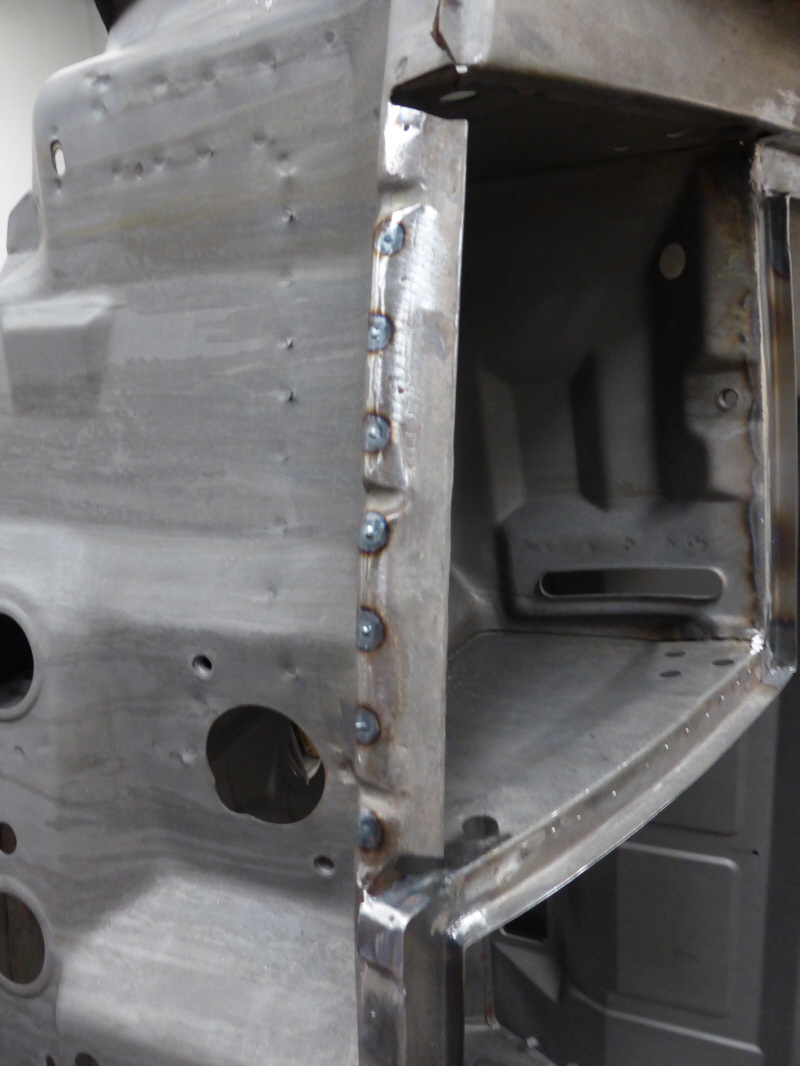
………. and cut it back along the front of the bonnet to resemble the weather strip channel on an early model. I thought about removing all of it, and replacing it with a 90 degree channel, like on the early models, however, this just introduced more undrained low spots. I decided to make the weather seal channel edge from the centre part of the impact bumper retaining strip, as it has 3 drainage channels (so not all of the impact bumper modifications on late models were bad!), and also to move the 2 other drainage channels which were originally in front of each headlight to the corners of the new weather strip channel edge:
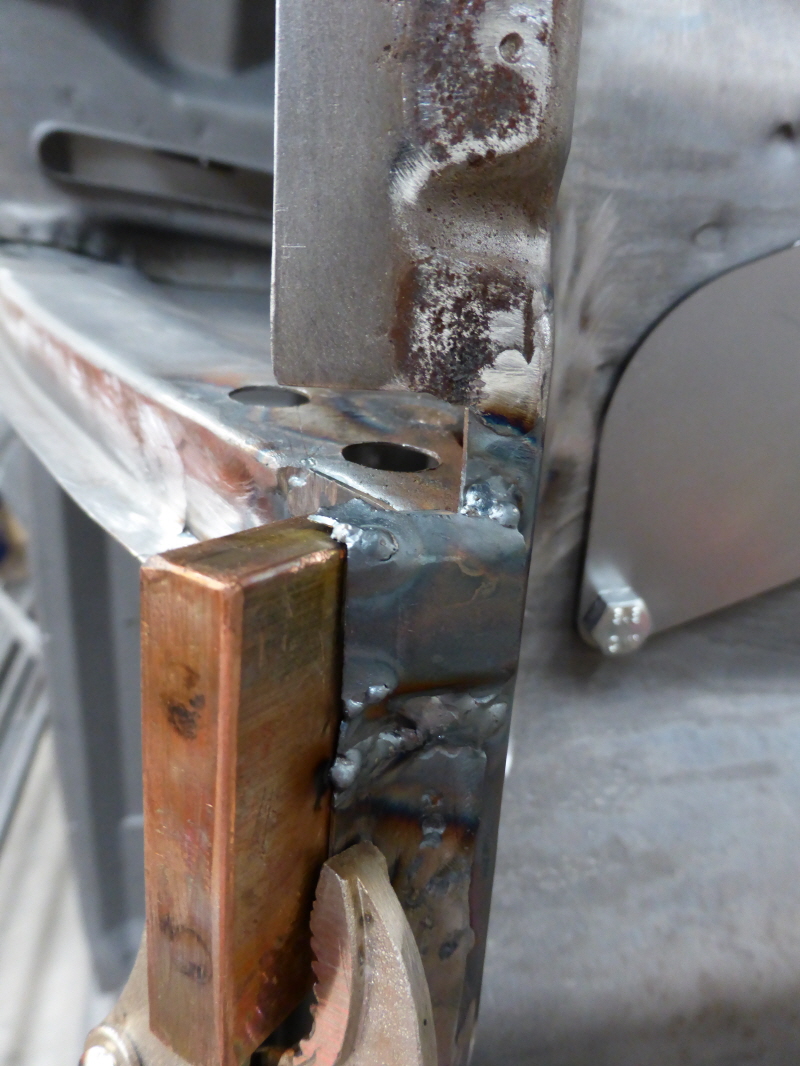
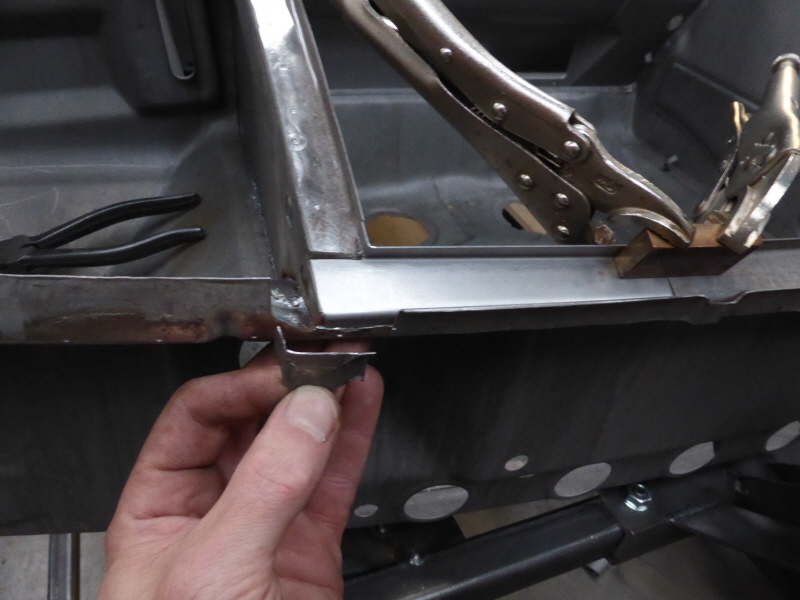
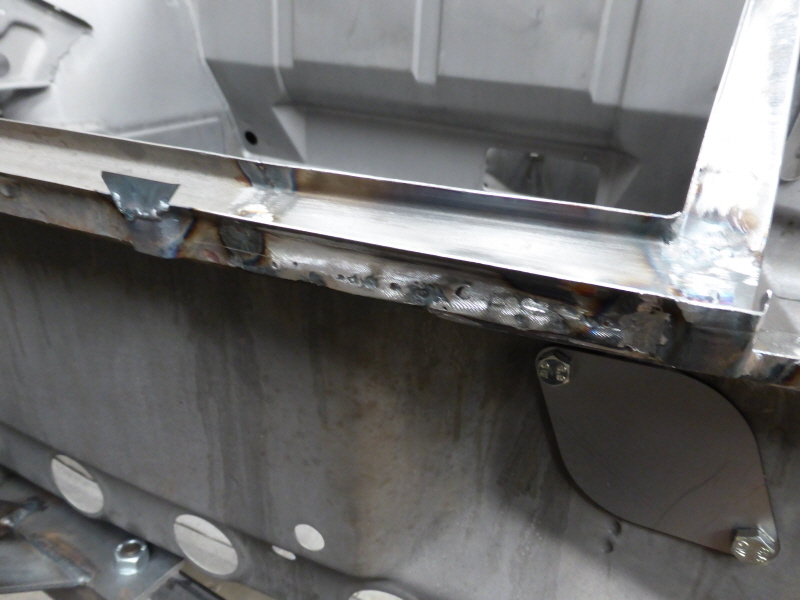
The two yellowish spots in the weld are where I’ve used silicone bronze tig wire to fill very localised pitting. Generally only where a tiny rust spot had left either very thin steel or a pinhole, and where cutting it out and welding a a new piece of steel would be more work, and not result in as neat an end result. I’d experimented with this (having never used silicone bronze before) on some very rusty remains of the floor, with good results:
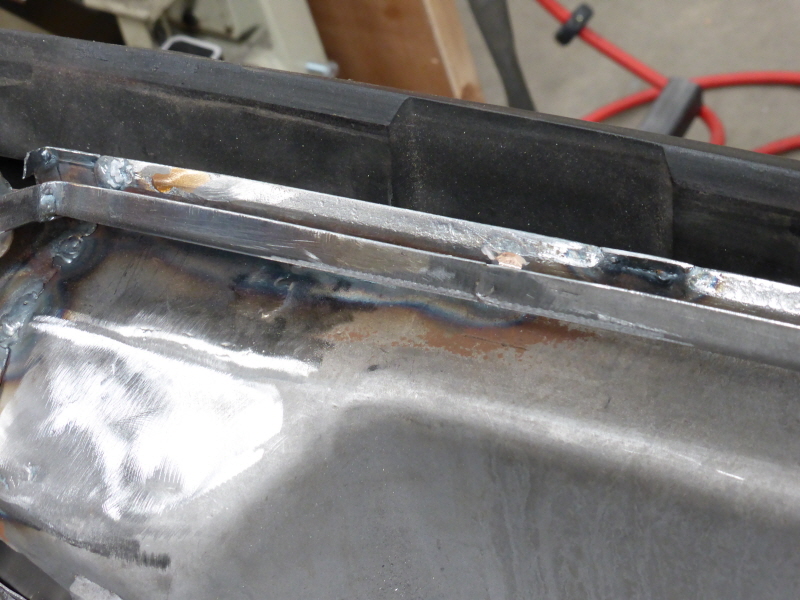
My first go at spot welding bodywork:
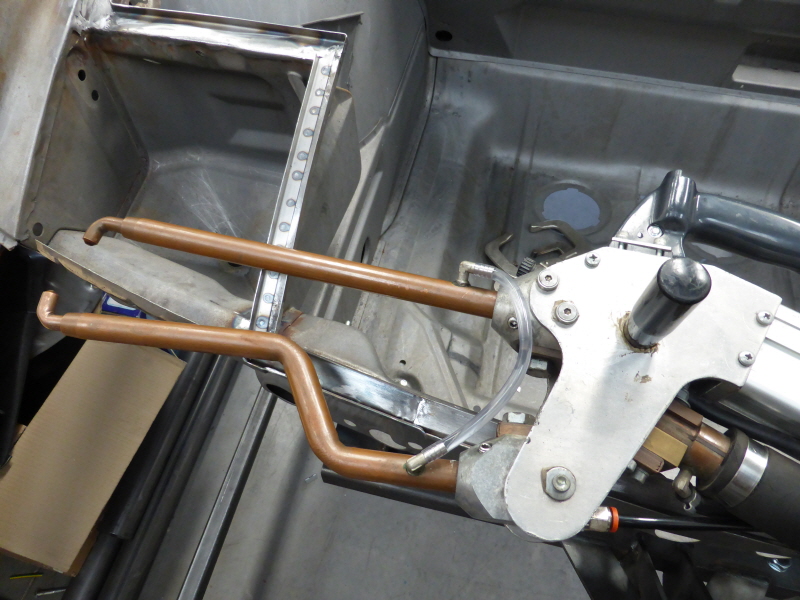
The weather seal channel repairs finished on one corner. I added 2 more drainage slots to the new channel edge at the rear of the headlight too:
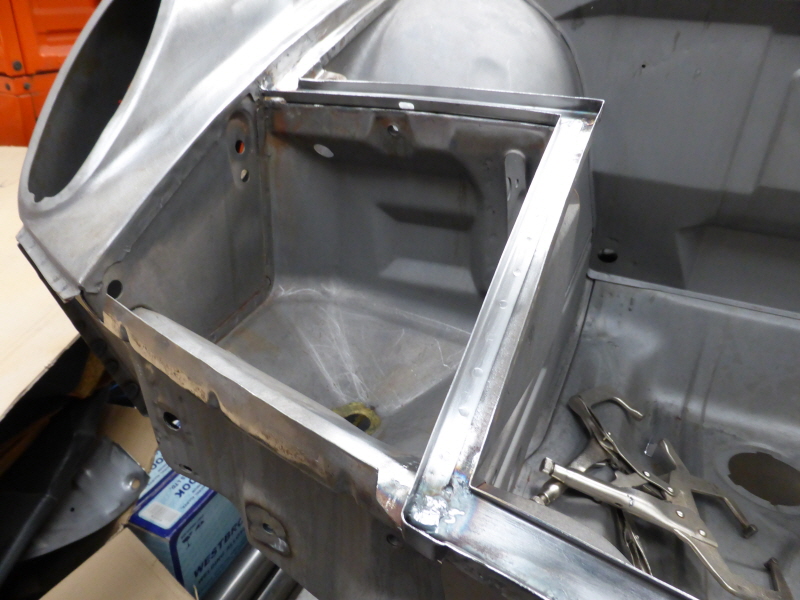
Removing the impact bumper retaining strips at the sides of the bumper:
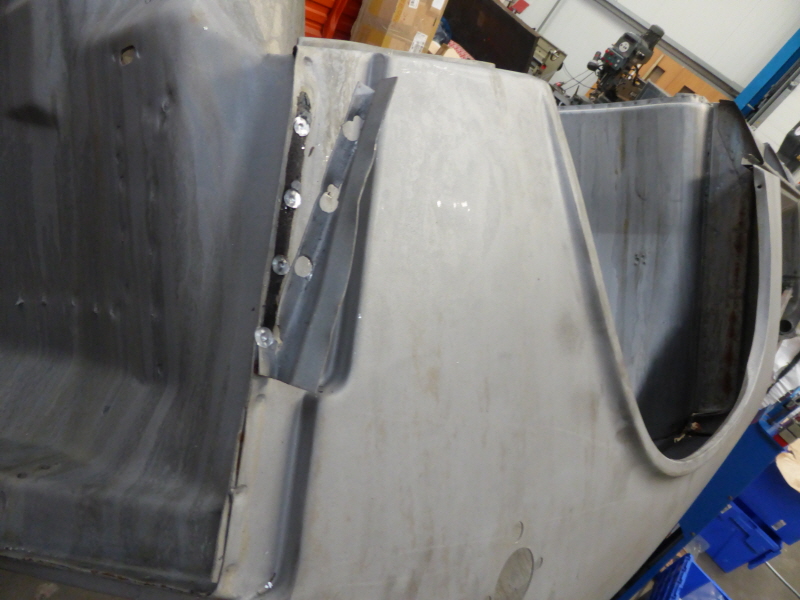
Trial fitting the early bumper mount reinforcing plates I made. I won’t weld them in until the wings are cut for the GT arches, as the access will be much better then. I messed up by copying the hole pattern for the plug welds to the inner wing from an early car, without realising the inner wing pressing is different on a late model. Of the 13 holes in the bracket, 7 of them have no steel behind them to weld to. I’ll either modify or re-make them to better suit the late model inner wings before they get welded on:
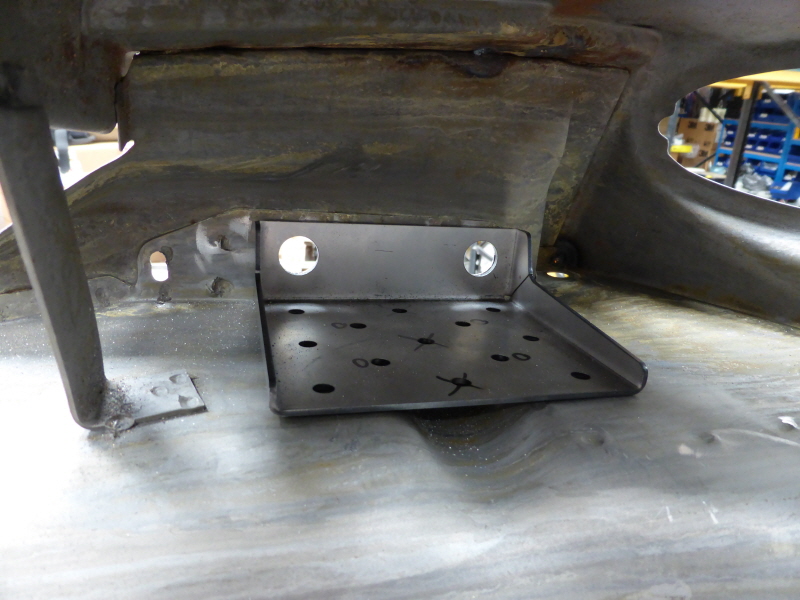
Going to trial fit the early bumper for the first time, I found that the RH fog light / horn grill nowhere near fitted the bumper. Strange, as they both appear to be original parts. I had to grind the bumper quite a bit to make enough room. Very pleased the extortionate prices put me off having the bumpers rechromed last year, as having to make more clearance for the grilles after spending so much on rechroming would have been unbelievably annoying:
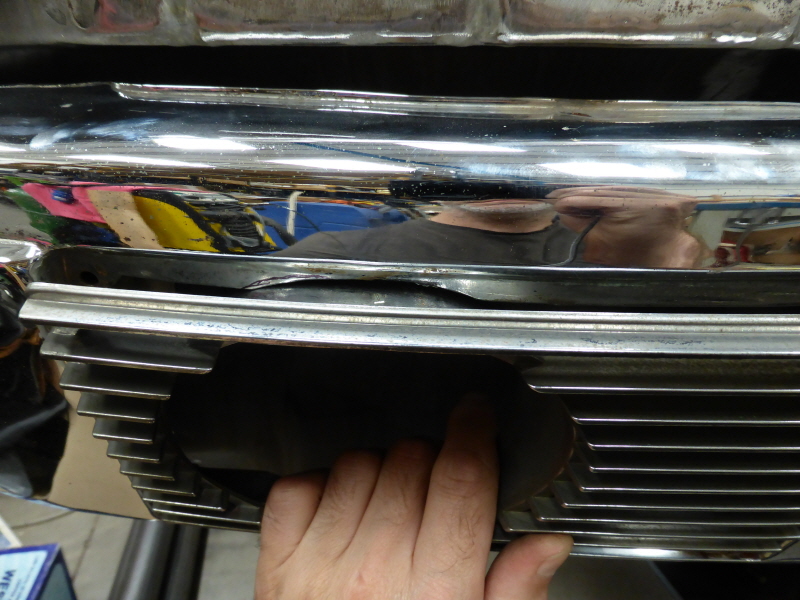
The early bumper bolted up for the first time. Sounds silly, as I know what an early model looks like, but it’s very satisfying seeing my late model start to look like one:
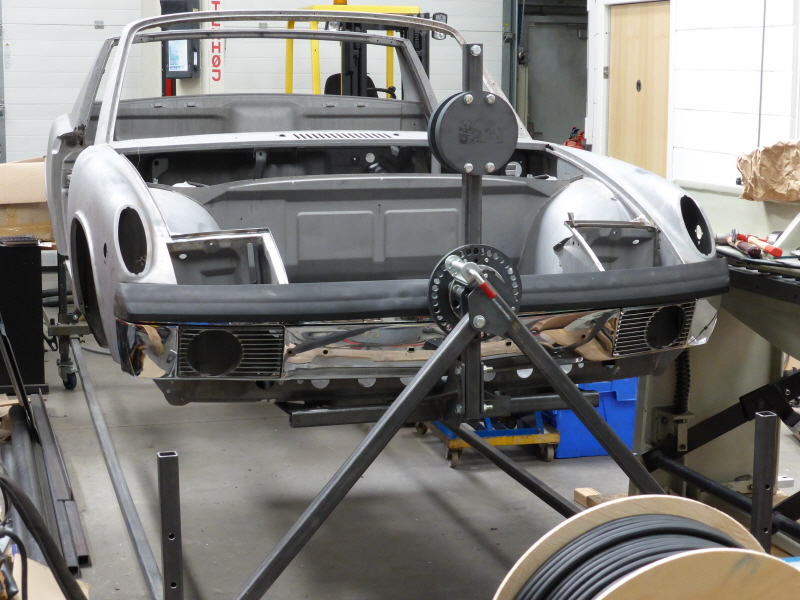
Hopefully the drainage channels I’ve added along the front of the weather seal channel won’t interfere with the fit of the bumper top. Unfortunately I can’t do a proper trial fit until the body is off the rotisserie, as I haven’t left enough space to trial fit the rubber top without it hitting the rotisserie:
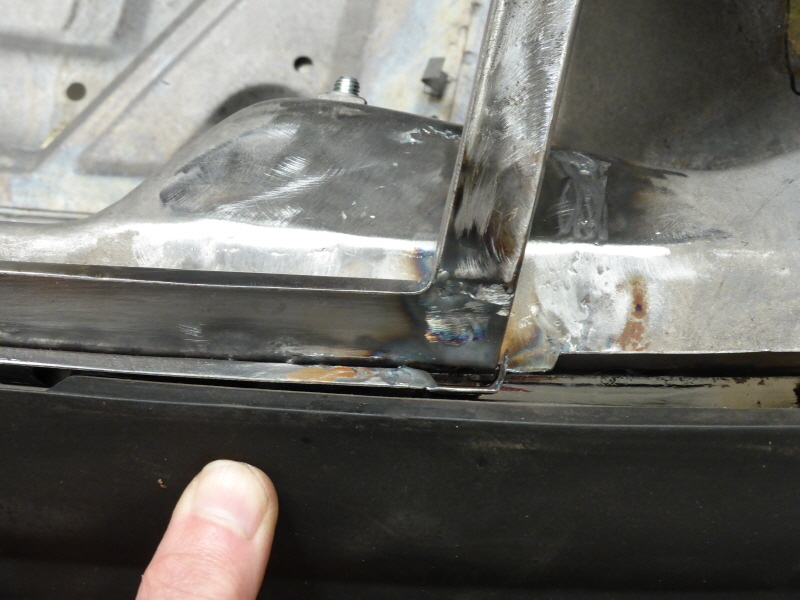
Fog light weld nuts ready to install, with access only from the front:
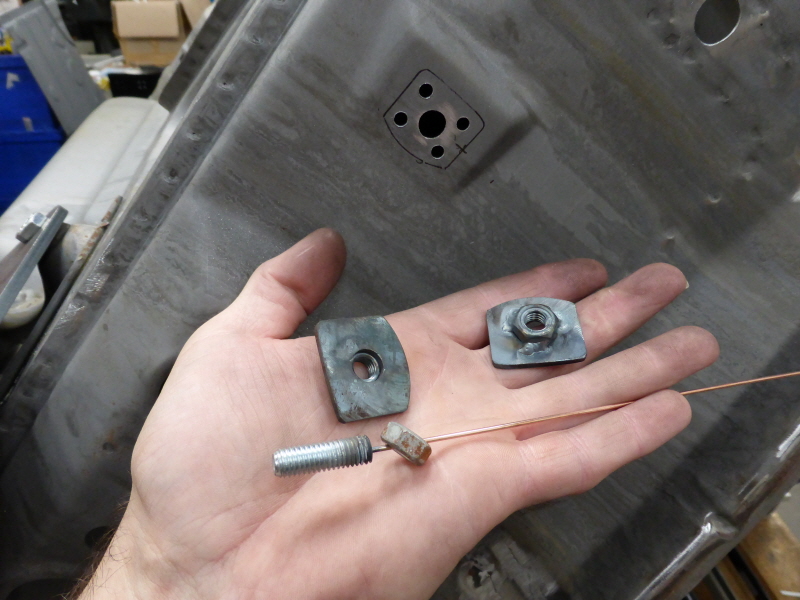
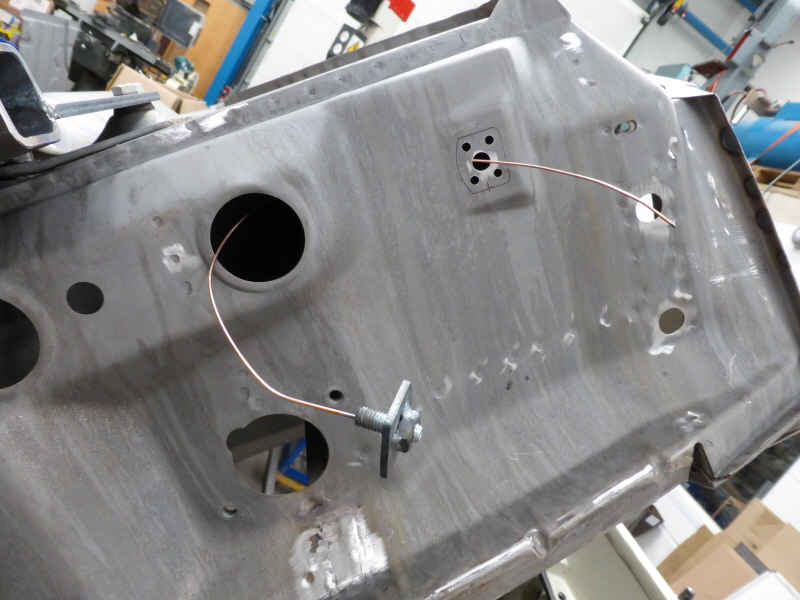
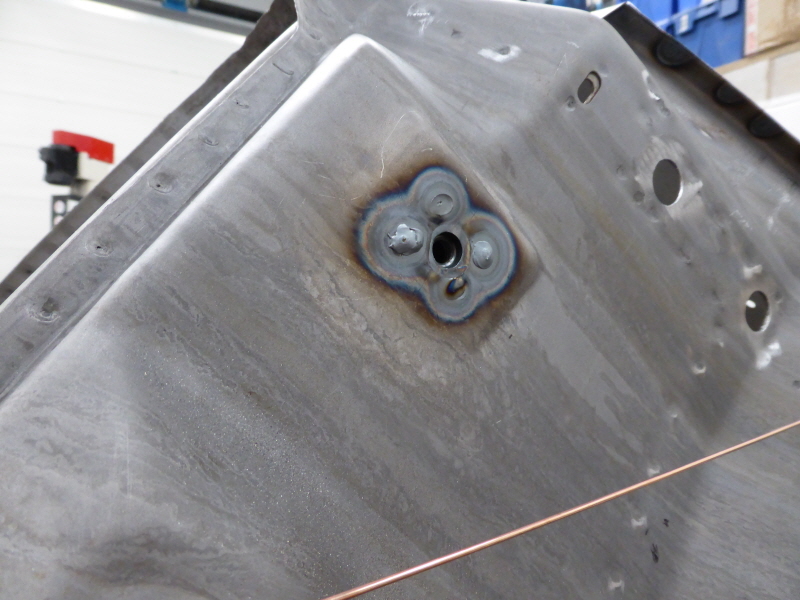
Regards,
RichardJ
1975 California spec 914 1.8 restoration project
RichardJ
1975 California spec 914 1.8 restoration project
- Bootsy
- Site admin and the Boss
- Posts: 23904
- Joined: Sat Nov 08, 2003 6:09 pm
- Location: Norwich
- Contact:
Re: 1975 914 1.8 Restoration
Wonderful stuff
1972 911T | 1994 993 Carrera | 1999 986 Boxster | 1990 T25 Camper
Vintage Heuer, Omega, Zenith and other vintage watches - http://www.heuerheritage.co.uk
Vintage Heuer, Omega, Zenith and other vintage watches - http://www.heuerheritage.co.uk
-
- Put a fork in me, I'm done!
- Posts: 1717
- Joined: Sat Aug 05, 2006 7:02 pm
- Location: Rochford, Essex
Re: 1975 914 1.8 Restoration
I bought a new set of fog light grills from Porsche a few years ago when they were still available. My right hand one didn't fit either.RichardJ wrote:
Going to trial fit the early bumper for the first time, I found that the RH fog light / horn grill nowhere near fitted the bumper. Strange, as they both appear to be original parts. I had to grind the bumper quite a bit to make enough room. Very pleased the extortionate prices put me off having the bumpers rechromed last year, as having to make more clearance for the grilles after spending so much on rechroming would have been unbelievably annoying:
Nice work on the repairs, did them all myself last year on my project.
Re: 1975 914 1.8 Restoration
Thanks. How strange about the genuine RH grills not fitting. No idea of the history of mine other than that they are pretty old from the state of the chrome, I bought them on US ebay with all the fog light parts. I had to grind about 3mm out at one end of the radius at the top of the bumper cutout, and maybe 1mm at the bottom too before the RH grill fitted. The LH one fitted perfectly.
Stephen, I was following your thread very closely last year and the other good 914 build threads on here, seeing what I had let myself in for in terms of the body repairs! I've not been following any of them as much lately due to not having time, but I'll be making an effort to now I'm actually making some progress. Thanks for the inspiration!
Stephen, I was following your thread very closely last year and the other good 914 build threads on here, seeing what I had let myself in for in terms of the body repairs! I've not been following any of them as much lately due to not having time, but I'll be making an effort to now I'm actually making some progress. Thanks for the inspiration!
Regards,
RichardJ
1975 California spec 914 1.8 restoration project
RichardJ
1975 California spec 914 1.8 restoration project
Re: 1975 914 1.8 Restoration
Amazing to me the exceptionally high quality of work being done here and on Defianty's and others' projects. Thirty years ago reading Practical Classics I'd never have imagined guys working at home would be using rotisseries, doing this calibre of metal work etc. No more mesh and Plastic Padding. The bar keeps being raised. Lovely job. John.
Re: 1975 914 1.8 Restoration
Thanks. Without any doubt it is the other 914 restoration thread on here which have motivated me to learn to tig and spot weld bodywork, rather then just miging everything, and to change the objective of my project to attempting to do a good job, rather than just an average one. Watching what must be hundreds of hours of Youtube welding and metal shaping videos helped too.
20 odd years ago I had to do a course to master tig welding aluminium as I was getting nowhere trying to teach myself. These days it would be relatively easy for someone to teach themselves, as there are so many very good Youtube videos on welding (weldingtipsandtricks being my favourite welding channel).
20 odd years ago I had to do a course to master tig welding aluminium as I was getting nowhere trying to teach myself. These days it would be relatively easy for someone to teach themselves, as there are so many very good Youtube videos on welding (weldingtipsandtricks being my favourite welding channel).
Regards,
RichardJ
1975 California spec 914 1.8 restoration project
RichardJ
1975 California spec 914 1.8 restoration project